Feedback tab – Rockwell Automation 1756-HYD02 ControlLogix Hydraulic Servo Module User Manual
Page 58
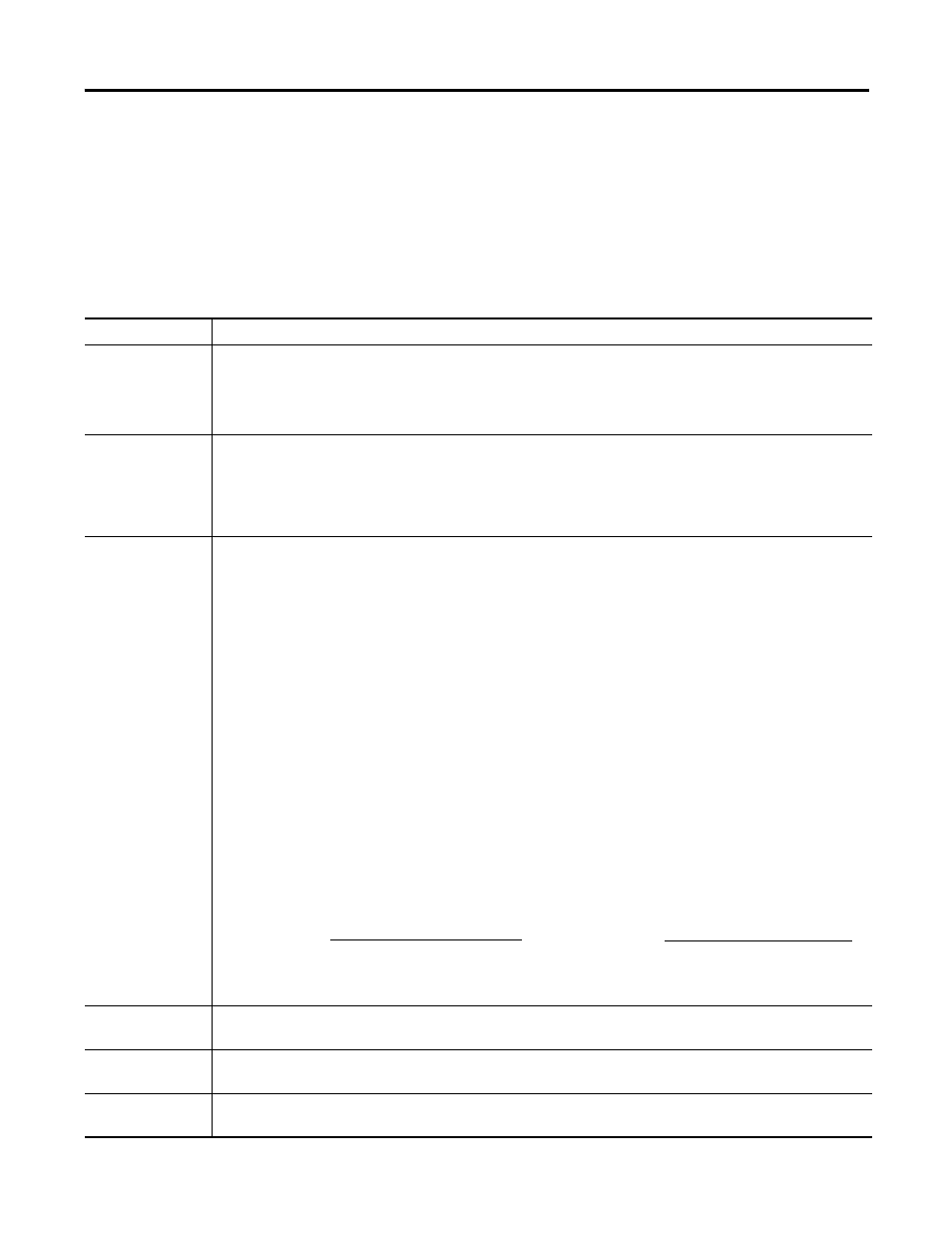
58
Publication 1756-UM525A-EN-P - June 2003
Chapter 4 Using the 1756-HYD02 Module Features
Feedback Tab
Use the Feedback tab to select a feedback type. RSLogix 5000 displays multiple
feedback types for the 1756-HYD02 module. At this release of the
1756-HYD02 module, only the LDT type is available. The table below lists the
configurable features available on the LDT feedback option.
Feature:
Definition:
LDT Type
Selection determines what type of LDT provides feedback to the 1756-HYD02 module.
• PWM - also called Gated or DPM
• Start/Stop Rising Edge
• Start/Stop Falling Edge
Recirculations
Recirculations is the process of acquiring a measurement from an LDT. You can repeat the measurement process
several times for each interrogation. The repetition of the measurement process is done automatically inside LDTs
with PWM type output. When configuring the LDT, you can select the number of times the process is repeated; that
number is used in this field.
Note that this field is enabled only if you have chosen PWM for LDT Type.
Calibration
Constant
The calibration constant (also called Gradient on some LDTs) is a number that is engraved on each LDT by the
manufacturer. It specifies the characteristics of that individual transducer. Because each transducer has its own
calibration constant, this number is used to calculate the conversion constant for the axis; the conversion constant
changes when an LDT is changed on an axis.
To calculate the Minimum Servo Update Period, use one of the following formulas:
For
μ
s/in: For
m/s:
These formulas do not assume a pre-existing calibration constant or conversion constant. Also, for an LDT with SSI
interface the formulas above apply. However, the specifications for LDTs with SSI interface vary in nature; we
recommend that you apply the manufacturers update period recommendations rather than have RSLogix 5000
compute a minimum servo update period. If it is a rotary (non-LDT) transducer with SSI interface then the Servo
Update Period can be simply defaulted to 250
μ
s.
Since both axes of the module must be updated at the module's configured servo update rate, make sure the
selected Servo Update Period on the Associated Axes tab is greater than the largest computed limit value above for
the two axes associated with the module.
To calculate the new conversion constant when an LDT is changed, use one of the following formulas:
If the calibration constant is in
μ
s/in:
If the calibration constant is in m/s:
You must type the new conversion constant in the Conversion Constant field on the Conversion tab. RSLogix 5000
does not automatically update the field after you use the Calculate button on this tab.
Length
LDT length defines the stroke of travel of the hydraulic cylinder. LDT length is used with the number of recirculations
to calculate the minimum servo update period.
Scaling
Scaling defines the relationship between the transducer unit of measure, as defined in the transducer length field,
and the user’s unit of measure (e.g. 39.37 inches/meter) defined on the Units tab.
Enable Absolute
Feedback
Absolute Feedback is always enabled for LDT.
Minimum Servo
Update Period =
[Length (in) X Calibration Constant (
μ
s/in) + Recirculation
delay (approximately 25
μ
s)] X Recirculations
Minimum Servo
Update Period =
[Length (m) X Calibration Constant (m/s) + Recirculation
delay (approximately 0.000025s)] X Recirculations
New conversion constant =
Old conversion constant X New calibration constant
Old calibration constant
New conversion constant =
Old conversion constant X Old calibration constant
New calibration constant