Maintenance schedule, Slidedriver operator maintenance schedule – Controlled Products Systems Group 222EX43 User Manual
Page 72
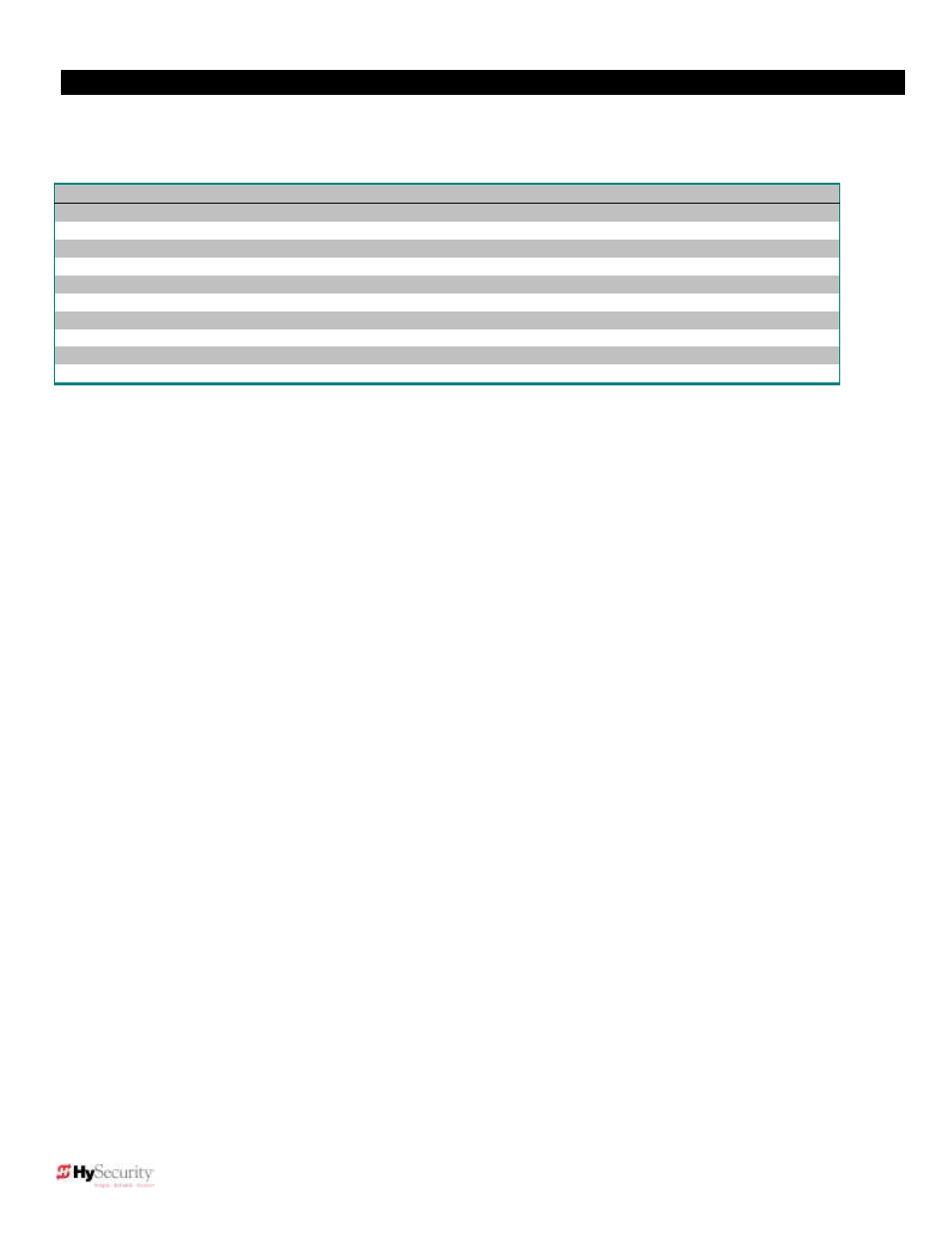
53
© 2012 Installation and Reference Manual D0119 Rev. J
Section 8
— Maintenance Schedule
SlideDriver Operator Maintenance Schedule
Name of part
What to do
Check at these recommended monthly intervals
1
3
6
12
60
Gate and hardware
Check for damage and wear
*1
X
Drive wheels
Check for tightness and wear
*2
X
Wheel clamp spring
Check for clamping tension
*3
X
Stop limit switches
Check for adjustment
*4
X
Deceleration switches
Check for adjustment
*4
X
Anchor bolts
Check for tightness
X
Fluid level
Check for loss of fluid
*5
X
Hydraulic fluid
Drain and replace fluid
X
Clock battery
Replace
*6
X
Motor Brushes (DC Only)
Replace
*7
X
Special Notes:
*1. Your gate and gate hardware will require more maintenance than your HySecurity operator. A damaged gate or worn
hardware may cause slow or erratic operation and will result in excess drive wheel wear. Lubricate gate hardware more
frequently and check for smooth operation by opening the toggle clamping mechanism and then pushing the gate
manually. One person should easily be able to push all but the largest of gates. Damaged or warped gate panels should
be straightened or replaced.
*2. Normally, drive wheel life is many years. They are designed to avoid slipping on the rail. Wheels may be greatly
shortened by any of these faults: clamping spring not adjusted correctly, operator misaligned in relation to gate panel,
badly warped gate panel, extremely stiff gate hardware, and/or loose wheel mounting bolts (tighten to 25 ft. lb).
*3. Verify that the red clamping spring is compressed tightly so that drive wheels apply a strong grip on drive rail. The red
spring should normally be compressed to 2-inches in height.
*4. The limit switch and deceleration switch rollers should ride ¼ to ½-inch below the drive rail, near the center of the
channel. Maladjustment may result in false or early tripping or no limit function at the end of travel. Verify that the limit trip
ramps are tightly bolted to the drive rail.
*5. The oil level should remain no less than one inch below the filler hole. See maintenance instructions for oil filling. Loss
of fluid is not normal and indicates a leak that must be located and repaired. Use Uniflow fluid, part MX000970, if
additional fluid is required.
*6. Replace the Smart Touch Controller battery with DL 2025 / DL 2032 or CR 2025 / CR 2032.
*7. DC Operators use DC motors with 4 carbon brushes which wear in normal operation. Worn brushes can damage the
DC motor. Under severe conditions HySecurity recommends that brushes be checked after 2 years or 250,000 cycles
and the replacement interval be adjusted as necessary.