4 setting-up the required technology objects – Siemens Simotion A4027118-A0414 User Manual
Page 76
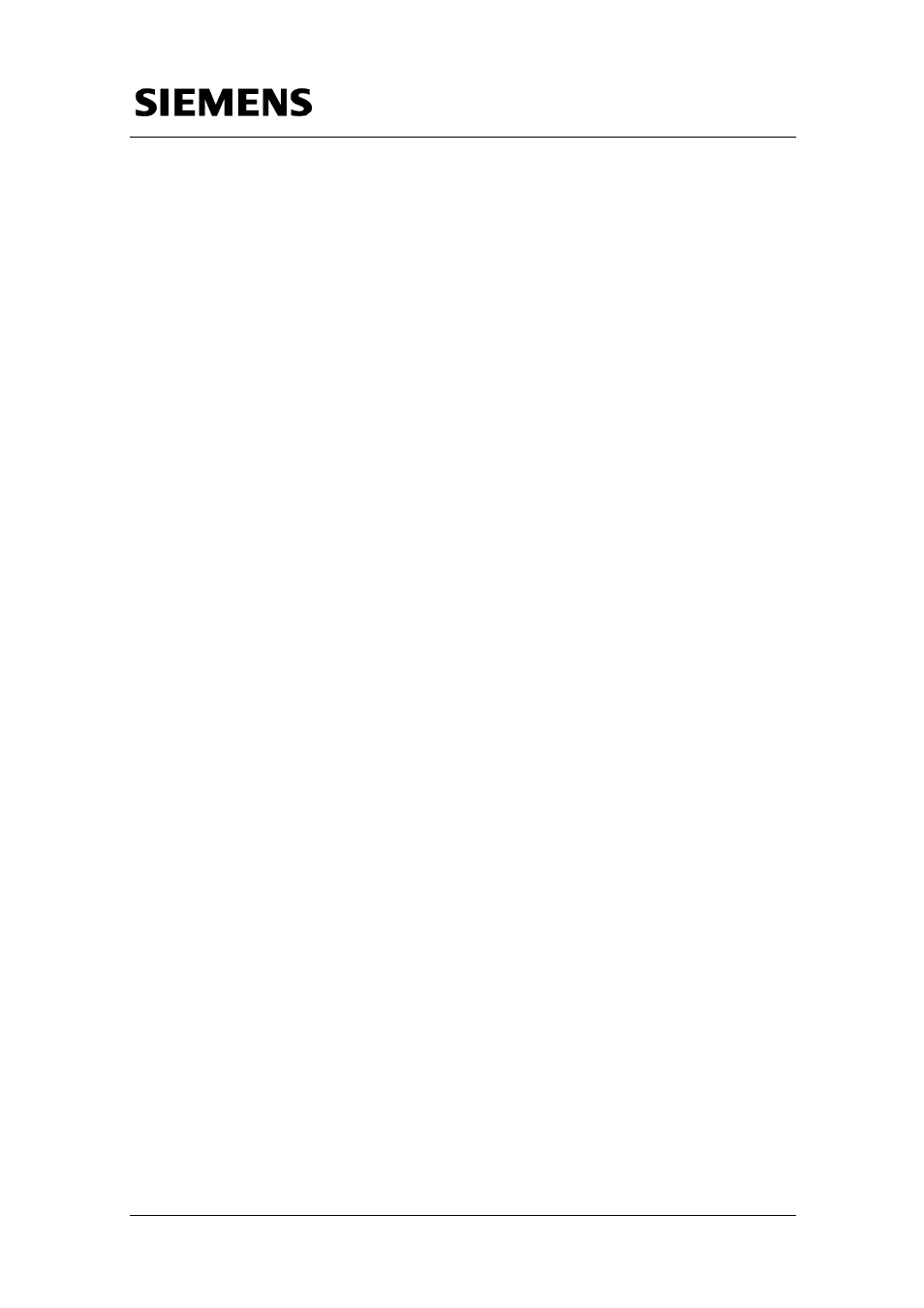
Section C: Integrating the core “flying saw” functions
Integrating the core “flying saw” functions
Flying Saw with SIMOTION
A4027118-A0414
V 1.4
Release 06/06/08
76/107
C
opyr
ight
©
Si
em
ens
AG 2
0
08
Al
l r
ights r
e
s
e
rv
ed
M
anual_
S
IM
OTION Fl
ying Saw
_
V1
.4.
d
oc
7.4
Setting-up the required technology objects
Prerequisite
SIMOTION SCOUT has been started.
The user knows how to apply the SIMOTION SCOUT program.
7.4.1 Flying
saw
axis
Configuration
• Insert a new axis with the name FlyingSawAxis
• Parameterize the axis as synchronous axis
• Set the axis type as linear
• Parameterize
as
modulo axis
with a modulo length greater than the
maximum traversing distance (this is monitored from the FlyingSaw-FB
Æ “parameterizing error”)
• All of the additional parameters should be set corresponding to the drive
and encoder data.
Mechanical system
• For the parameter “distance for each spindle revolution” enter the
distance that the knife tip of the “flying saw” moves through for one
motor revolution.
• Appropriately supplement the other parameters as well as geometry
and design.
Pre-assignment
• Please enter this parameter corresponding to the drive dynamic
performance.
Limits
• Please enter these parameters corresponding to the system layout and
configuration.
Referencing (homing)
• Please enter these parameters corresponding to the encoder
(the template assumes a referenced/homed axis). If an incremental
encoder is used, it is necessary to reference/home the axis in mode 4
“Manual”
before additional operating modes are selected. )