AMETEK DCS-E 3kW Series User Manual
Page 78
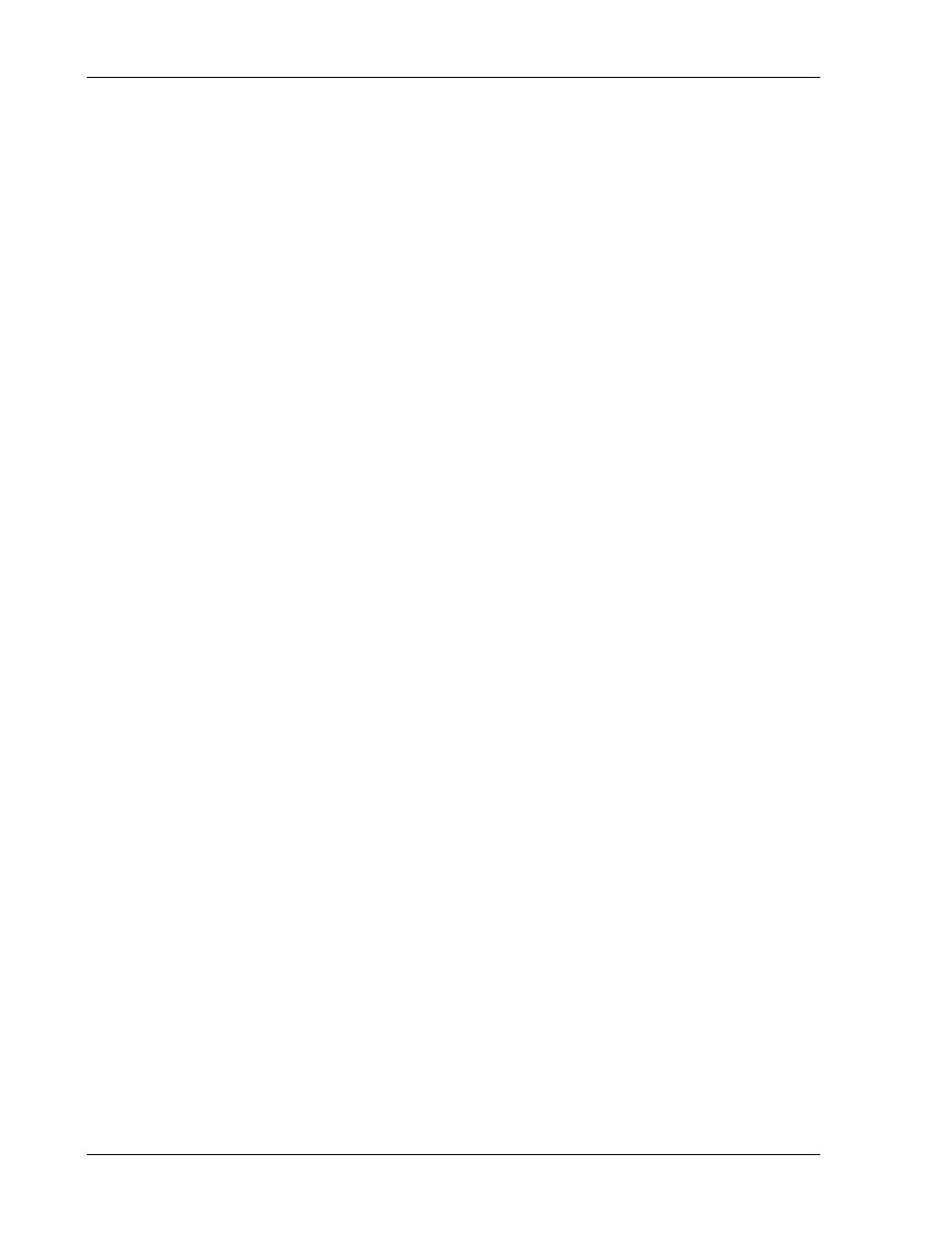
Theory of Operation
Sorensen DCS-E Series 3kW Supplies
5-8
M362295-01 Rev C
signal before inputting it to the PWM current sense comparator at pin 3. A primary side, flyback
winding on T1 and diode CR39 provides the voltage feedback signal for the PWM as well as its
raw supply power. Resistors R121 and R131 scale the voltage feedback signal before it is input
to the inverting side of the PWM error amplifier at pin 2. The output of the error amplifier is input
to the current sense comparator which controls the PWM output pulse width. Four secondary
windings on transformer T1 are diode-rectified and filtered to provide +28V, +15V, -15V and
+5V outputs. The +5V
REFERENCE
is derived from the +15V supply by reference IC U1. The
-6.2V output is derived from the -15V supply by zener diode CR4. Diodes CR31 and CR32,
resistors R107 and R108, and capacitors C45 and C46 form snubbers on the primary of T1 to
limit transients. Resistor R130 and capacitor C61 are compensation components for the error
amplifier. Diode CR38 provides a +18V supply voltage for the inrush limiting and over-voltage
shutdown circuits.
I
NRUSH
L
IMIT
C
ONTROL
, I
NPUT
O
VER
-
VOLTAGE
S
HUTDOWN
,
AND
S
YNC
C
IRCUITS
The inrush limit control circuit monitors the high voltage DC supply and holds the A3 PCB PWM
and the A6 PCB inrush relay K1 OFF until the raw supply reaches approximately 240 Vdc. The
circuit is formed by op amp U14-B, transistors Q8 and Q9, and their related components. On
initial power up, the output of U14-B is held low by a 5V reference signal on pin 6. As the raw
supply voltage increases, the voltage on pin 5 increases until, at a raw supply voltage of
approximately 240 Vdc, the voltage at pin 5 exceeds the reference voltage and the output of
U14-B goes high. This turns ON transistors Q8 and Q9. Q8 energizes the coil of relay K1 on the
A6 PCB which closes the relay contacts and shorts out the inrush limiting resistors R1/R1A.
Transistor Q9 turns on optocoupler U15 which enables the sync signal to the A3 PCB and
allows the A3 PWM to start.
Input over-voltage shutdown is provided by op amp U14-A. U14-A monitors the raw supply
voltage at pin 2 through the voltage divider formed by resistors R109 and R110. When the raw
supply reaches approximately 410V, the voltage at pin 2 exceeds the 5V reference at pin 3 and
the output of U14-A goes low. This pulls the inverting input of U14-B low through diode CR37
and causes the output of U14-B to go low. This turns OFF transistor Q9 which disables the sync
signal to the A3 PWM and activates its shutdown circuit.
V
OLTAGE
C
ONTROL
, C
URRENT
C
ONTROL
, M
ODE
I
NDICATOR
,
AND
I
NTERNAL
S
HUTDOWN
/S
OFT
S
TART
C
IRCUITS
The voltage and current control circuits monitor the output voltage and current from the supply
and provide a feedback signal for the A3 PCB PWM and the A4 PCB down programming
circuits.
The voltage control circuit consists of op amp U3-D and its related components. The output
voltage of the supply is monitored at the inverting input of U3-D (pin 13) through the positive
sense line and the voltage divider formed by resistors R6, R7, R44, and R43. A 0-5V reference
signal at the non-inverting input (pin 12) comes from one of three sources, depending on which
programming mode has been selected. In local programming mode, the reference signal comes
from the front panel voltage control through analog gate U4-C. When remote analog
programming is enabled, the input signal is routed through analog gate U4-B. When the optional
IEEE-488 programming card is enabled, the reference signal is routed to the reference input
through resistor R78. Resistor R10 and capacitors C7 and C8 are compensation components
for U3-D.