2 connections at the encapsulator b-395 pro, Connections at the encapsulator b-395 pro – BUCHI Encapsulator B-395 Pro User Manual
Page 18
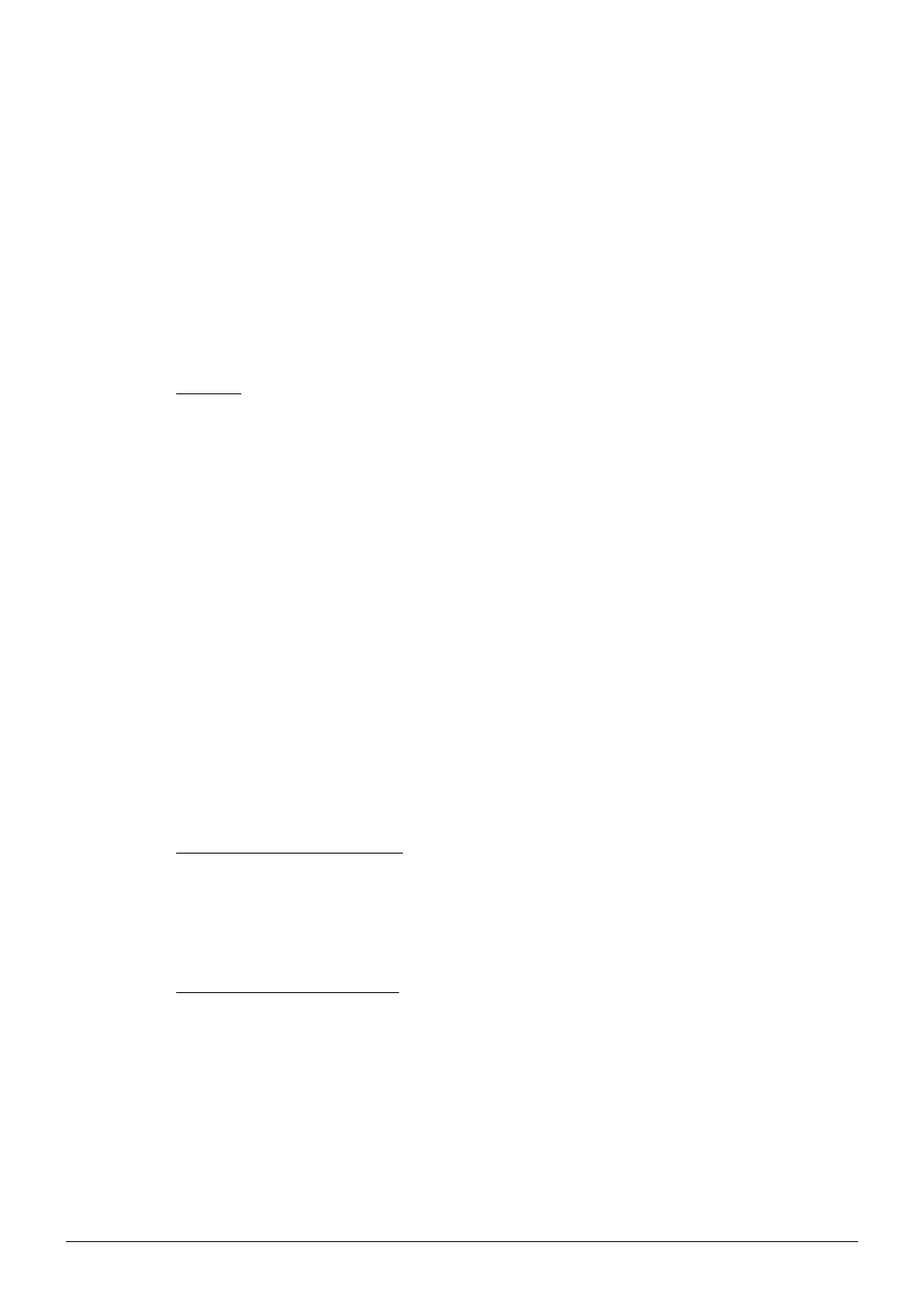
4 Description of function
18
B-395 Pro
Operation Manual, Version C
The main parts of the Encapsulator B-395 Pro are the control unit, with the syringe pump, the elec-
trical and pneumatic systems, and the reaction vessel. All parts of the instrument which are in direct
contact with the beads can be sterilized by autoclaving.
The product to be encapsulated (cells, microorganisms, or other biologicals and chemicals) is mixed
with an encapsulating polymer (typically alginate) and the mixture put into a syringe or a pres-
sure bottle , see figure 4-1. The polymer-product mixture is forced into the pulsation chamber
by either a syringe pump a or by air pressure . The liquid then passes through a precisely drilled
nozzle and separates into equal size droplets on exiting the nozzle. These droplets pass through an
electrical field between the nozzle and the electrode resulting in a surface charge. Electrostatic
repulsion forces disperse the beads as they drop to the hardening solution.
Bead size
The bead size is controlled by several parameters including the vibration frequency, amplitude, nozzle
size, flow rate, and physical properties of the polymer-product mixture. In general, the bead diameter
of Ca-alginate beads is twice the nozzle diameter. But, by varying the jet velocity and the vibration
frequency, the range can be adjusted by about ±15 %.
Optimal parameters for bead formation are indicated by visualization of real-time bead formation in the
light of a stroboscope lamp . When optimal parameters are reached, a standing chain of droplets is
clearly visible. Once established, the optimal parameters can be preset for subsequent bead produc-
tion runs with the same encapsulating polymer-product mixture. Poorly formed beads, which occur at
the beginning and end of production runs, are intercepted by the bypass cup .
Depending on several variables, 50 to 5000 beads are generated per second and collected in a
hardening solution within the reaction vessel . Solutions in the reaction vessel are continuously
mixed by a magnetic stir bar to prevent bead clumping. In addition, the reaction vessel and/or
solution must be electrically grounded. At the conclusion of the production run, the hardening solution
is drained off (waste port ), while the beads are retained by a filtration grid . Washing solutions,
or other reaction solutions, are added aseptically through a sterile filter . The beads can be further
processed into microcapsules, or transferred to the bead collecting flask .
4 .2
Connections at the Encapsulator B-395 Pro
Front connections (See figure 5-2)
• Main switch
• Air out
• Voltage
• Ground
Rear connections (See figure 5-1)
• Electric supply
• Air inlet
• Magnetic stirrer
• Vibration
• Optional plug