Fabricator 211i basic welding – Tweco 211i Fabricator User Manual
Page 74
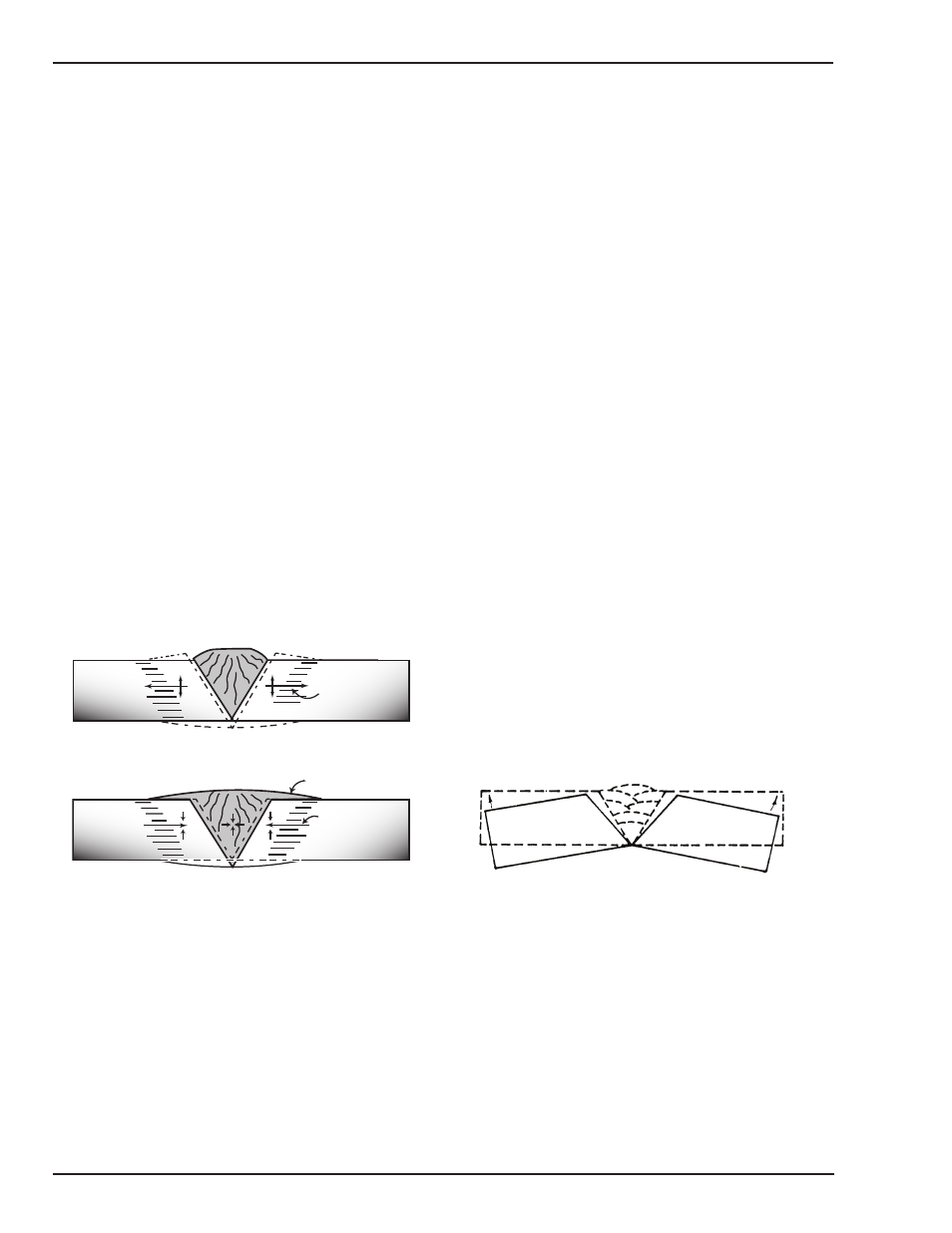
FABRICATOR 211i
BASIC WELDING
BASIC WELDING
4-14
Manual 0-5157
B. Expansion and Contraction of Parent Metal in
the Fusion Zone:
While welding is proceeding, a relatively small
volume of the adjacent plate material is heated to a
very high temperature and attempts to expand in all
directions. It is able to do this freely at right angles
to the surface of the plate (i.e., "through the weld",
but when it attempts to expand "across the weld" or
"along the weld", it meets considerable resistance, and
to fulfill the desire for continued expansion, it has to
deform plastically, that is, the metal adjacent to the
weld is at a high temperature and hence rather soft,
and, by expanding, pushes against the cooler, harder
metal further away, and tends to bulge (or is "upset".
When the weld area begins to cool, the "upset" metal
attempts to contract as much as it expanded, but,
because it has been "upset" it does not resume its
former shape, and the contraction of the new shape
exerts a strong pull on adjacent metal. Several things
can then happen.
The metal in the weld area is stretched (plastic defor-
mation), the job may be pulled out of shape by the
powerful contraction stresses (distortion), or the weld
may crack, in any case, there will remain "locked-up"
stresses in the job. Figures 4-29 and 4- 30 illustrate
how distortion is created.
Art # A-07705_AB
Hot
Hot
Weld
Upsetting
Expansion with
compression
Cool
Figure 4-29: Parent Metal Expansion
Art # A-07706_AC
Weld
Permanent Upset
Contraction
with tension
Figure 4-30: Parent Metal Contraction
Overcoming Distortion Effects
There are several methods of minimizing distortion ef-
fects.
A. Peening
This is done by hammering the weld while it is still
hot. The weld metal is flattened slightly and because of
this the tensile stresses are reduced a little. The effect
of peening is relatively shallow, and is not advisable
on the last layer.
B. Distribution of Stresses
Distortion may be reduced by selecting a welding
sequence which will distribute the stresses suitably
so that they tend to cancel each other out. See Fig-
ures 4-30 through 4-33 for various weld sequences.
Choice of a suitable weld sequence is probably the
most effective method of overcoming distortion,
although an unsuitable sequence may exaggerate it.
Simultaneous welding of both sides of a joint by two
welders is often successful in eliminating distortion.
C. Restraint of Parts
Forcible restraint of the components being welded is
often used to prevent distortion. Jigs, positions, and
tack welds are methods employed with this in view.
D. Presetting
It is possible in some cases to tell from past experi-
ence or to find by trial and error (or less frequently,
to calculate) how much distortion will take place in a
given welded structure. By correct pre-setting of the
components to be welded, constructional stresses
can be made to pull the parts into correct alignment.
A simple example is shown in Figure 4-31.
E. Preheating
Suitable preheating of parts of the structure other
than the area to be welded can be sometimes used
to reduce distortion. Figure 4-32 shows a simple
application. By removing the heating source from b
and c as soon as welding is completed, the sections
b and c will contract at a similar rate, thus reducing
distortion.
Art # A-07707
Figure 4-31: Principle of Presetting