0 description, 1 field of application, 2 method of functioning – ARI Armaturen ARI-PREMIO Plus EN User Manual
Page 5
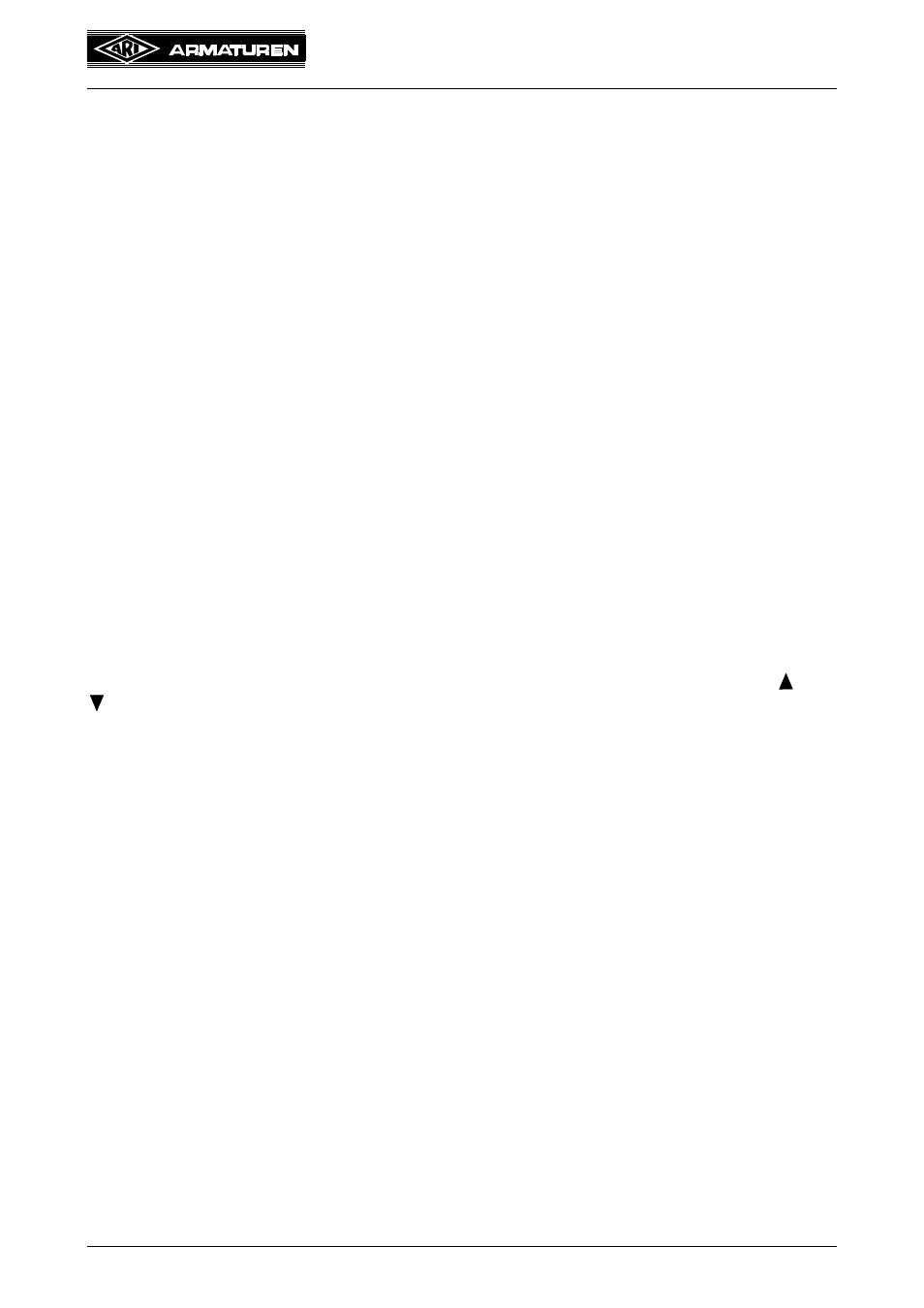
0040501004 5010
Page 5
Operating and installation instructions
Thrust actuator ARI-PREMIO-Plus
4.0 Description
4.1 Field of application
ARI-PREMIO linear thrust actuators are employed to actuate control or shut-off valves
requiring a nominal linear stroke distance.
The intelligent PREMIO-Plus thrust actuator is used whenever the actuator is controlled
with an analogue signal (0 to 10 V / 4 to 20 mA) or a 3-point signal and feedback
information about positions, operating states, faults, etc. has to be output.
If supplied with the valve, the lift of the thrust actuator will be set to the stroke distance of
the valve.
Selection of the proper actuator version in alignment with the corresponding fitting as well
as use of the thrust actuator in accordance with the specified technical data is the
responsibility of the systems engineer.
See data sheet for areas of application, application limits and potential.
Any use of the thrust actuator beyond the specified technical data or improper use of the
actuator is deemed to be not for the intended purpose.
The ambient conditions have to be conform to the actual electromagnetic compatibility
directives. Additional the compatibility to this directives has to be maintained in case of
expansion or other changing of the ambient conditions.
4.2 Method of functioning
The eight parameter switches allow the PREMIO-Plus thrust actuator to be adapted to a
variety of situations without a PC or tools. The electronics are likewise suitable for use in a
wide range of supply and signalling systems.
The motor and spindle can be moved up and down in manual mode by means of the and
switch positions.
The valve final positions and the type of control (3-point or analogue) are automatically
determined by the electronics in an initialisation run. An analogue signal must be present at
the input during the initialisation run for analogue control.
The desired position can be specified by means of the analogue control input. The input is
protected against polarity reversal. It can be configured as a current (4 to 20 mA) or voltage
(0 to 10 V) input using a switch.
Two binary control inputs are provided for the 3-point signal. These inputs are designed for
a wide operating range with voltages from 12 V AC/DC to 250 V AC/DC.
The 3-point control signal takes priority over the analogue input signal, e.g. for fail-safe or
anti-freeze protection. If a signal is present at both inputs (double control), the control mode
is interrupted.
The spindle position is determined by means of non-contacting and non-wearing reflex
sensors.
The motor output stage operates the connected AC motor by means of two triac switching
stages with a 3-point control signal. This stage is electrically isolated from the control
electronics by opto-decoupled drivers. A zero voltage switch controls the triacs in order to
restrict emissions to a minimum.
The actual position (position feedback) is output via the analogue output (optional). The
output signal is configured as a current or voltage output using the same switch as for the
analogue input signal. The output is electrically isolated.