Installation/setup fabricator 211i – Tweco 211i Fabricator User Manual
Page 45
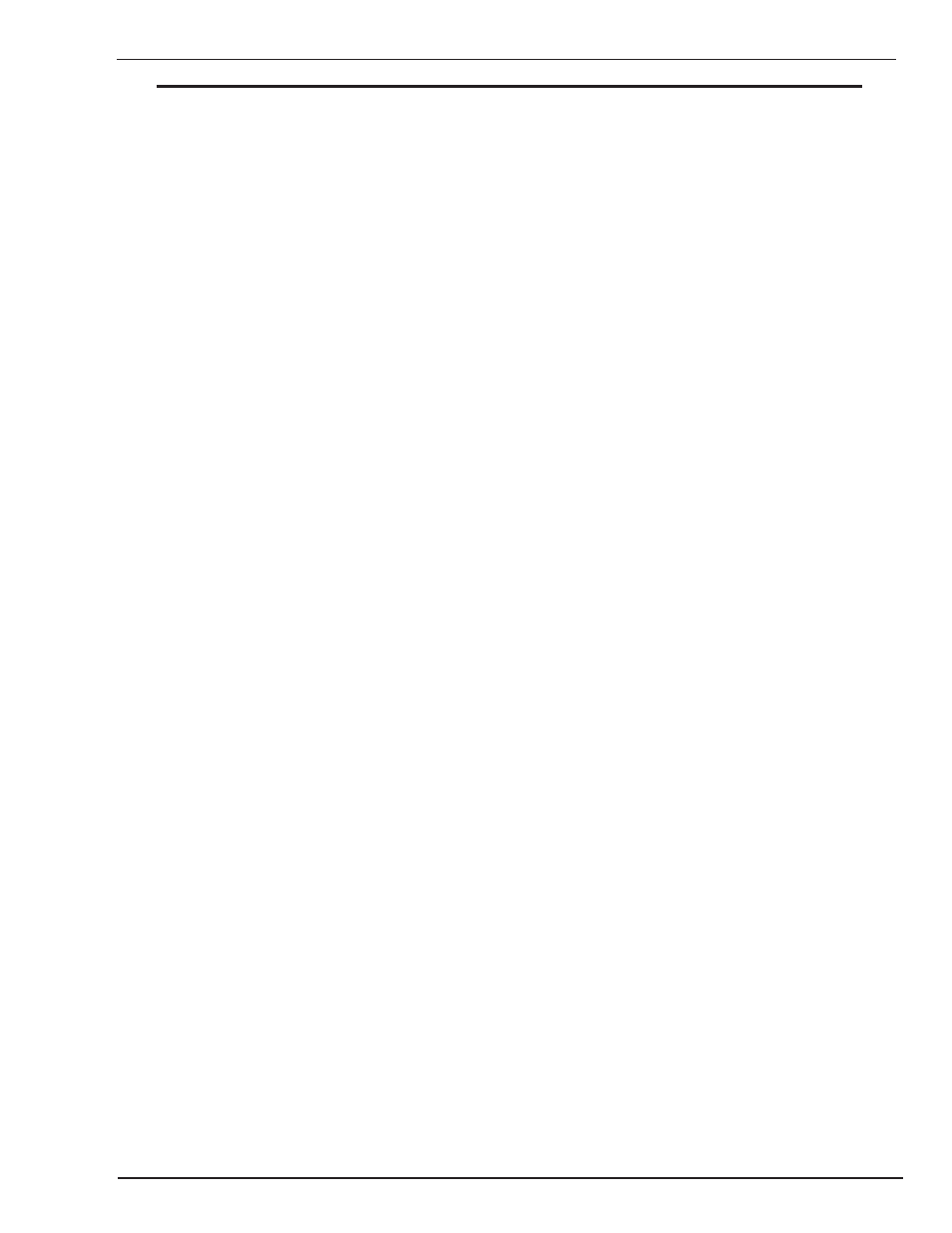
INSTALLATION/SETUP
FABRICATOR 211i
Manual 0-5157
3-13 INSTALLATION/SETUP
NOTE
The preview functionality provided on this power source is intended to act as a guide only. Some differ-
ences may be observed between preview values and actual welding values due to factors including the
mode of welding, differences in consumables/gas mixtures, individual welding techniques and the transfer
mode of the welding arc (ie dip versus spray transfer). Where exact settings are required (in the case of
procedural work), it is recommended that alternate measurement methods be utilized to ensure output
values are accurate.
When MIG Mode is Selected
In this mode the control knob is used to adjust the output voltage of the unit. The welding voltage is increased by
turning the knob clockwise or decreased by turning the knob anti-clockwise. The optimum voltage level required
will dependent on the type of welding application. The setup chart on the inside of the wire feed compartment
door provides a brief summary of the required output settings for a basic range of MIG welding applications.
When STICK Mode is Selected
In this mode the multifunction control knob is used to adjust arc force. Arc force control provides an adjustable
amount of welding force (or “dig”) control. This feature can be particularly beneficial in providing the operator
the ability to compensate for variability in joint fit-up in certain situations with particular electrodes. In general
increasing the arc force control toward ‘10’ (maximum arc force) allows greater penetration control to be achieved.
Arc force is increased by turning the control knob clockwise or decreased by turning the knob anti-clockwise
When LIFT TIG Mode is Selected
In this mode the multifunction control knob is used to adjust down slope. Down slope allows the user to select the
ramp down time at the completion of the weld. The main function of down slope is to allow the welding current
to be gradually reduced over a pre-set time frame such that the welding pool is given time to cool sufficiently.
Note that when in 2T normal mode (refer item 12), the unit will enter down slope mode as soon as the trigger
switch is released (ie if the multifunction control knob is set to 5, the unit will ramp down from the present welding
current to zero over 5 seconds). If no down slope time is selected then the welding output will cease immediately.
If the unit is set to 4T latch mode, to enter down slope mode the trigger must be held in for the selected time
period (ie press and release trigger to commence welding, then press and hold trigger again to enter down slope
mode). Should the trigger be released during the down slope phase (4T only), the output will cease immediately.
11. Arc Control (Inductance)
The arc control operates in MIG mode only and is used to adjust the intensity of the welding arc. Lower arc control
settings make the arc softer with less weld spatter. Higher arc control settings give a stronger driving arc which
can increase weld penetration. Soft means maximum inductance while Hard means minimum inductance.
12. Trigger Mode Control (MIG and LIFT TIG Mode only)
The trigger mode control is used to switch the functionality of the of the torch trigger between 2T (normal) and
4T (latch mode)
2T (Normal Mode)
In this mode, the torch trigger must remain depressed for the welding output to be active. Press and hold the torch
trigger to activate the power source (weld). Release the torch trigger switch to cease welding.
4T (Latch Mode)
This mode of welding is mainly used for long welding runs to reduce operator fatigue. In this mode the operator
can press and release the torch trigger and the output will remain active. To deactivate the power source, the trigger
switch must again be depressed and released, thus eliminating the need for the operator to hold the torch trigger.
Note that when operating in LIFT TIG mode, the power source will remain activated until the selected downslope
time has elapsed (refer Item 10).