Seed delivery troubleshooting – Great Plains YP3025A Operator Manual User Manual
Page 94
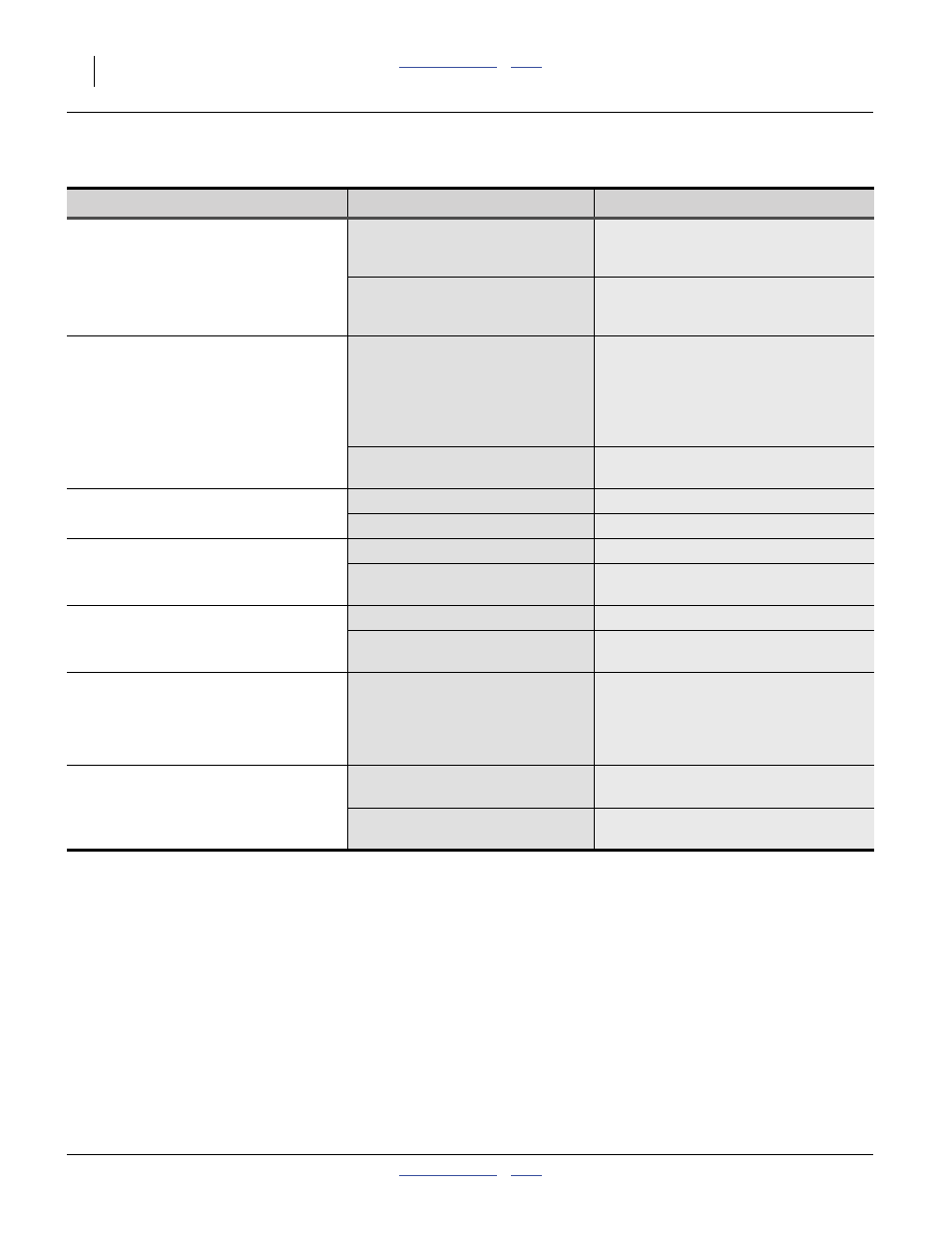
90
YP3025A
Great Plains Manufacturing, Inc.
401-705M
02/16/2012
Null4.aac:
Metadata: End of “Seed Delivery Troubleshooting
Seed Delivery Troubleshooting
Problem
Cause
Solution
Single row doesn’t fill or keep up with
other rows.
Y tube is bent/angled off feed
pipe.
Loosen pipe and spin so the bend is
straight down and Y-tube is not pointing
to front or rear of air pipe.
Drop tube to meter is too long,
causing seed to pool and plug
hose or Y-tube.
Shorten hose (with planter raised, but
row units lowered, to ensure hose is
not too short).
Both rows on one meter outlet low or
not keeping up with other rows.
Blockage in air slot in top of air-
box.
Clear by using a long skinny tool and
taking hose off through hose outlet.
It may be necessary to take top off air-
box or use side access doors to clear
junk from slot.
Bad hose routing between deliv-
ery hose and airbox on wing.
Correct hose routing.
Multiple rows fail for lack of seed.
Fan speed too high/too low.
Check/adjust fan speed.
Out of seed.
Add seed.
Single or multiple hoses plugging just
ahead of airbox.
Fan speed too high/too low.
Check/adjust fan speed.
Possible air leak.
Check for air leak downstream
between box and top of meter.
All rows fail.
Lack of seed.
Fan speed too high. Adjust fan speed.
Extremely high populations may
require slightly reduced field speed.
1, 2, 3, or more outlets fail.
Outlets can be side-by-side or random.
Plugging may also move from one out-
let to another.
Foreign matter in seed chamber in
bottom of airbox.
Clean out seed chamber.
Little or no seed to a lot of rows with
heavily treated seed.
Seed treatment sticky.
Add Ezee Glide Plus to seed to dry out
seed treatment.
Treatment mixed unevenly and
plugging outlets.
Clean out seed. Re-mix.