FEC AFC1500 User Manual
Page 32
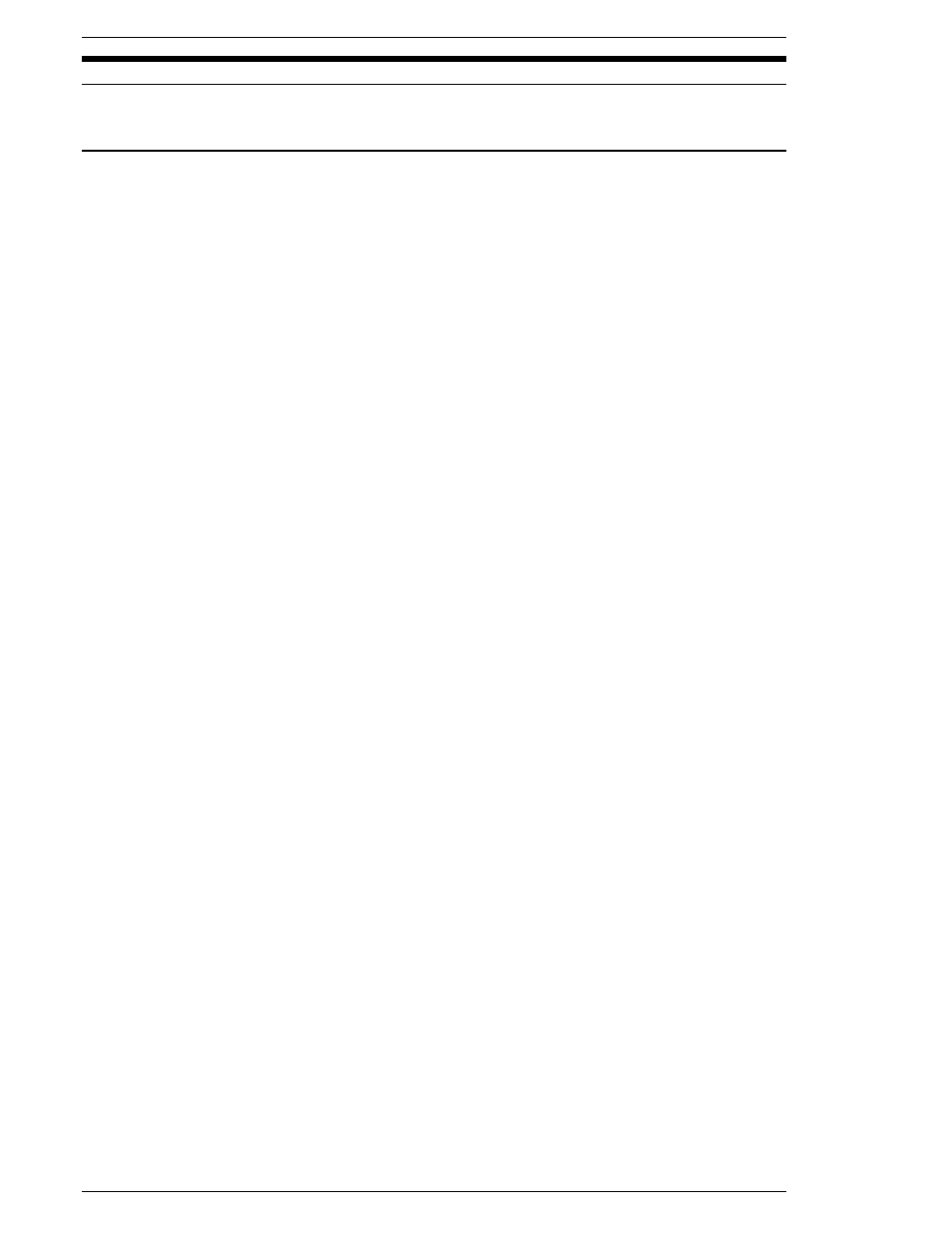
Chapter 3: System Description
Page 3-2
3.1
System Block Diagram
3.1.1 Multi System Block Diagram Description
{
Spindles can be configured as stand alone units (with independent I/O) or combined in a
multiple spindle configuration controlled by one main controller (Multi Unit) using one set of
I/O to control the group of spindles. This configuration is referred to as a “Multi System”.
{
In a Multi System, communication and spindle control for up to
31
SAN Units (Spindle Con-
trollers) is accomplished through the Multi Unit via an
RS485
Daisy chain connection on the
front of each Axis unit.
{
Spindle programming / monitoring is accomplished through either a detachable Laptop PC
or an embedded HMI PC, running the AFC User Console software package, for simultaneous
uploading / downloading of up to 31 spindles.
{
A “Hot -Swap” detachable keypad/display can be used on each SAN Unit to monitor the in-
dividual spindle status.
{
The use of a Multi Unit provides one set of PLC I/O for controlling multiple spindle fasten-
ing operations. Fieldbus interfaces are available for direct connection to networks such as
Profibus, DeviceNet, AB Remote I/O, CCLink, Ethernet I/P, etc.
{
Discrete 24 VDC (Sinking) I/O on the SAN unit provides direct communications with the
PLC for limited individual spindle control when the system is configured with a Multi Unit. The
individual spindle I/O can provide individual spindle status when required.
{
Dedicated communications with the system is provided via communications ports available
directly on the Multi Unit. Once configured, the system is not dependent on a PC or software
package to receive or transmit data from/to an external device.
{
A detachable or embedded PC running the AFC User Console software can be connected
to the Multi Unit for increased data communications or manipulation capabilities.