Carrier 09DK054-084 User Manual
Page 7
Attention! The text in this document has been recognized automatically. To view the original document, you can use the "Original mode".
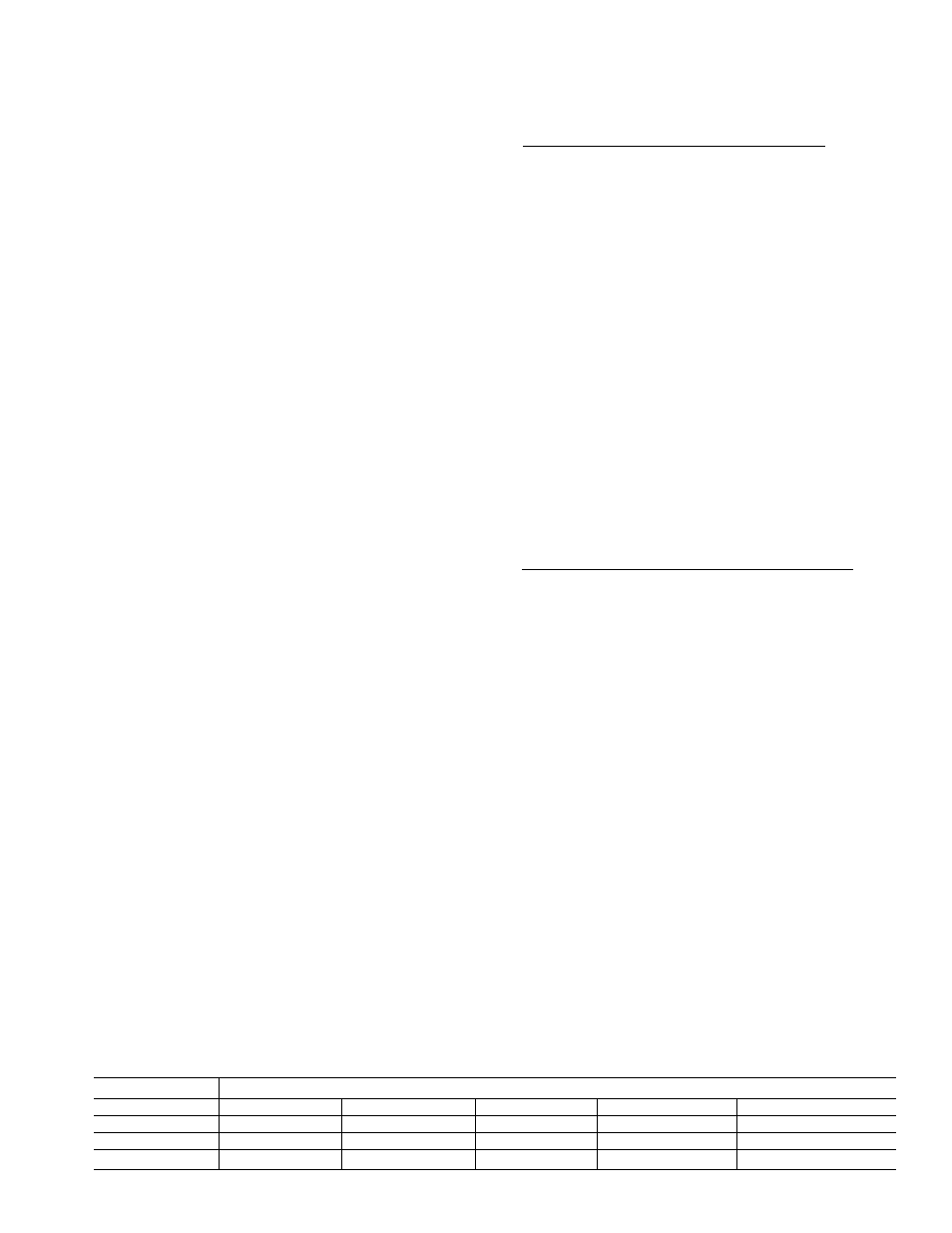
Step 3 — Complete Refrigerant Piping
GENERAL — All field leak and pressure testing should be
in accordance with local code requirements. If a local code
does not exist, use ASHRAE (American Society of Heat
ing, Refrigeration and Air Conditioning Engineers) Stan
dard 15, Safety Code for Mechanical Refrigeration.
For leak testing procedures, refer to the Carrier’s
“Refrigerant Service Techniques” Book, Form SM-IA.
For any parts that need to be removed, use a mini tubing
cutter. Perform phos-copper brazing on all field-made con
nections while protecting adjacent joints from heat.
Install or replace filter-drier(s). BEFORE CHARGING THE
SYSTEM, INSTALL OR REPLACE THE FILTER-
DRIER(S) CONNECTED TO THE LIQUID LINE WITHIN
THE INDOOR UNIT(S) TO PREVENT CONTAMINA
TION WITHIN THE SYSTEM.
COIL REFRIGERANT PIPING INSTALLATION - Hot
gas and liquid connections are located on the same end and
are capped from the factory with a heat shrink-type cap,
which provides a clean joint for field piping. The coil cir
cuiting is designed to provide several selections of coil splits
to satisfy various applications (See Table 2), with piping
connections made in the field. In all cases where circuits
are field connected, the piping connections should be made
within the unit cabinet. The hot gas lines should enter and
the liquid lines should leave the condenser at the header
end of the unit.
As a standard item, a tubing package for headering, in
cluding two fan cycle pressure switches (FCPSs) and hard
ware is provided for the 100, 50/50, and 67/33% typical
condenser coil circuiting options. The tubing also provides
the ports for easy FCPS installations. The ports come with
a 1/4 in. male flare fitting and check valve for each FCPS
replacement. Tubing and FCPSs are field installed regard
less of circuiting. Tubing packages are not offered for the
33/33/33% and 33/33/17/17% coil circuiting options; tub
ing for these coil circuit options must be field fabricated
and installed. See Fig. 5 and 6 for tubing package contents.
NOTE: 67/33, 33/33/33 and 33/33/17/17 represent average
coil split combinations. Refer to sections below for actual
values for your particular coil split combination.
IMPORTANT: With the 67/33, 33/33/33, and 33/33/
17/17% capacity split options, 3 or 4 FCPSs are used.
For these applications, an accessory fan control kit is
required. See accessory installation instructions for more
information.
Figure 7 shows a typical piping application for a condenser
with a multiple-split system. Figure 8 shows the typical field
piping arrangements for the 09DK units. See Fig. 9 for coil
connection details. Figures 10 and 11 show typical factory
supplied coil circuiting and typical field installed 67/33%
coil split circuiting respectively.
TUBING PACKAGE INSTALLATION - Before install
ing, inspect the package contents. If any parts are missing
or damaged, file a claim with the shipping company and
notify your Carrier representative. A field supplied 3/8-in.
conduit (Greenfield conduit recommended) is required
according to UL/CSA (Underwriters’ Laboratories/
Canadian Standards Association) code for the FCPS field
wiring. Field supplied 3/8-in. conduit connectors are re
quired for connection to the junction box.
100% Coil Circuiting Applications: 054. 064 Units
1. Piping
— Refer to Fig. 9 and 12 for field piping details
for 100% coil circuiting. Note that tubes 15 and 22 require
cut on the longer leg of the tube. Two 7/8-in. OD tubes,
approximately 3 in. (76.2 mm) long, must be cut from the
remaining tubes (tubes 21, 23, or 25) and brazed between
the tees (item 8) and coil header stubs. The remaining tubes
are not used in this application and may be discarded.
2. Install Fan Cycle Pressure Switches and Clamps — Braze 2
valve core bodies (item 5) to designated hole locations on
tubes 19 and 22. Insert valve cores (item 6), into valve core
bodies by threading into place and tightening to 1.5 to
3 in.-lb (169.5 to 339 mN-m). Install FCPSl and FCPS2
(item 7) at designated locations on tubes 19 and 22. Cut the
3/8-in. field-supplied FCPS conduit at a desired length to
fit between each FCPS location and the junction box on the
unit. Figure 11 shows a typical installation of the conduit.
Feed FCPS wires through each conduit and secure at the
switch by utilizing each conduit connector. See Fig. 13.
Secure the conduit at the junction box with 3/8-in. field-
supplied conduit connectors. Wire FCPSl and FCPS2
according to Fig. 14. Clamp hot gas line, tube 27, at the
location specified in Fig. 12 using the 1 5/8-in. clamp
(item 4) and the 2 screws supplied. Clamp the liquid line,
tube 24, using the 1 1/8-in. clamp (item 2) and the 2 screws
provided.
50/50% Coil Circuiting Applications: 054 and 064 units
1. Piping —
Refer to Fig. 9 and 15 for field piping details
for 50/50% coil circuiting. Note that tubes 21 and 22
require cuts on the longer leg of the tubes. Two 7/8-in.
OD tubes, approximately 3 in. (72.6 mm) long, must be
cut from the remaining tubes (21, 25, 26, or 29) and brazed
between the tees (item 8) and coil header stubs. The re
maining tubes are not used in this application and may be
discarded.
2. Install Fan Cycle Pressure Switches and Clamps — Braze 2
valve core bodies (item 5) to designated hole locations on
tubes 19 and 22. Insert valve cores (item 6) into valve core
bodies by threading into place and tightening to 1.5 to
3 in.-lb (169.5 to 339 mN-m). Install FCPSl and FCPS2
(item 7) at designated locations on tubes 19 and 22. Cut the
field-supplied 3/8-in. FCPS conduit at a desired length to
fit between each FCPS location and the junction box on the
unit. Figure 11 shows a typical installation of the conduit.
Feed FCPS wires through each conduit and secure at the
switch using each conduit connector. See Fig. 13. Secure
the conduit at the junction box with 3/8-in. field-supplied
conduit connectors. Wire FCPSl and FCPS2 according to
Fig. 14. Clamp hot gas lines, tube 15 at the location spec
ified in Fig. 15 using the two 1 3/8-in. clamps (item 3)
and 4 screws provided. Clamp the liquid lines, tubes 21
and 23, using the two 7/8-in. clamps (item 1) and the
4 screws provided.
Table 2 — Coil Circuiting Options
09DK
09DK CIRCUITING OPTIONS
054
100%
50/50%
66/34
34/34/32
34/34/16/16
064
100%
50/50%
66/34
34/34/32
34/34/16/16
074
100%
50/50%
68/32
32/32/36
32/32/18/18
084
100%
50/50%
67/33
33/33/33
33/33/17/17