Bray 7000_8000 Series User Manual
Bray Equipment
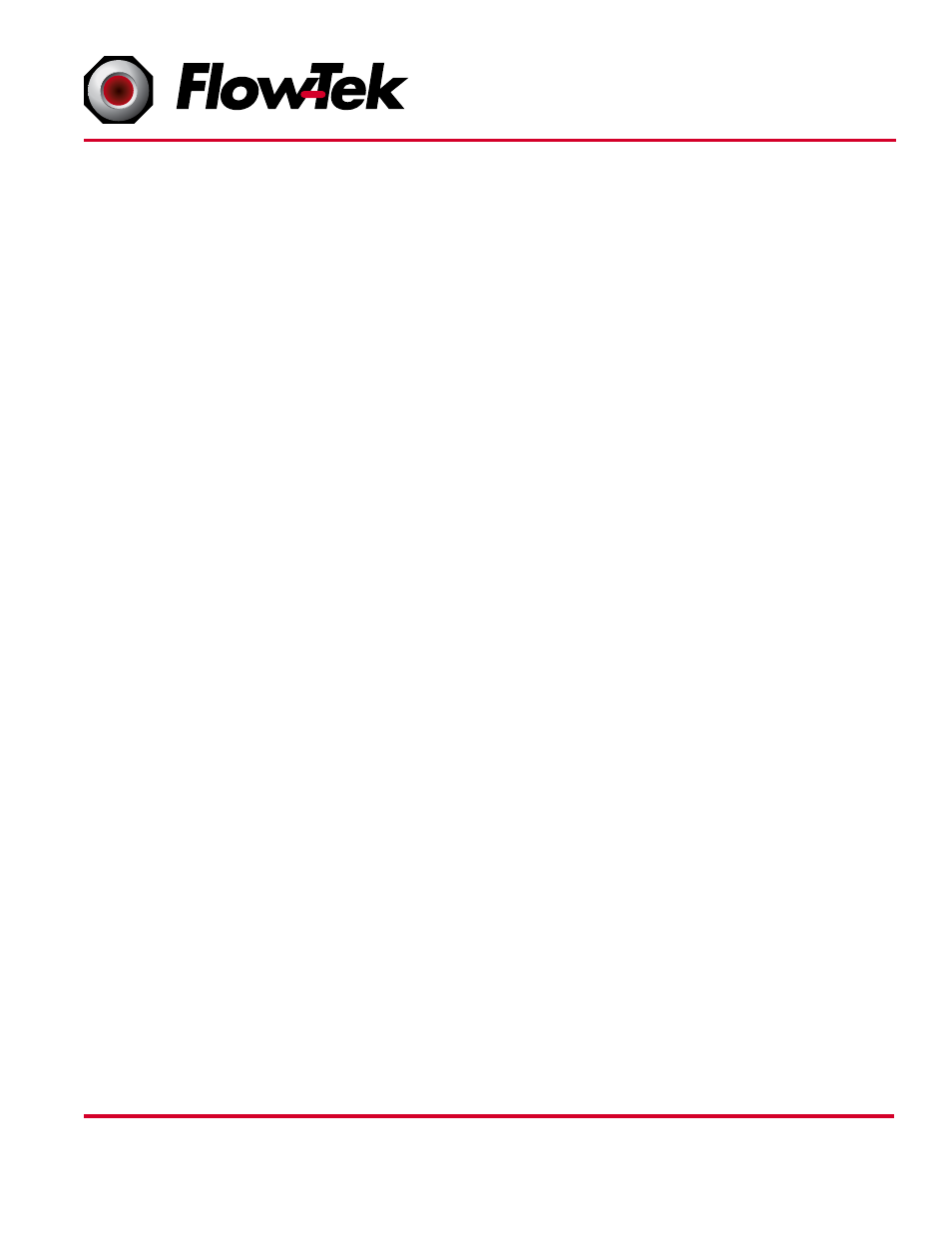
Installation and Maintenance Manual
Series 7000 and 8000 Ball Valves
Date: August 2011 / Page 1 of 9
®
A Subsidiary of BRAY INTERNATIONAL, Inc.
FLOW-TEK,
Inc.
Tel:
832.912.2300
© 2011 Flow-Tek, Inc.
8323 N. Eldridge Pkwy #100
Fax: 832.912.2301
Houston,
Texas
77041
www.flow-tek.com
7000/8000 SERIES BALL VALVES
INSTALLATION - MAINTENANCE MANUAL
USE:
The design features of this valve include three piece
construction and a “free floating” ball allowing ease
of maintenance without special tools. The ball is not
fixed, but is free to move with the line pressure. As a
result of this feature, these valves are capable of tight
shut-off with flow in either direction regardless of the
position of the valve in the line.
The downstream seat, opposite the pressurized side of
a closed valve, must carry the load exerted by the line
pressure on the ball, while the upstream seat is subject
to little load or wear. For this reason, it is sometimes
possible to increase useful seat life by turning the valve
end-for-end in the pipeline.
1. USE:
The valve should be maintained as part of a preventative
maintenance program and in accordance with
Flow-Tek’s recommended pressure, temperature and
corrosion limits to ensure a long service life. During
shipment, storage, and in operation, the valve should
be fully open or fully closed (“open” is preferred for
shipping and storage). Do not use in throttling service
without investigating flow and pressure conditions.
WARNING: Before installing this equipment, confirm
that it is suitable for the intended service.
The identifications tags describe the maximum allowable
service conditions for this product.
Be sure that the installation is protected by appropriate
pressure control and safety devices to ensure that
acceptable limits are not exceeded.
2. OPERATION:
Operation of the valve is done by turning the handle a
1/4 turn (90 degree turn). CW to close, CCW to open.
A. VALVE OPEN POSITlON
The handle is parallel with the pipeline.
B. VALVE IN CLOSED POSITION
The handle is perpendicular to the pipeline.
Valves with actuators should be checked for actuator
-valve alignment. Misalignment will result in high
operational torque and damage to valve stem and seals.
STEM SEAL ADJUSTMENT:
Stem seal leakage may be corrected without disassembly
by tightening the packing gland nut until such leakage
stops. If the leakage continues or valve operating torque
becomes excessive, the seals are worn and replacement
will be necessary.
1. For 1/2”- 2”, if slight leakage is noted at stem,
straighten lock washer tab, tighten stem nut to
flatten Bellville Washers, back stem nut off 1/4
turn, secure lock washer tab.
2. For sizes larger than 2”, simply tighten the gland
bolts evenly until leak stops. Do not over tighten.
3. GENERAL INFORMATION FOR ON-SITE
INSTALLATION:
Before installing the valves, the pipes must be flushed
clean of dirt, burrs, and welding residues, or the seats
and ball surface will be damaged.
The valve may be installed in any position on the
pipeline.
The pipe must be correctly aligned and spaced as to
not induce stresses in the valve.
As shipped from the factory, Valves may contain
silicone based lubricant. This is for break-in and may
be removed by disassembly and solvent washing, if it
is objectionable for a particular application.
INSTALLATION OF THREADED END VALVES:
1. The use of a thread sealant is recommended; Use
conventional sealant, such as hemp core, Teflon, etc;
2. Apply wrench only on the hex/octagon nearest