KB Electronics KBMK-24DF User Manual
Page 42
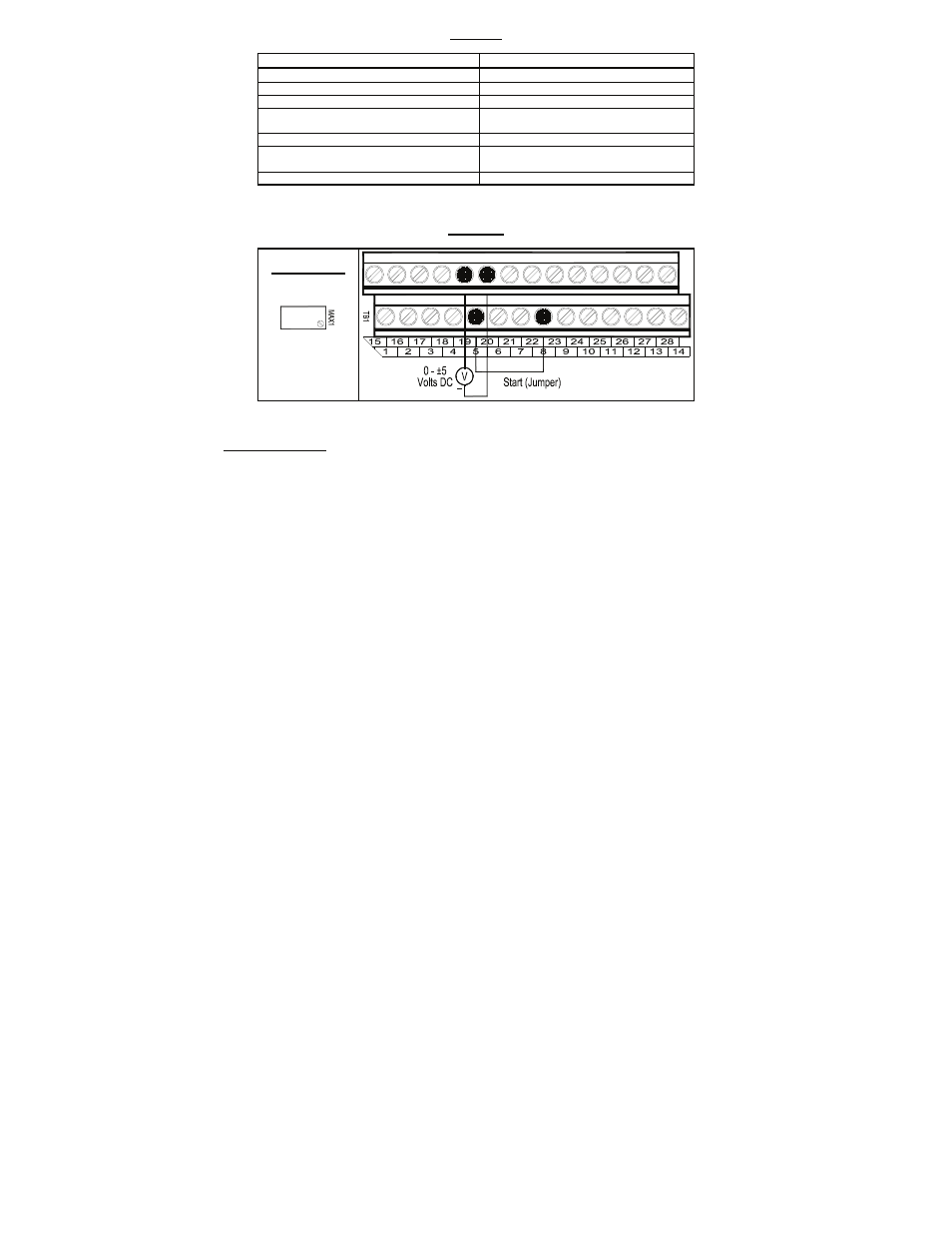
42
TABLE 23
ANALOG INPUT "1" SIGNAL VOLTAGE FOLLOWING PROGRAMMING
Function No.
Code/Range
2.00: Frequency Control 0002:
Analog Signal 1
9.00: Analog Input 1 Gain 0
–
500:
Set to the Desired Gain
7.04: Multi-Function Input Terminal 5
0010: N.O. Start*
9.01: Analog Input 1 Slope
0000: Positive
0001: Negative
9.02: Analog Input 1 Offset 0
–
100:
Set to the Desired Offset
9.03: Analog Input 1 Type
0000: Unidirectional
0001: Bidirectional
9.04: Analog Input 1 Response Time (mSec) 2 – 100: Set to the Desired Time
*Factory setting.
FIGURE 32
ANALOG INPUT "1" SIGNAL VOLTAGE FOLLOWING CONNECTIONS
MAX1 Trimpot
+
ANALOG INPUT "2"
See Table 24, on page 43, for Analog Input 2 electrical ratings.
Voltage Signal Input: Set Jumper J1 to the "VOLT" position (factory setting).
Current Signal Input: Set Jumper J1 to the "CUR" position.
PWM Signal Input: Set Jumper J1 to the "VOLT" position (factory setting).
Connect the signal input to Terminal "21" and the common to Terminal "22". Connect the Start (Jumper) to
Terminal "5", which is factory set for N.O. Start ("0010") and to any available common terminal ("8", "12", "14",
"16", "18", "20", "22"). See Table 25, on page 43, for drive programming. See Figure 33, on page 43, for
connections.
MAX2 Trimpot: If the Analog Input 2 signal voltage is higher than the input signals specified in Table 16, on
page 30, use Trimpot MAX2 to attenuate it. Apply the maximum signal input and set the drive for full speed
output and observe the display. Rotate Trimpot MAX2 counter clockwise until the drive output frequency
begins to drop. Then rotate Trimpot MAX2 clockwise until the display returns to the maximum output
frequency. Set the signal slope and adjust the gain, offset, and response time as desired.