Warning – Reznor R6GP Unit Installation Manual User Manual
Page 17
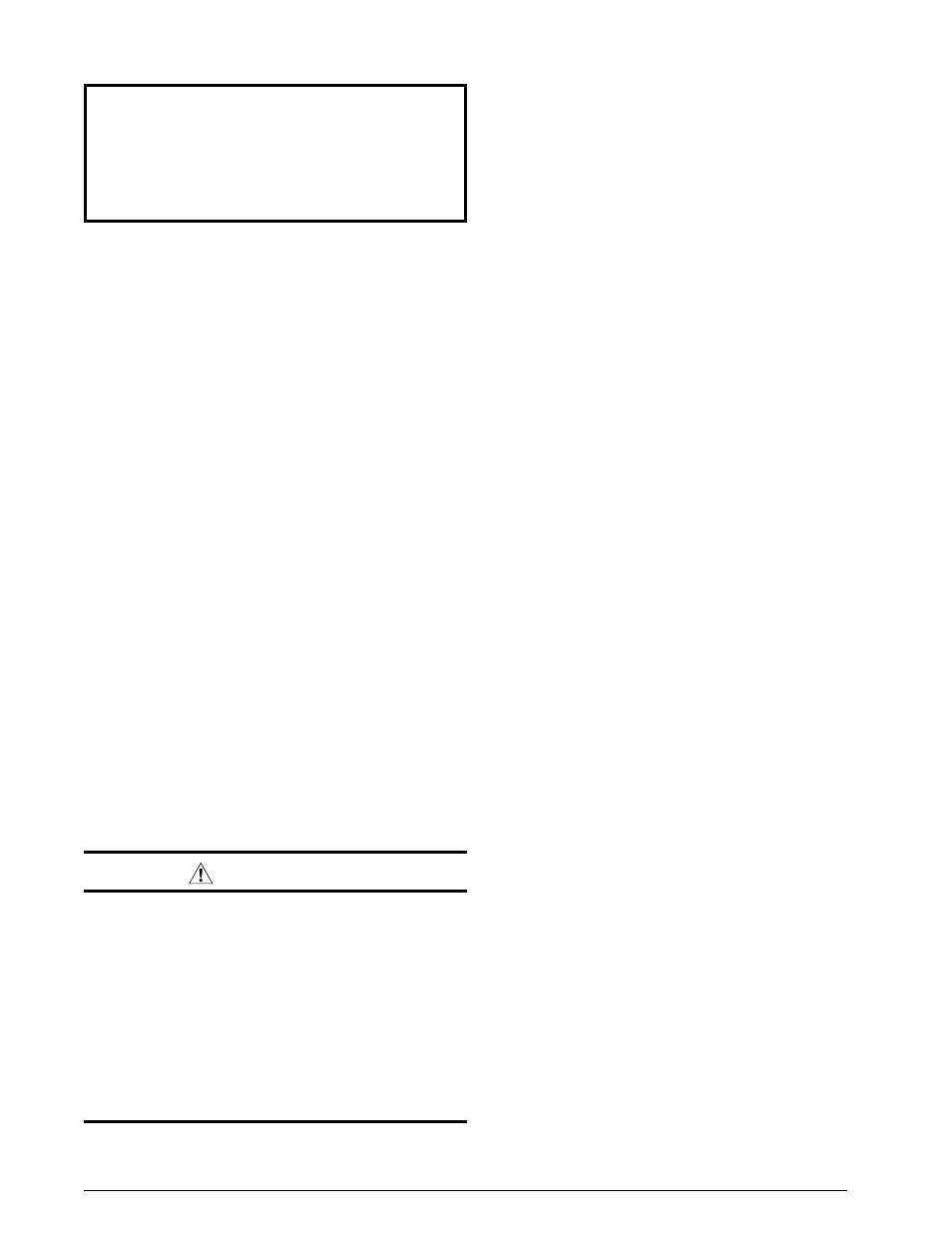
17
Manifold Pressure Adjustment
The manifold pressure for both HIGH and LOW firing rates
must be set to the appropriate value for your installation.
To adjust the manifold pressure for either high fire (Stage
1& 2) or low fire (Stage 1 only) follow these instructions
after identifying the correct regulator spring adjustment
screw from Figure 21 or 22 (Page 45) for your particular
gas valve:
1. Obtain the required input firing rate from Table 15 (page
40). NOTE: The values listed in the table is based on
sea level values. At higher altitudes, the heating value
of gas is lower than the sea level heating value. See
High Altitude Deration section (pages 11 & 12).
2. Turn OFF the gas supply at the manual valve located
on the outside of the unit.
3. Using a 3/16” Allen wrench, remove the plug from the
OUTLET pressure tap (OUTLET side of gas valve). See
Figure 23 (page 46)
4. Install an 1/8” NPT pipe thread fitting that is compatible
with a manometer or similar pressure gauge.
5. Connect the manometer or pressure guage to the
OUTLET pressure tap.
6. Turn ON the main gas supply at the manual valve.
7. Remove the regulator cap. Turn the regulator
adjusting screw clockwise to increase the pressure or
counterclockwise to reduce the pressure.
8. Replace the regulator cap after adjustments are
complete.
9. Turn OFF the gas supply at the manual valve.
10. Disconnect the Manometer or pressure guage.
11. Remove the NPT fitting and reinstall the OUTLET
pressure tap plug. Hand tighten the plug first to prevent
cross-threading. Tighten with a 3/16” Allen wrench.
Refrigerant Charging
WARNING:
If repairs make it necessary for evacuation and
charging, it should only be done by qualified,
trained personnel thoroughly familiar with this
equipment. Some local codes require licensed
installation/service personnel to service this
type of equipment. Under no circumstances
should the owner attempt to install and/or
service this equipment.
Fail
ure to comply with this warning could result
in property damage, personal injury, or death.
Example:
• Time for 1 revolution of a gas meter with a 1 cubic
foot dial = 40 seconds.
• From Table 17 read 90 cubic feet gas per hour.
• Local heating value of the gas (obtained from gas
supplier) = 1,040 Btu per cubic foot.
• Input rate = 1,040 x 90 = 93,600 Btuh.
OPERATING SEQUENCE
The operating sequences for the heating, cooling, and fan
modes are described below. Refer to the wiring diagrams
(Figures 15 & 16, pages 38 & 39).
Cooling Mode
1. On a call for cooling the thermostat closes, applying 24
VAC to Y1, G, & Y2 if Stage 2 cooling is calling.
2. G applies 24VAC to the main circulating blower circuit.
3. Y1 & Y2 apply 24VAC through all safety switches before
energizing their respective contactors.
4. When the thermostat is satisfied the contactors are
de-energized.
5. The circulating blower motor de-energizes immediately.
Heating Mode
1. On a call for heat, the thermostat closes, applying 24
VAC to the W1 terminal (and W2 terminal if Stage 2
heat is required).
2. The integrated control monitors the safety circuit at all
times. If either the roll-out switch or the over-temperature
limit controls open, the gas valve will not energize.
The main blower continues to operate until the over-
temperature limits close, the flame roll-out switch is
manually reset, or the thermostat is satisfied.
3. The integrated control checks all safety switches at
the beginning of each heating cycle. If closed, the
combustion blower performs a 10 second pre-purge.
4. The integrated control will then supply power to the
direct spark ignitor and immediately energizes the gas
valve.
NOTE: Burner operation begins in high fire mode
with both Stage 1 and Stage 2 gas valve energized,
independent of the thermostat call for Stage 2 heat. If
after 30 seconds of operation with no call for Stage 2
heat, the integrated control will resume heating operation
in low fire mode of operation and Stage 2 gas valve is
de-energized.
5. The flame must be proven through the flame sensor in
10 seconds to hold the gas valve open. The integrated
control will monitor the gas flame with the flame sensor
for the entire time the gas valve is open. If for any reason
the gas flame drops out, the gas valve will immediately
close. After 30 second purge, the integrated control will
try to ignite fourteen more times.
6. The main air blower will start and continue to run 40
seconds after the gas valve opens.
7. When the thermostat is satisfied, the integrated control is
de-energized. The gas valve and combustion blower de-
energize immediately while the main air blower continues
The R6 Series packaged gas/electric units are fully charged
at the factory and when installed accordingly, no charging
is required. The refrigerant charge can be checked and
adjusted through the service ports provided on the units.
Use only gauge lines which have a “Schrader” depression
device present to actuate the valve. Refer to Figures 17
- 19 (pages 42 - 43)
Refrigerant charging must be done by qualified personnel
familiar with safe and environmentally responsible
refrigerant handling procedures. See Unit Rating Plate
for the proper type and amount of refrigerant.