Ransburg, Troubleshooting guide, Rma-303 indirect charge - maintenance – Ransburg RMA Indirect A11600 User Manual
Page 73
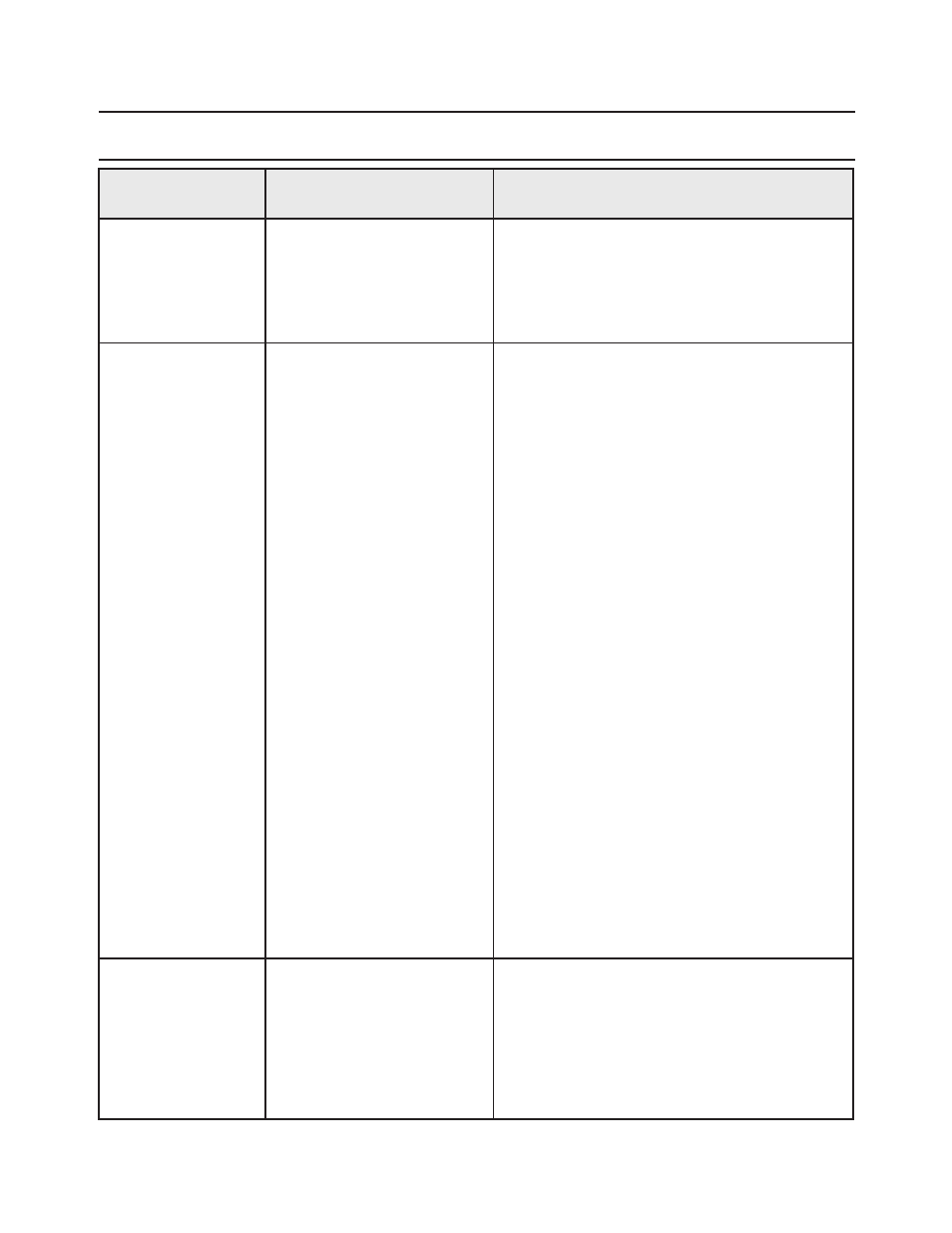
TROUBLESHOOTING GUIDE
(Continued On Next Page)
General Problem
Possible Causes
Corrective Action
Bad Spray Pattern
Low or No High
Voltage
Low Transfer
Efficiency (or
light coverage)
1. Bell cup damaged
2. Low voltage
3. Paint lodged in shaping air
ring
1. High current draw
2. MicroPak controller cas-
cade
3. Improperly mounted air
turbine
4. Faulty low voltage connec-
tions (usually indicated by
MicroPak feedback fault
light)
5. Faulty high voltage con-
nection
6. MicroPak or cascade fail-
ure
7. MicroPak settings not cor-
rect
8. Damaged high voltage
cable
9. Dielectric breakdown of
high voltage parts
10. Improper color change
(i.e., paint or solvent in
dump line)
1. Low or no high voltage
2. Poor grounding of parts
being coated
1. Replace bell cup.
2. See "Low or No High Voltage" below.
3. Disassemble and clean (see "Maintenance"
section).
1. Check resistance of electrodes.
2. Inspect low voltage at the MicroPak and the
cascade.
a. Faulty low voltage cable.
3. Verify ground connection of air turbine to
earth ground at less than 1 MΩ.
4. a. Make sure quick disconnection electrical
connection is aligned and clean.
b. Check low voltage connection at cascade.
5. Verify that high voltage cable is fully seated in
the cascade and the high voltage ring.
6. Refer to current MicroPak manual for detailed
Troubleshooting Guide.
7. Refer to current "MicroPak" manual for de-
tailed "Troubleshooting Guide."
8. Remove and inspect/measure resistance.
9. Check cascade, high voltage ring, and high
voltage cable. Replace defective parts.
10. Optimize color change.
1. Verify high voltage at electrodes. Normally,
a high voltage setting of 30-70 kV is appropri-
ate for most applications.
2. Verify that parts being coated are properly
grounded (the electrical resistance between
the part and ground must not exceed
1 megohm).
RMA-303 Indirect Charge - Maintenance
Ransburg
69
LN-9252-06.4