Bray MPF150_130_230_240 Series User Manual
Bray Equipment
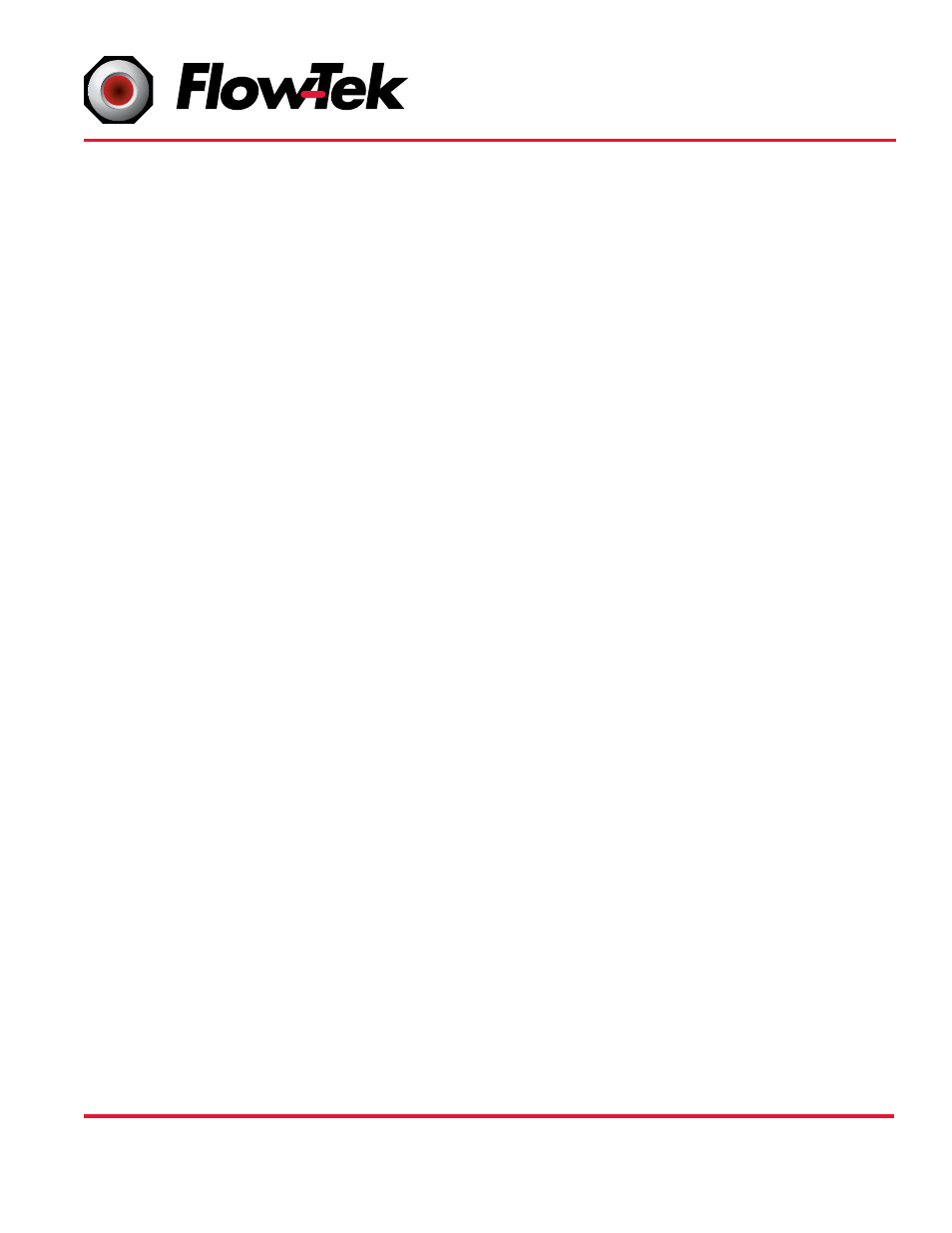
Installation and Maintenance Manual
MPF150/300, MPT230/240 Ball Valves
Date: April 2012 / Page 1 of 8
®
A Subsidiary of BRAY INTERNATIONAL, Inc.
FLOW-TEK, Inc.
Tel: 832.912.2300
© 2011 Flow-Tek, Inc.
8323 N. Eldridge Pkwy #100
Fax: 832.912.2301
Houston, Texas 77041
www.flow-tek.com
INSTALLATION – MAINTENANCE MANUAL
SERIES MPF150, MPF300, MPT230, MPT240
Valve Installation
1. Handling
To ensure safety, user must handle the valve with
both hands so that the weight of the valve is equally
distributed at both ends. If a hoist is used to lift a large
valve, the user must make sure the hoist is strong
enough to support the weight of the valve.
2. Cleaning
To prevent damage to the seats and ball surface, the
user must inspect the valve for dirt, burrs and welding
residues prior to installation. Although all valves were
cleaned and bagged prior to delivery, if for some
unforeseen circumstances that the valves were soiled
during transportation, the user must clean the valve
prior to installation. The user may clean the valve by
water, steam or pressurized air.
3. Flow Direction
Our valves are bi-directional, meaning upstream or
downstream could be at either end of the valve.
4. Position and Weight Support
The weight of the valve must be properly supported by
means other than the connected pipelines. The valve
end connection and the pipeline forms an integral
sealing zone. If the weight of the valve is entirely
distributed to the joint area, the valve will defonn and
cause leakage.
5. Installation of Threaded End Valve(MPT230)
a. Use conventional sealant, such as hemp core,
Teflon, etc.
b. Use wrench and apply force on the hexagon
end of the valve only. Apply force to other area
of valve may seriously damage the valve.
c. For applications where threaded end valves
are back-welded on site, the valves must be
dismantled according to instructions for weld
end valves.
6. Systems Hydrostatic Test
Before delivery, our valves are tested to 1.5 times
the allowable pressure at ambient temperature in the
partial open position. After installation, the pipeline
may be subjected to system test pressure of no more
than 1.5 times the rated pressure.
Valve Operation
1. Ball Valve Flow Diagram
Our multiport ball valve may be configured into many
different options depending on customer’s application.
Refer to the last page of this IOM Manual for all the
possible flow patterns.
2. Manual Operation
a. Valve Flow Path is indicated by markings on
the top of ball valve stem.
b. The illustration on the last page shows standard
valve position at the time of shipment.
3. Automatic Operation
a. Prior to actuator installation, please check the
flow path of the valve as indicated by marking
on the top of ball valve stem as shown in the
illustrations on the last page.
b. After Actuator installation, valve should
be check for valve stem alignment. Axial
misalignment will result in high operational
torque and unnecessary wear on the stem seal.
Maintenance
1. Maintenance Frequency
User should determine the maintenance frequency
depending on specific application. If there is sign
of leakage from the stem, it is time to replace the
stem sealing components. If there is sign of internal
leakage, it is time to replace the seats and gasket
components. Life of the valve can be maximized if the
valve is used within the rated range, in accordance
with pressure, temperature, and corrosion data.