Controlled Products Systems Group 222EX43 User Manual
Page 22
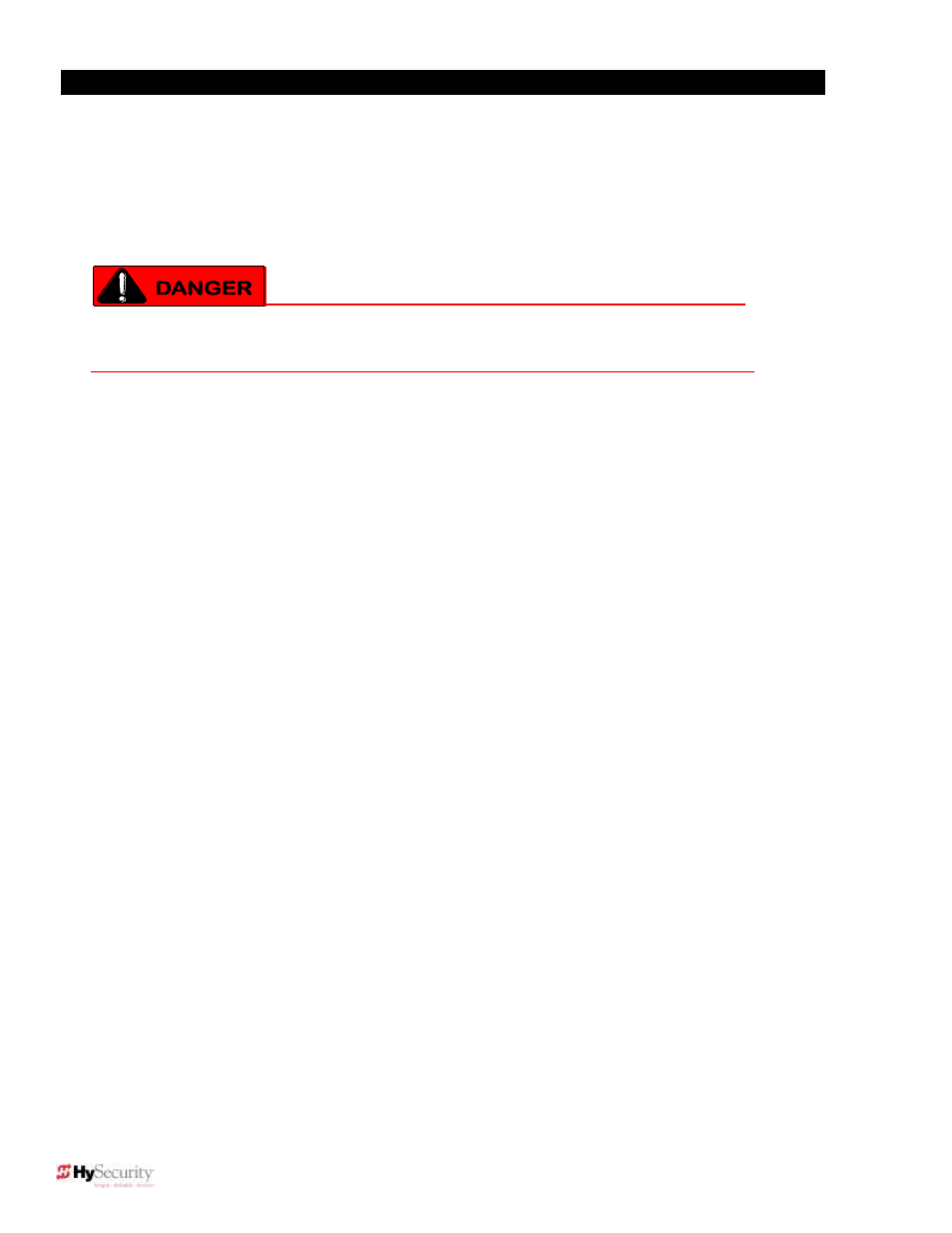
5
© 2012 Installation and Reference Manual D0119 Rev. J
Section 1
— Important Safety Information — READ FIRST!
Site, Gate, Equipment and Regulatory Requirements
The gate moves freely in both directions. Never over-tighten a clutch or pressure relief valve to
compensate for a stiff gate.
The operator will be installed on the secured (non-public) side of the gate.
The operator will be properly grounded and the intended supply voltage matches the voltage
label on the operator.
The potential for lightning discharge exists with all gates, fences, and gate operators.
National Electric Code (NEC) requires a separate earth ground in addition to the required
equipment ground.
HySecurity recommends grounding the operator with a separate ground rod to shield the
operator against electromagnetism and other electrical signals that may cause erratic operation
with or damage to the Smart DC Controller.
NOTE: If you do not ground the operator with a separate ground rod, you risk voiding the
Limited Warranty.
The gate operation controls have been mounted far enough away from the moving gate such
that users cannot touch the gate while operating the controls. All easily accessible controls must
have a security feature to prevent unauthorized use.
The operator controls will be located in line-of-sight to the gate. Radio controls and other remote
access controls must be connected only to the Remote Open input.
Required external entrapment sensors will be installed. Be certain to carefully review the
instructions for placement, installation and adjustment of these external entrapment sensors.
External entrapment sensors must function to reverse the movement of the gate in both
opening and closing directions. If edge (contact) sensors are used, they are to be mounted
on the leading and trailing edges of the gate, as well as post mounted on the inside and outside
of the gate (See illustration on page 4). If photo eyes or other non-contact sensors are used,
they are to be mounted in locations most likely to guard against entrapment. A combination of
contact and non-contact sensors may be used, but all must be recognized components under
the UL 325 standard. See page 32 for details on the requirements.
If entrapment protection is provided by a continuous pressure actuation control, a placard
stating “WARNING” – “Moving Gate has the Potential of Inflicting Injury or Death - Do Not Start
Gate Un
less Path is Clear” must be posted. Additionally, no other activation device shall be
connected and no automatic closing device, of any kind, shall be used.
The automatic operator is labeled as appropriate for both the type and UL usage class of the
gate.
NOTE: Slide Driver 50VF2, 50VF2-EFO and 50VF3 sliding gate operators must be installed
only for Class III & IV applications.
Class I: Intended to serve single to four family residential uses
Class II: Multi-family use, or any application intended to serve the general public
Class III: Commercial applications not intended to serve the general public
Class IV: Highest security. Security personnel prevent unauthorized access
Sliding gate operators installed in Class III & IV applications do not have a speed restriction and
the secondary entrapment sensor requirement is met if the system is configured as described
for Class I & II use, or by the following alternative means, such as:
Employing the use of a 100dB buzzer which sounds at least 3 seconds before the gate
moves.
Employing the use of a constant hold-type push button control.