Input and output functions – ITT S-DRIVE IM213 User Manual
Page 19
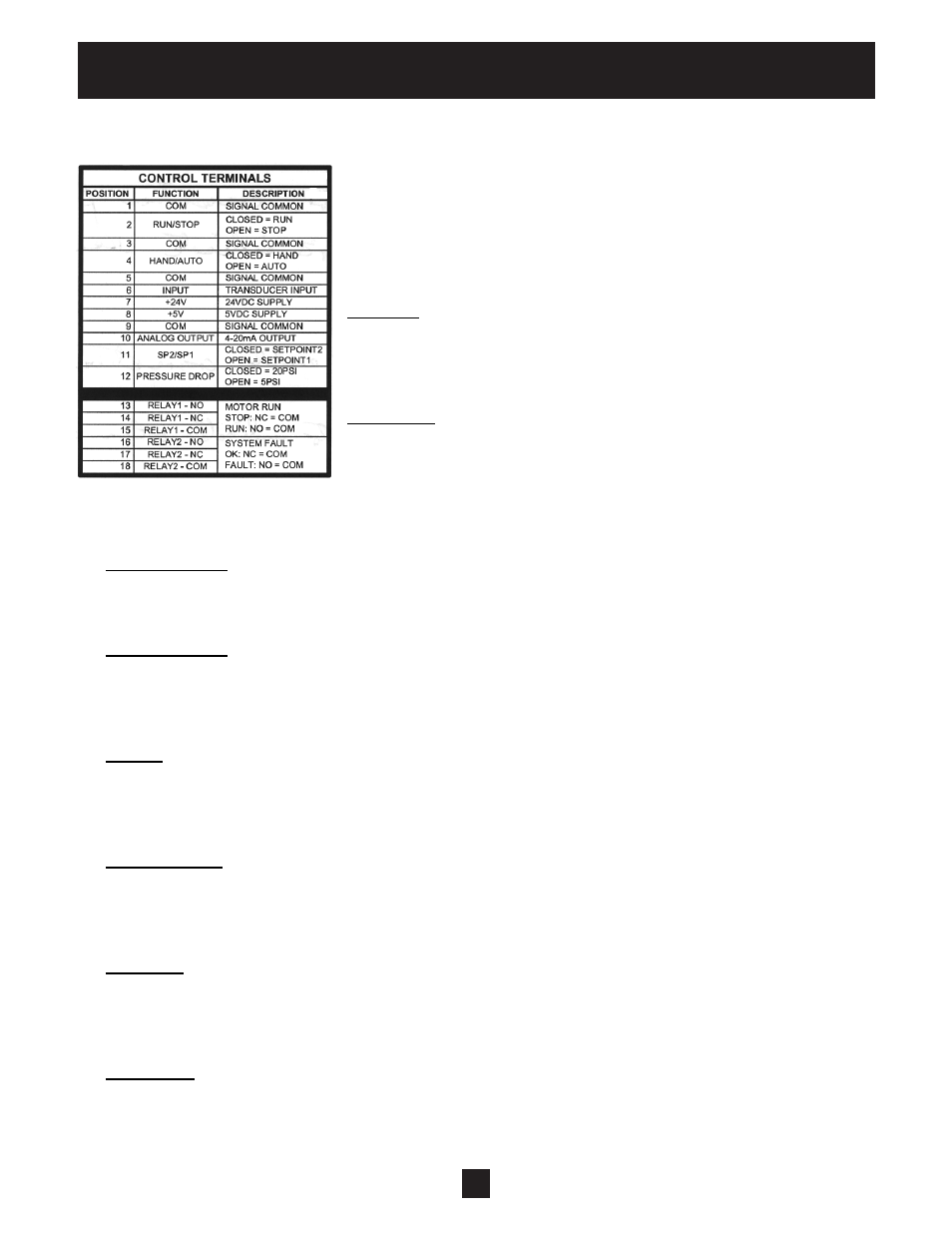
19
Input and Output Functions
Section 8
The control terminal strips allow for a variety of input and output functions.
Warning: Turn off all power to the controller before wiring devices to the
control terminals.
Warning: Inputs RUN/STOP, HAND/AUTO, SP2/SP1 and PRESSURE DROP are
switch inputs. Do not connect power to these inputs or damage to the controller
will result. Only connect non-powered switch contacts to these inputs.
RUN/STOP: This input allows the pump/motor to be turned on and off by an
external switch. Connect the contacts of a non-powered external switch to
terminals 1 (COM) and 2 (RUN/STOP). When the switch is closed the controller
is in RUN mode (output to motor is enabled). When the switch is open the
controller is in STOP mode (output to motor is disabled).
HAND/AUTO: This input allows the controller to run the motor at full speed
without the use of a pressure transducer. This input can be controlled by an
external non-powered switch. Connect the contacts of a non-powered external
switch to terminals 3 (COM) and 4 (HAND/AUTO). When the switch is closed the
controller is in HAND mode. While in HAND mode the RUN/STOP input is used to start and stop the motor and the
pressure transducer input is ignored. When the switch is open the controller is in AUTO mode. While in AUTO mode
the controller uses the pressure transducer feedback to control the speed of the motor.
INPUT and +24V: These terminals are the transducer feedback and transducer power supply. Connect the white
lead from the transducer cable to terminal 6 (INPUT). Connect the brown lead from the transducer cable to terminal 7
(+24V). Connecting the drain (bare) wire to the chassis allows grounding of the case of the pressure transducer. The
controller is configured with a 300 PSI 4-20mA output pressure transducer.
ANALOG OUTPUT: This output is a 4-20mA signal based on motor speed (4mA = 0Hz, 20mA = 60Hz) and can be
connected to external monitoring or external control devices. Connect terminal 10 (ANALOG OUTPUT) to the 4-20mA
input of the external device. Connect terminal 9 (COM) to the negative side of the current loop on the external device.
The external device must have an input resistance (impedance) in the range of 45Ω to 250Ω. The maximum output
voltage is 24V.
SP2/SP1: This input allows the system to operate at one of 2 pressure settings. This input can be controlled by an
external non-powered switch. Connect the contacts of a non-powered external switch to terminals 5 (COM) and 11
(SP2/SP1). When the switch is closed pressure set point 2 is enabled (preset to 75 PSI when used with a 300 PSI
transducer). When the switch is open pressure set point 1 is enabled (preset to 50 PSI when used with a 300 PSI
transducer).
PRESSURE DROP: This input allows the user to select the amount of pressure drop in the system before the pump
starts. This input can be controlled by an external non-powered switch. Connect the contacts of a non-powered
external switch to terminals 5 or 9 (COM) and 12 (PRESSURE DROP). When the switch is closed the system pressure
will drop 20 PSI (when used with a 300 PSI transducer) before restarting the pump. When the switch is open the
system pressure will drop 5 PSI (when used with a 300 PSI transducer) before restarting the pump.
RUN RELAY: This output indicates when the pump/motor is running. This output can be used to control power to a
light, an alarm or other external device. When the pump/motor is off terminal 13 (RELAY1 – NO) will be open and
terminal 14 (RELAY 1 – NC) will be connected to terminal 15 (RELAY1 – COM). When the pump/motor is on terminal
13 (RELAY1 – NO) will be connected to terminal 15 (RELAY1 – COM) and terminal 14 (RELAY 1 – NC) will be open.
The relay rating is 250Vac, 5 amps maximum.
FAULT RELAY: This output indicates when the system is faulted. This output can be used to control power to a light,
an alarm or other external device. When the system is not faulted terminal 16 (RELAY2 – NO) will be open and
terminal 17 (RELAY 2 – NC) will be connected to terminal 18 (RELAY2 – COM). When the system is faulted terminal
16 (RELAY2 – NO) will be connected to terminal 18 (RELAY2 – COM) and terminal 17 (RELAY 2 – NC) will be open.
The relay rating is 250Vac, 5 amps maximum.