6 engine implement pump, 1 pump description, 2 pump failure analysis – JLG 534D-10 User Manual
Page 137: 3 pump replacement, Control valves, Engine implement pump, Pump description, Pump failure analysis, Pump replacement
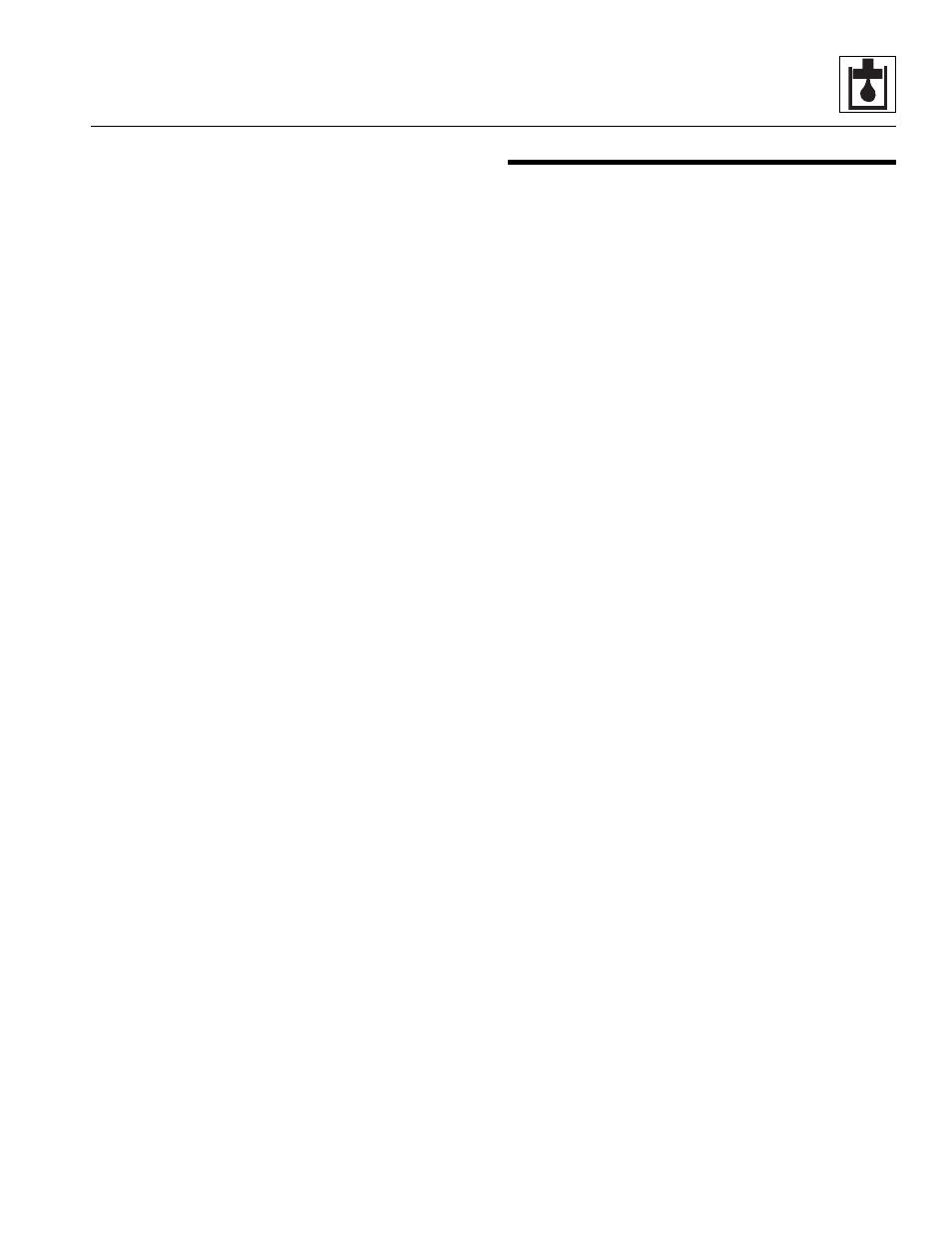
8.13
534D-9, 534D-10 & 544D
Hydraulic System
c. Cleaning and Drying
If contaminated hydraulic oil or foreign material is in the
tank, the tank can usually be cleaned.
Note: If a leak is suspected in the hydraulic oil reservoir,
contact JLG Service Department.
1. Have a dry chemical (Class B) fire extinguisher near
the work area.
2. Remove the hydraulic oil reservoir drain plug, and
safely drain any hydraulic oil into a suitable
container. Dispose of hydraulic oil properly.
3. Clean the hydraulic oil reservoir with a high-pressure
washer, or flush the tank with hot water for five
minutes and drain the water. Dispose of
contaminated water properly.
d. Inspection
Note: If a leak is suspected in the fuel or hydraulic oil tank,
contact JLG Service Department.
1. Inspect the hydraulic oil reservoir thoroughly for any
cracks, slices, leaks or other damage.
2. With the hydraulic oil reservoir removed from the
machine, plug all openings except one elbow fitting.
Install the elbow fitting, and apply approximately
1-1.5 psi (7-10 kPa) of air pressure through the
elbow. Check the reservoir for leaks by applying a
soap solution to the exterior and look for bubbles to
appear at the cracked or damaged area.
e. Reservoir Installation
1. Place the hydraulic oil reservoir into its original
orientation.
2. Secure the hydraulic oil reservoir to the frame with
the previous mounting hardware.
3. Uncap and connect the previously labeled hydraulic
hoses to their appropriate locations.
4. Install the hydraulic fluid level sight-glass using
special designed and drilled capscrews and gaskets.
5. Install hydraulic filter bracket and hydraulic filters.
6. Fill the hydraulic oil reservoir according to
specifications. Refer to Section 2.4, “Fluid and
Lubricant Capacities.”
7. Check the hydraulic oil reservoir for leaks.
8. Connect the battery negative (-) cable to the battery
negative (-) terminal.
9. Install the hydraulic oil reservoir/fuel tank cover.
10. Close and secure the engine cover.
8.6
ENGINE IMPLEMENT PUMP
8.6.1
Pump Description
For internal service instructions contact your local JLG
distributor.
8.6.2
Pump Failure Analysis
The pump is the “heart” of the hydraulic system, and
whenever there is a problem in the system, the pump
often is blamed. However, pump failure is seldom due to
failure of pump components. Pump failure usually
indicates another problem in the hydraulic system.
According to pump manufacturer statistics, 90-95 percent
of pump failures are due to one or more of the following
causes:
• Aeration
• Cavitation
• Contamination
• Excessive Heat
• Over-Pressurization
• Improper Fluid
In the event of pump failure, investigate further to
determine the cause of the problem.
8.6.3
Pump Replacement
a. Pump Removal
1. Park the machine on a firm, level surface, level the
machine, fully retract the boom, lower the boom,
place the transmission control lever in (N) NEUTRAL,
engage the park brake and shut the engine OFF.
2. Place a Do Not Operate Tag on both the ignition key
switch and the steering wheel, stating that the
machine should not be operated.
3. Open the engine cover and the hydraulic oil
reservoir/fuel tank cover. Allow the system fluids to
cool.
4. Disconnect the battery negative (-) cable from the
battery negative (-) terminal.
5. Drain the hydraulic reservoir. Refer to Section 8.5.1,
“Hydraulic Oil Reservoir Draining.”
6. Relieve any trapped pressure in the hydraulic
system.
7. Thoroughly clean the pump and surrounding area,
including all hoses and fittings before proceeding.
Note: Cap all hoses as you remove them to prevent
unnecessary fluid spillage.