Emerson Process Management ControlWave EFM 3808 User Manual
Page 101
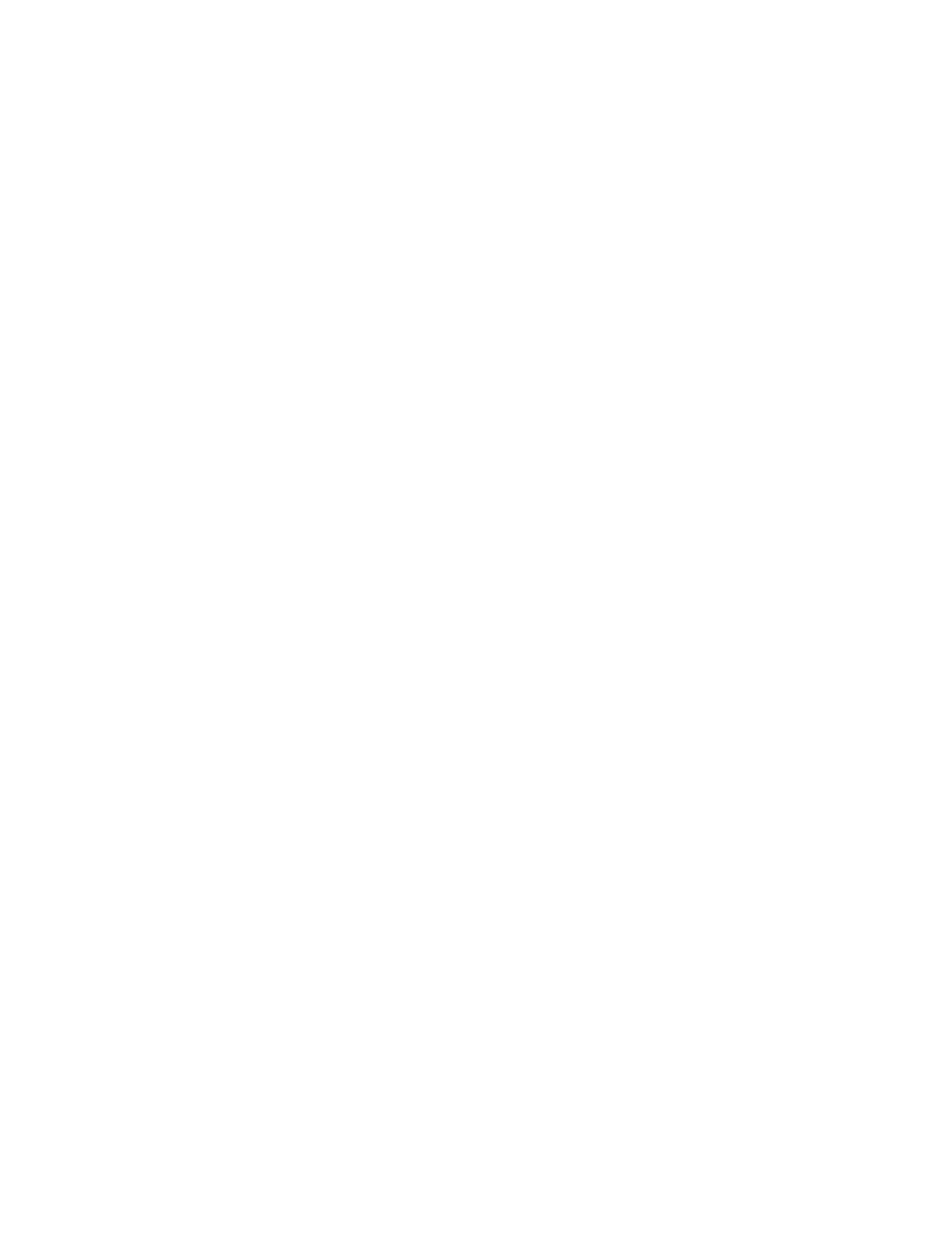
CI-ControlWave EFM
Installation & Operation / 2-49
1. Remove connector TB1 from the System Control Module (SCM) and remove the
Battery/Power Harness from the Battery Charger/Power Manager Board.
2. Remove the Lead-acid Battery from its shipping carton.
3. Install the Lead-acid Battery (on end) as illustrated in Figure 2-36. Note: Make sure
the Lead-acid Battery is fully charged before installing it.
4. Route Solar Panel Power Wiring Harness into the enclosure through the Solar Power
Conduit Fitting (see Item 5 of Figure 2-3).
5. Connect the Solar Panel Harness to the internal Battery (Red = Pos. & Black = Neg.).
6. Secure the Battery via the Battery Clamp.
7. When you are ready to apply power, connect the Battery Power Harness to either the
Power Distribution Board (if present) or to TB1 on the SCM.
2.3.9.5 ControlWave EFM System Grounding
ControlWave EFM Enclosures are provided with a Ground Lug that accommodates up to a
#4 AWG wire size. A ground wire must be run between the Enclosure’s Ground Lug (see
Figure 2-3) and a known good Earth Ground. As an extra added precaution, it is
recommended that a #14 AWG wire be run from SCM Power Connector TB1-3 (Chassis
Ground) to the same known good Earth Ground. The following considerations are provided
for the installation of ControlWave EFM system grounds (see S1400CW):
• Chassis Ground Lug to Earth Ground wire size should be #4 AWG. It is recommended
that stranded copper wire is used and that the length should be as short as possible.
• This ground wire should be clamped or brazed to the Ground Bed Conductor (that is
typically a stranded copper AWG 0000 cable installed vertically or horizontally).
• The wire ends should be tinned with solder prior to insertion into the Chassis Ground
Lug. Note: Use a high wattage Soldering Iron.
• The ground wire should be run such that any routing bend in the cable has a minimum
radius of 12-inches below ground and 8-inches above ground.
2.3.10 Operation of the Lithium Backup Coin-cell Battery
CPU Modules have a Coin-cell Socket (S1) that accommodates a 3.0V, 300 mA-hr lithium
coin cell. A supervisory circuit on the CPU is used to switch to battery power when the
regulated 3.3Vdc VCC falls out of specification. The CPU switches the battery voltage to the
VBAT3.3 hardware signal, which provides backup power for the real-time clock (RTC) and
the system SRAM on the CPU Module.
The system SRAM has a standby current draw of 20uA maximum for each part. For a unit
containing 2MB of SRAM, a worst-case current draw of 42uA allows a battery life of
approximately 7142 hours.
Jumper JP1 on the Battery Backup Board must be installed to enable the battery. For
maximum shelf life, the battery may be isolated from the circuit by removing Jumper JP1.
JP1’s suitcase jumper can be stored on either of its pins.
CPU Modules are shipped with the Lithium backup battery installed. To remove the
backup battery, pry up the Battery Securing Tab on the Coin-cell Battery Socket and then
remove the battery using a pair of tweezers or needle-nose pliers. Install the replacement
battery. Note: This step will not be required until units have been in operation for an ex-
tended period of time (normally many years) as the battery life is approximately 7142 hours
of backup service. (Power is drawn from the battery when the unit looses power).