Mode commands – HEIDENHAIN PWM 20 User Manual
Page 228
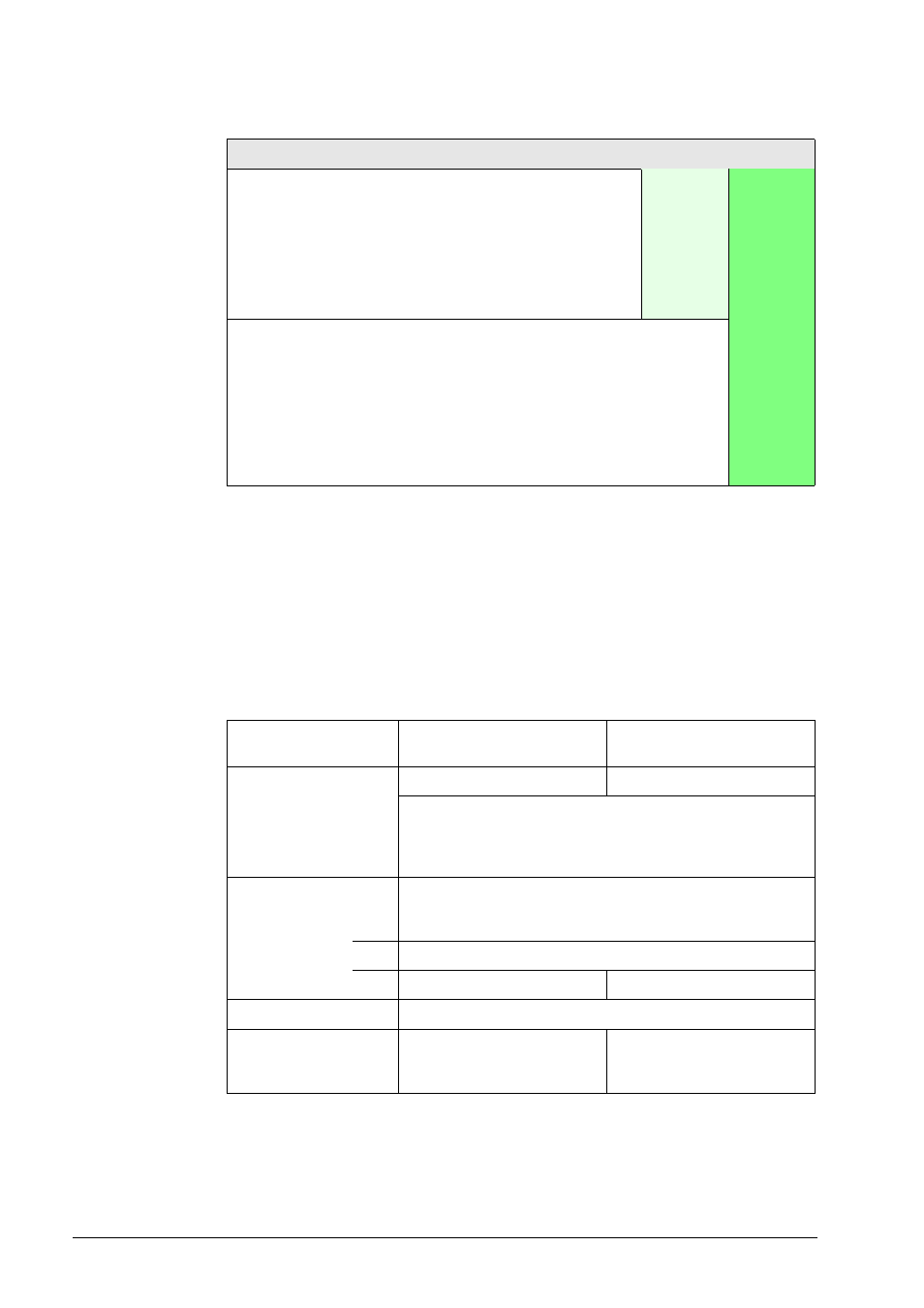
November 2014
Interface description
229
MODE commands
1)
Same reaction as from switching the power supply off and on
2)
Selected additional information is also transmitted
3)
Reserved for encoders that do not support the safety system
The time absolute linear encoders need for calculating the position values tcal differs depending
on whether EnDat-2.1 or EnDat-2.2 MODE commands are transmitted (see catalog: Linear
Encoders for Numerically Controlled Machine Tools – Specifications). If the incremental signals
are evaluated for axis control, then the EnDat 2.1 MODE commands should be used. Only in this
manner can an active error message be transmitted synchronously with the currently requested
position value. EnDat 2.1 MODE commands should not be used for pure serial position-value
transfer for axis control.
MODE commands
Encoder send position value
Selection of memory area
Encoder receive parameters
Encoder send parameters
Encoder receive reset
1)
Encoder send test values
Encoder receive test command
EnDat 2.1
EnDat 2.2
Encoder send position value with additional data
Encoder transmit position value and receive selection of
memory area
2)
Encoder send position value and receive parameter
2)
Encoder send position value and send parameter
2)
Encoder send position value and receive error reset
2)
Encoder send position value and receive test command
2)
Encoder receive communication command
3)
Without delay
compensation
With delay compensation
Clock frequency
f
C
100 kHz ... 2 MHz
100 kHz ... 16 MHz
Calculation
time for
Position value
Parameter
t
cal
t
ac
See Specifications
Max. 12 ms
Recovery time
t
m
EnDat 2.1: 10 to 30 µs
EnDat 2.2: 10 to 30 µs or 1.25 bis 3.75 µs (fc
1 MHz)
(parameterizable)
t
R
Max. 500 ns
t
ST
-
2 µs to 10 µs
Data delay time
t
D
(0.2 + 0.01 x cable length in m) µs
Pulse width
t
HI
t
LO
0.2 to 10 µs
0.2 to 50 ms/30 µs (with LC)
Pulse width fluctuation
HIGH to LOW max. 10 %