2 engine disassembly, inspection and service, 3 engine installation, Engine disassembly, inspection and service – JLG 534D-10 User Manual
Page 121: Engine installation
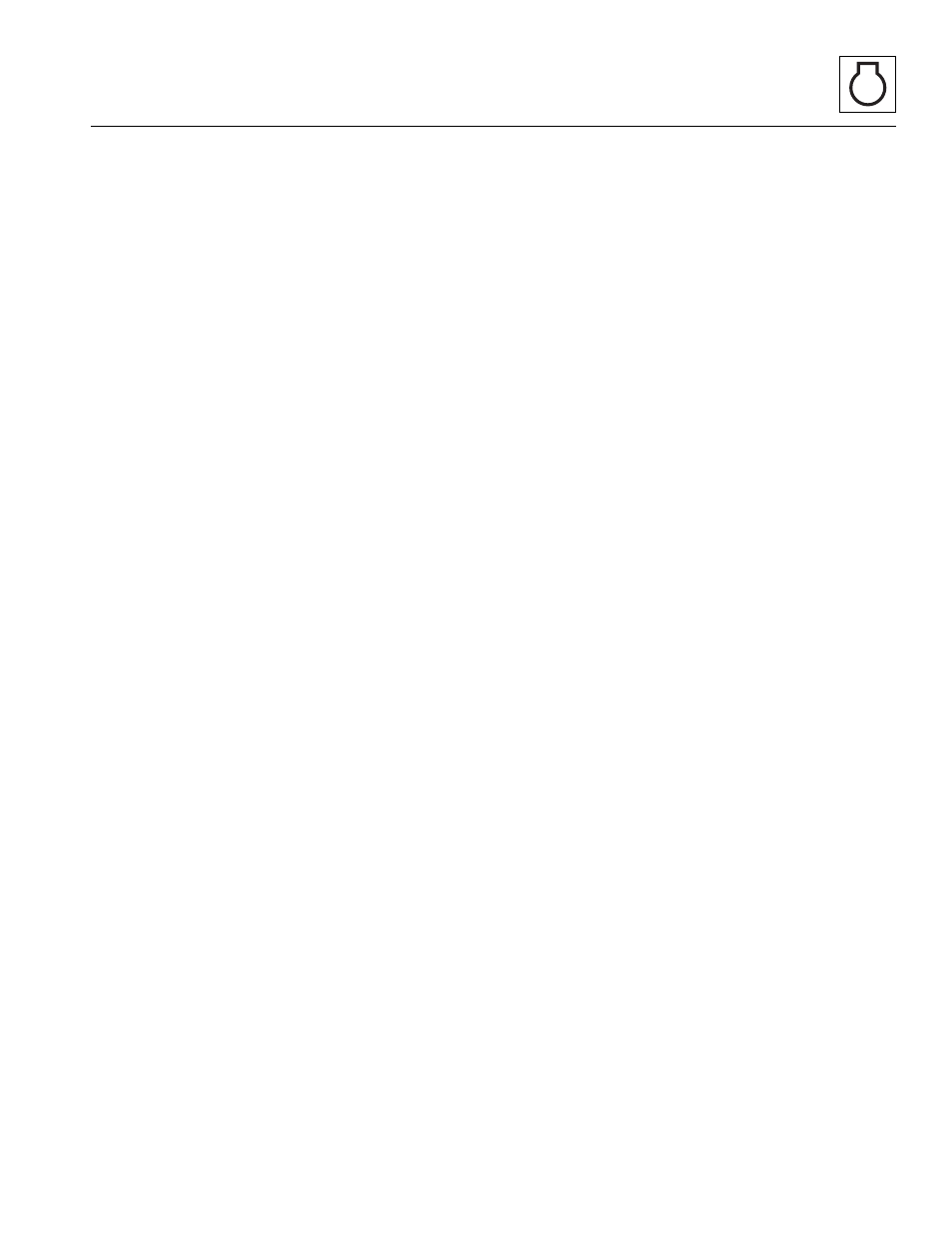
7.13
534D-9, 534D-10 & 544D
Engine
18. Remove the exhaust flex pipe from the exhaust pipe.
Remove the exhaust pipe from the exhaust manifold.
19. Loosen the clamps on the air intake at the engine
and on the 90° elbow.
20. Remove the air intake elbow, tube and 90° elbow.
Cover the end of the air intake tube still attached to
the side of the cab.
Note: Disregard the following directions in step 23, 24
and 25 if pump is being left on machine and continue to
step 26.
21. Label, disconnect and cap all hydraulic hoses and
tubes attached to the traction lock valve. Cap all
fittings and openings to prevent dirt and debris from
entering the hydraulic system.
22. Remove tubes and traction lock valve.
23. Loosen and remove both hydrostatic drive pump
mounting bolts. Pull pump back until clear of engine.
24. Loosen and remove the three engine mount bolts
and washers.
25. Secure the engine with a lifting strap or chain from
the appropriate lifting points. Use a suitable hoist or
overhead crane. Have an assistant ensure that the
engine clears all frame components during removal.
26. Place engine on a flat, level surface.
7.12.2
Engine Disassembly, Inspection and
Service
Engine disassembly, internal inspection, service, repair
and assembly procedures are covered in the appropriate
service manual. Contact the local power unit parts
distributor for further information.
Note: If the engine is being replaced, there may be external
components that will be required to be transferred from the
original engine to the replacement engine depending upon
who you purchase the new engine from and the
configuration of your replacement engine. Refer to the
appropriate user manual for detailed procedures that cover
the transfer of original engine components to the
replacement engine.
7.12.3
Engine Installation
1. Secure the engine with a lifting strap or chain from
the appropriate lifting points. Use a suitable hoist or
overhead crane.
2. Inspect the engine mounting bracket isolators.
Replace isolator if cracked or worn.
3. Lift the engine and slowly push and lower into the
engine bay. Have an assistant ensure that the
engine clears all frame, hose and harness
components during engine installation.
4. Align the motor mount holes and install the bolts.
Tighten the motor mount bolts.
5. Push the hydrostatic drive pump splined shaft into
the coupler. Install and tighten both bolts.
6. Torque the hydrostatic pump bolts to 240 lb-ft
(325 Nm), +25/-0 lb-ft (+34/-0 Nm).
7. Connect the fuel inlet and return lines to the engine.
Note: The engine harness is routed and attached at
various places on the engine using hold-down clamps
and plastic wire ties. Before installing engine and with
the help of an observer, ensure that engine clears the
harness during installation.
8. Connect all the labeled wire harness connections on
the engine and hydrostatic drive pump.
9. Install brackets and the traction lock valve.
10. Uncap and reconnect the previously labeled tubes
and hoses to the appropriate locations on the drive
pump and traction lock valve.
11. Install both heater hoses to the engine and tighten
clamps.
12. Install the complete radiator/cooler assembly and
tighten the mounting bolts
13. Install the hose clamps on the radiator hoses and
work onto the engine. Tighten the clamps.
14. Connect the drive pump inlet and outlet hoses on the
oil cooler.
15. Install the charge air tubes to the charge air cooler
(544D w/ John Deere engine and all Cummins
engines).
16. Install the exhaust pipe to the exhaust manifold.
Install the v-band clamp holding the exhaust pipe to
the exhaust manifold.
17. Install the flex pipe and tighten the clamps on the
exhaust pipe.
18. Install the engine cover, rear cover and dust shield.
19. Connect the battery negative (-) cable to the battery
negative (-) terminal.
20. Open the radiator cap and fill the radiator completely
with a 50/50 mixture of ethylene glycol and water.
Replace and tighten the radiator cap. Add coolant to
the overflow bottle until the bottle is 1/4 to 1/2 full.
This overfilling will compensate for any air trapped in
the cooling system.
21. Open the hydraulic oil reservoir and fill with
Mobilfluid 424
®
Tractor Hydraulic Fluid (ISO 46).