3 alarms, causes and actions – IAI America ACON-CY User Manual
Page 107
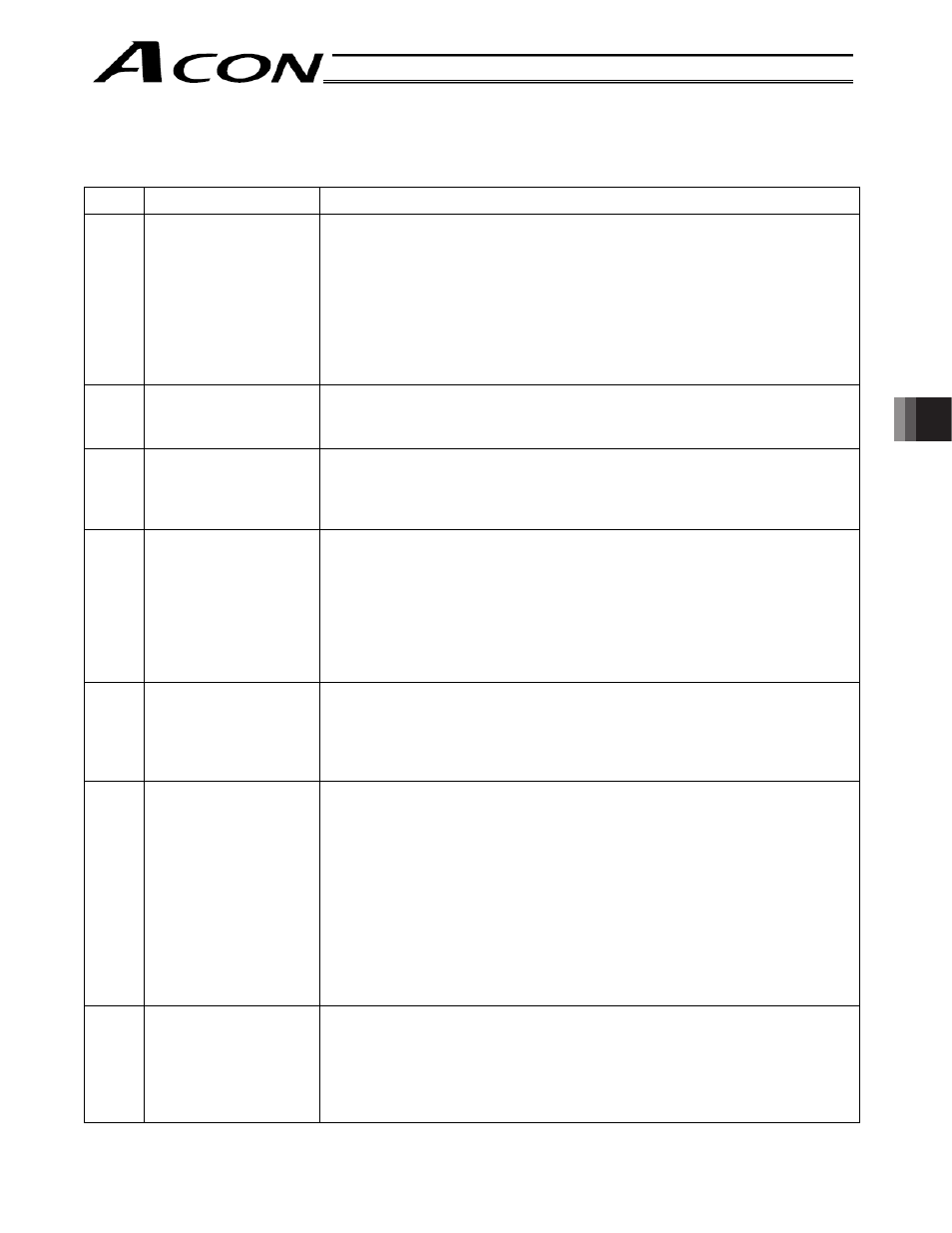
95
7. T
roubleshooting
7.3
Alarms, Causes and Actions
(1) Operation Cancellation Alarms
Code Error
Cause/action
0A2
Position data error
Cause: [1] A move command was input when a target position was not yet
set in the “Position” field.
[2] The target position in the “Position” field is outside the soft limit
range.
[3] A target position was specified as a relative coordinate in the
“Position” field in solenoid valve mode 0.
Action: [1] Set a target position first.
[2] Change the target position to a value inside the soft limit range.
[3] Specify the target position as an absolute coordinate.
0A3 Position
command
information data error
Cause: The speed or acceleration/deceleration at the value command
exceeded the maximum setting value.
Action: Change to the appropriate value.
0B5
Phase-Z position error
The position at which the phase-Z was detected at homing was outside the
specified range.
Cause: Encoder error
Action: Contact IAI.
0BA
Home sensor not yet
detected
This alarm indicates that the actuator equipped with a home check sensor did
not complete homing successfully.
Cause: [1] The load contacted peripheral equipment during the homing.
[2] The slide resistance of the actuator is large in some areas.
[3] The home check sensor is not installed properly, or the sensor
is faulty or its circuit is open.
Action: If the load is not contacting any peripheral equipment, [2] and [3] are
suspected. Contact IAI.
0BE
Homing timeout
Cause: After the start of homing, homing does not complete after elapse of
the time set by the manufacturer’s parameter. (This alarm does not
generate during normal operation.)
Action: As one possible cause, the controller and actuator combination may
be incorrect. Contact IAI.
0C0
Excessive actual speed Cause: The motor speed exceeds the maximum speed set by the
manufacturer’s parameter.
This alarm does not generate during normal operation, but it may
occur if the load decreased before a servo error was detected and
the motor speed has increased as a result. This condition occurs
due to the following reasons:
[1] The slide resistance of the actuator is large in some areas.
[2] The load increased due to momentary application of external
force.
Action: Check the assembly condition of mechanical parts for any
abnormality. If the actuator itself is suspected as the cause, contact
IAI.
0C9 Excessive
motor
power-supply voltage
This alarm indicates that the voltage of the motor power supply is excessive
(24 V + 20%: 28.8 V or above).
Cause: [1] The voltage of the 24-V input power supply is high.
[2] Faulty part in the controller
Action: Check the input power-supply voltage.
If the voltage is normal, contact IAI.