Tweco 400 Ultra-Cut(October 2014) User Manual
Page 75
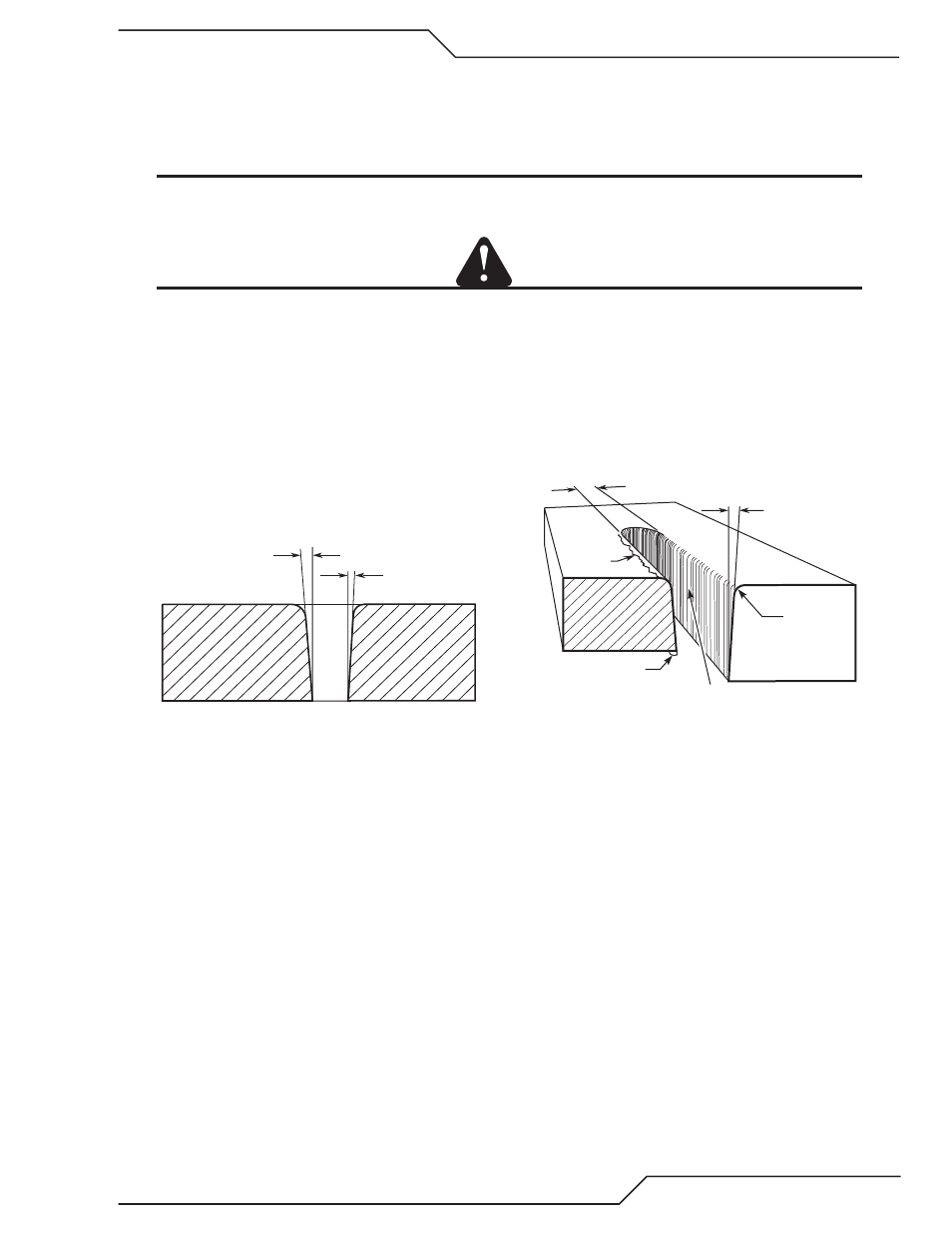
ULTRA-CUT 100 XT/200 XT/300 XT/400 XT
Manual 0-5264
OPERATION
4-11
6. Place the MODE switch to the RUN position.
7. Set the Plasma Power Supply Enable / Disableswitch (on the Gas Control Module) to Enable. The Module
performs purges of 15 seconds, 11 seconds, and another 11 seconds. This removes water from the torch
parts.
NOTE
When switching gases between operations, allow enough purge time to clear the prior gas from the torch
leads.
CAUTION
While nothing prevents the operator from switching gases during piloting or cutting it is not recommended
to do so. If the operator switches gases during piloting or cutting, the power supply will finish the cut with
the first gas chosen. Then the gas control will switch to the new gas. Switching gases during piloting or
cutting may damage torch parts, torch leads, the control module, or the piece being cut.
Cut Quality
Cut quality requirements differ depending on application. For instance, nitride build-up and bevel angle may be
major factors when the surface will be welded after cutting. Dross-free cutting is important when finish cut quality
is desired to avoid a secondary cleaning operation. Cut quality will vary on different materials and thicknesses.
Right Side
Cut Angle
Left Side
Cut Angle
A-00512
Kerf Width
Cut Surface
Bevel Angle
Top Edge
Rounding
Cut Surface
Drag Lines
Dross
Build-Up
Top
Spatter
A-00007
Cut Surface
The condition (smooth or rough) of the face of the cut.
Bevel Angle
The angle between the surface of the cut edge and a plane perpendicular to the surface of the plate. A perfectly
perpendicular cut would result in a 0° bevel angle.
Top-Edge Rounding
Rounding on the top edge of a cut due to wearing from the initial contact of the plasma arc on the workpiece.
Dross Build-up and Top Spatter
Dross is molten material which is not blown out of the cut area and re-solidifies on the plate. Top spatter is
dross which accumulates on the top surface of the workpiece. Excessive dross may require secondary cleanup
operations after cutting.
Kerf Width
The width of material removed during the cut.
Nitride Build-up
Nitride deposits which may remain on the cut edge of the carbon steel when nitrogen is present in the plasma
gas stream. Nitride buildups may create difficulties if the steel is welded after the cutting process.