Ii - 3 encoders and measured value display – HEIDENHAIN PT 855 for Milling User Manual
Page 94
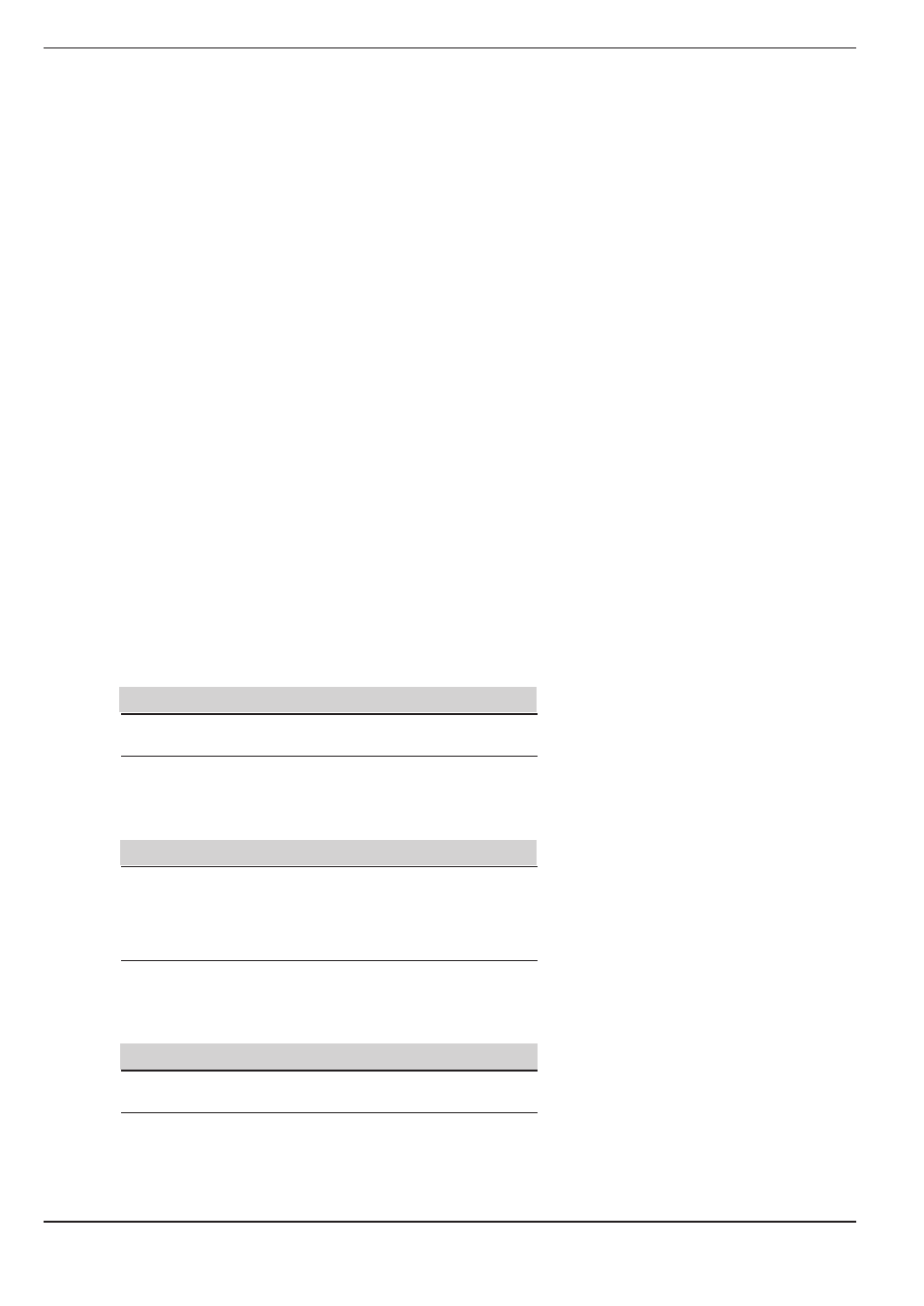
II - 3 Encoders and Measured Value Display
92
Technical Information
POSITIP 855
II - 3
Encoders and Measured Value Display
This chapter describes all operating parameters which you must set
for the encoders and measured value display. Most entries can be
found in the operating instructions for your encoder.
Chapter II - 2 contains a list of operating parameters in which you
can record your entries.
Adapting the encoder
- Encoder output signals 16 µA or 40 µA
- Reference marks on the encoder:
distance-coded or one reference mark
- Deactivation of reference mark evaluation
- Definition of the coordinate axes
- Counting direction of the encoder signals
- Encoder monitoring
- Linear axis-error compensation
Selection of display step
Setting the measured-value display
- Designations of the coordinate axes
- Unit of measurement
- Display of rotary axes
- Angle display
- Axis combination
- Radius/diameter display
Adapting the encoders
Encoder output signal: P81.*
Encoder with 16 µA output signal:
P81.* = 0
Encoder with 40 µA output signal:
P81.* = 1
The position feedback encoders on the machine may have one
reference mark or several distance-coded reference marks.
Reference marks on the encoder: P43.*
One reference mark (none):
P43.* = 0
Distance-coded reference marks (500 TP):
P43.* = 500
Distance-coded reference marks (1000 TP): P43.* = 1000
Distance-coded reference marks (2000 TP): P43.* = 2000
Distance-coded reference marks (5000 TP): P43.* = 5000
Reference mark evaluation can be deactivated separately for
each axis. Note that the datum points for those axes are then
no longer stored in non-volatile memory.
Reference mark evaluation: P44.*
Evaluate reference marks (yes):
P44.* = 0
Do not evaluate reference marks (no):
P44.* = 1