Feed table, Roller pressure adjustment knobs – Drylam PRO-LAM PL1200-HP User Manual
Page 36
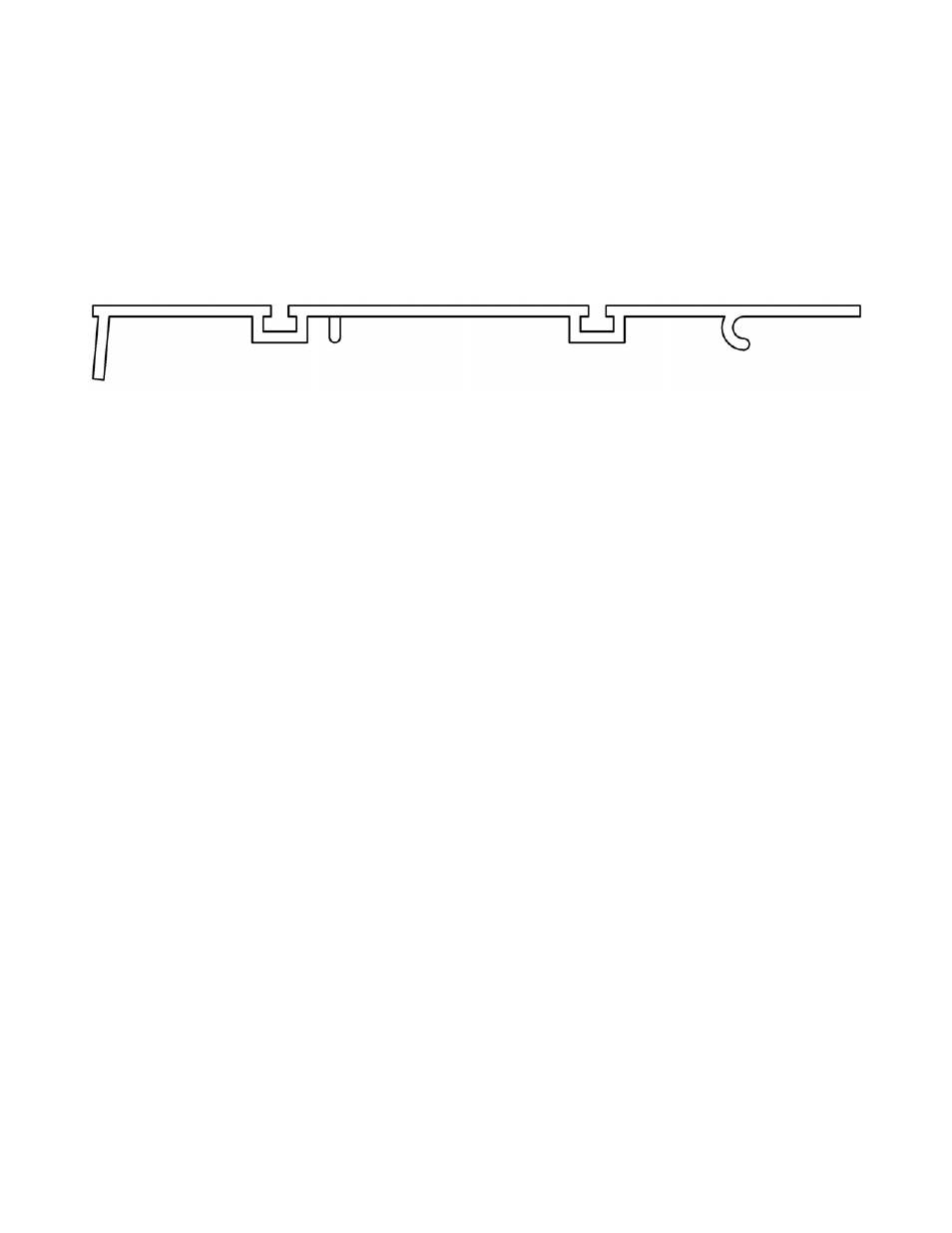
36
Feed Table
The feed table is used to correctly position the material in relation to the rollers. Located on the surface of
the Feed Table are two (or more by option) feed guides. These guides help keep the material being
laminated square and aligned with the film edge and, in effect, correctly locate it for slitter operation.
These feed guides are adjustable for both angle and position. To adjust the feed guides simply loosen the
two knurled knobs located on the top of the guides and slide the feed guide to the desired location.
Adjustment
For a preliminary adjustment to align the feed guides to the slitters locate the feed guide in the
approximate desired location. Using a piece of paper align it along the front of the feed table even with the
edge. While holding the paper in position, align the feed guide with the edge of the paper. Tighten knurled
knobs. This preliminary adjustment should bring the feed guides parallel to the film path and only require
very small adjustments. Run a piece of paper through while using the slitters. Take note of the difference
in the alignment of the paper from end to end and divide the difference in half. This should be the amount
that the feed guide should be adjusted. If the front side of the paper is too far to the right move the
backside of the feed guide to the right and vice versa.
Roller Pressure Adjustment Knobs
These adjustment knobs are located in each corner on the top of the side frames, two for the rear and two
for the front. They control the amount of pressure that is put on the rollers and the laminate. Typical
adjustment is about 1-2 full turns on the front and 0-1 turns on the rear. When running materials thicker
than 1/8” always loosen the front adjustment to one turn or less and the rear to one turn or less. To obtain a
closer edge seal on thicker papers such as 8 or 12-point cover or card stock it may be necessary to increase
the pressure on the front rollers from the factory settings.
Too little pressure on the front rollers will result in poor edge seal and in severe cases a poor surface bond.
Excessive pressure on the front or rear rollers may result in accelerated roller wear, or curled laminate
from front to back or corner to corner.
Roller pressure may affect film curl as the film exits the laminator. The laminate should be checked for
curl after a roller pressure adjustment.