Field wiring, 6a o & m : 6, Two wire connection when using a 2/3/4 wire device – Bray 6A Series O&M Manual User Manual
Page 6: Three/four wire, Hart, Profibus da/dp, foundation fieldbus
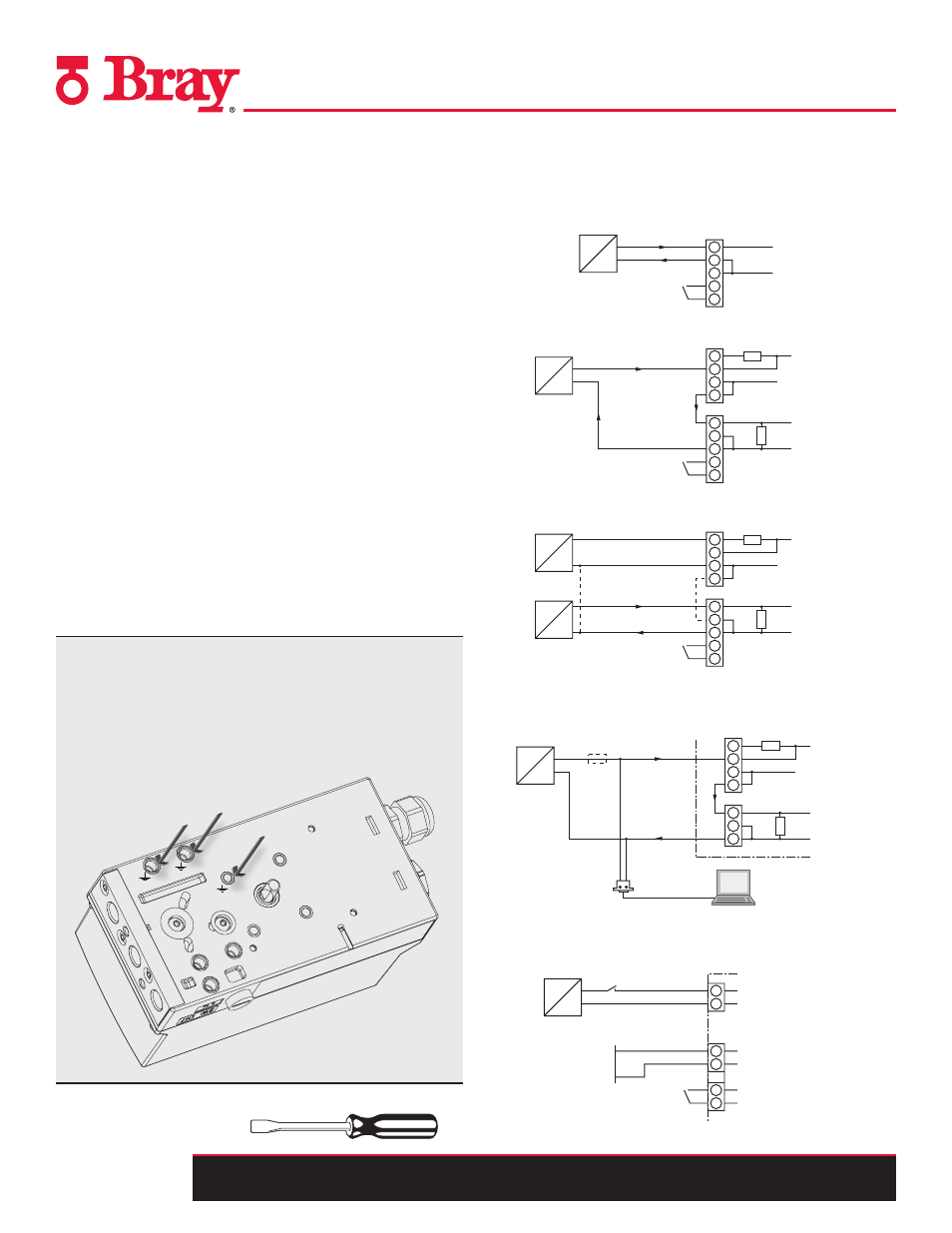
All information herein is proprietary and confidential and may not be copied or reproduced without the expressed written consent of BRAY INTERNATIONAL, Inc.
The technical data herein is for general information only. Product suitability should be based solely upon customer’s detailed knowledge and experience with their application.
Series 6A Operation & Maintenance – field Connections
6A O & M : 6
fIelD WIrInG
Each S6A is provided with two conduit entries for power/incom-
ing analog signal of the main unit and any optional modules.
Please refer to the wiring diagrams referenced in this docu-
ment when connecting the positioner and any optional modules.
It is essential to install the optional modules before connect-
ing the positioner electrically. Refer to the following “Technical
Description” portion of this manual for relevant power distribu-
tion sizing information when installing a S6A positioner and its
optional modules.
Safety Notes:
• Local regulations regarding hazardous environments must be
followed when installing this device in a hazardous location.
• The conduit connections must be properly sealed to maintain
the weatherproof integrity of the actuator enclosure.
• Never connect the current input (terminals 6 and 7 as shown
on the diagrams to the right) to a power source; the positioner
will probably be destroyed in that case. Always use a current
source with a maximum output current of I = 20 mA.
• To maintain auxiliary power, the input current must be a min-
imum of 3.6 mA.
Note: The plastic enclosure is metallized from inside to
increase the electromagnetic compatibility (EMC) with
respect to high-frequency radiation. The shield is connected
to the threaded bush shown in Figure 1 such that it is elec-
trically conductive. This protection is effective only if you
connect at least one of the bushes to the grounded control
valves through electrically conductive (bare) attachments.
Figure 1
1.
2.
3.
Tools Needed:
• Instrument Screwdriver
I General Area
1. Two Wire
4 ... 20 mA
BE1 = Binary Input
7
8
9
10
+
–
J
6
Input for safety shutdown (activated using coding jumper)
1)
≤ 30 V
≤ 24 V
+
–
BE1 = Binary Input
7
9
10
+
–
6
1)
81
82
Input for safety shutdown (activated using coding jumper)
1)
≤ 24 V
–
BE1 = Binary Input
7
9
10
+
–
6
81
82
HART
modem
PC/Laptop
R 250 W if req.
1)
3
Only required with current sources not conforming to HART
1)
2
3
4
5
+
–
I
l
y
= 4 ... 20 mA
6
7
8
l
W-
l
H+
1) Jumper between 5 and 7 only for three-wire system
2
3
4
5
+
–
J
6
7
8
9
10
4 ... 20 mA
0/4 ... 20 mA
2
3
4
5
+
–
6
7
8
9
10
18 ... 30 V
J
+
–
BE1 = Binary Input
BE1 = Binary Input
1)
Power Supply
Non-Hazardous
Hazardous area, Zone 1
2. Two Wire Connection When Using a 2/3/4 Wire Device
4 ... 20 mA
BE1 = Binary Input
7
8
9
10
+
–
J
6
Input for safety shutdown (activated using coding jumper)
1)
≤ 30 V
≤ 24 V
+
–
BE1 = Binary Input
7
9
10
+
–
6
1)
81
82
Input for safety shutdown (activated using coding jumper)
1)
≤ 24 V
–
BE1 = Binary Input
7
9
10
+
–
6
81
82
HART
modem
PC/Laptop
R 250 W if req.
1)
3
Only required with current sources not conforming to HART
1)
2
3
4
5
+
–
I
l
y
= 4 ... 20 mA
6
7
8
l
W-
l
H+
1) Jumper between 5 and 7 only for three-wire system
2
3
4
5
+
–
J
6
7
8
9
10
4 ... 20 mA
0/4 ... 20 mA
2
3
4
5
+
–
6
7
8
9
10
18 ... 30 V
J
+
–
BE1 = Binary Input
BE1 = Binary Input
1)
Power Supply
Non-Hazardous
Hazardous area, Zone 1
3. Three/Four Wire
4 ... 20 mA
BE1 = Binary Input
7
8
9
10
+
–
J
6
Input for safety shutdown (activated using coding jumper)
1)
≤ 30 V
≤ 24 V
+
–
BE1 = Binary Input
7
9
10
+
–
6
1)
81
82
Input for safety shutdown (activated using coding jumper)
1)
≤ 24 V
–
BE1 = Binary Input
7
9
10
+
–
6
81
82
HART
modem
PC/Laptop
R 250 W if req.
1)
3
Only required with current sources not conforming to HART
1)
2
3
4
5
+
–
I
l
y
= 4 ... 20 mA
6
7
8
l
W-
l
H+
1) Jumper between 5 and 7 only for three-wire system
2
3
4
5
+
–
J
6
7
8
9
10
4 ... 20 mA
0/4 ... 20 mA
2
3
4
5
+
–
6
7
8
9
10
18 ... 30 V
J
+
–
BE1 = Binary Input
BE1 = Binary Input
1)
Power Supply
Non-Hazardous
Hazardous area, Zone 1
4. HART
4 ... 20 mA
BE1 = Binary Input
7
8
9
10
+
–
J
6
Input for safety shutdown (activated using coding jumper)
1)
≤ 30 V
≤ 24 V
+
–
BE1 = Binary Input
7
9
10
+
–
6
1)
81
82
Input for safety shutdown (activated using coding jumper)
1)
≤ 24 V
–
BE1 = Binary Input
7
9
10
+
–
6
81
82
HART
modem
PC/Laptop
R 250 W if req.
1)
3
Only required with current sources not conforming to HART
1)
2
3
4
5
+
–
I
l
y
= 4 ... 20 mA
6
7
8
l
W-
l
H+
1) Jumper between 5 and 7 only for three-wire system
2
3
4
5
+
–
J
6
7
8
9
10
4 ... 20 mA
0/4 ... 20 mA
2
3
4
5
+
–
6
7
8
9
10
18 ... 30 V
J
+
–
BE1 = Binary Input
BE1 = Binary Input
1)
Power Supply
Non-Hazardous
Hazardous area, Zone 1
5. Profibus DA/DP, Foundation Fieldbus
4 ... 20 mA
BE1 = Binary Input
7
8
9
10
+
–
J
6
Input for safety shutdown (activated using coding jumper)
1)
≤ 30 V
≤ 24 V
+
–
BE1 = Binary Input
7
9
10
+
–
6
1)
81
82
Input for safety shutdown (activated using coding jumper)
1)
≤ 24 V
–
BE1 = Binary Input
7
9
10
+
–
6
81
82
HART
modem
PC/Laptop
R 250 W if req.
1)
3
Only required with current sources not conforming to HART
1)
2
3
4
5
+
–
I
l
y
= 4 ... 20 mA
6
7
8
l
W-
l
H+
1) Jumper between 5 and 7 only for three-wire system
2
3
4
5
+
–
J
6
7
8
9
10
4 ... 20 mA
0/4 ... 20 mA
2
3
4
5
+
–
6
7
8
9
10
18 ... 30 V
J
+
–
BE1 = Binary Input
BE1 = Binary Input
1)
Power Supply
Non-Hazardous
Hazardous area, Zone 1