Description, Operation, Guide to applications – Powers 593 Series Flowrite II Heavy Duty Bronze Globe Control Valves User Manual
Page 3
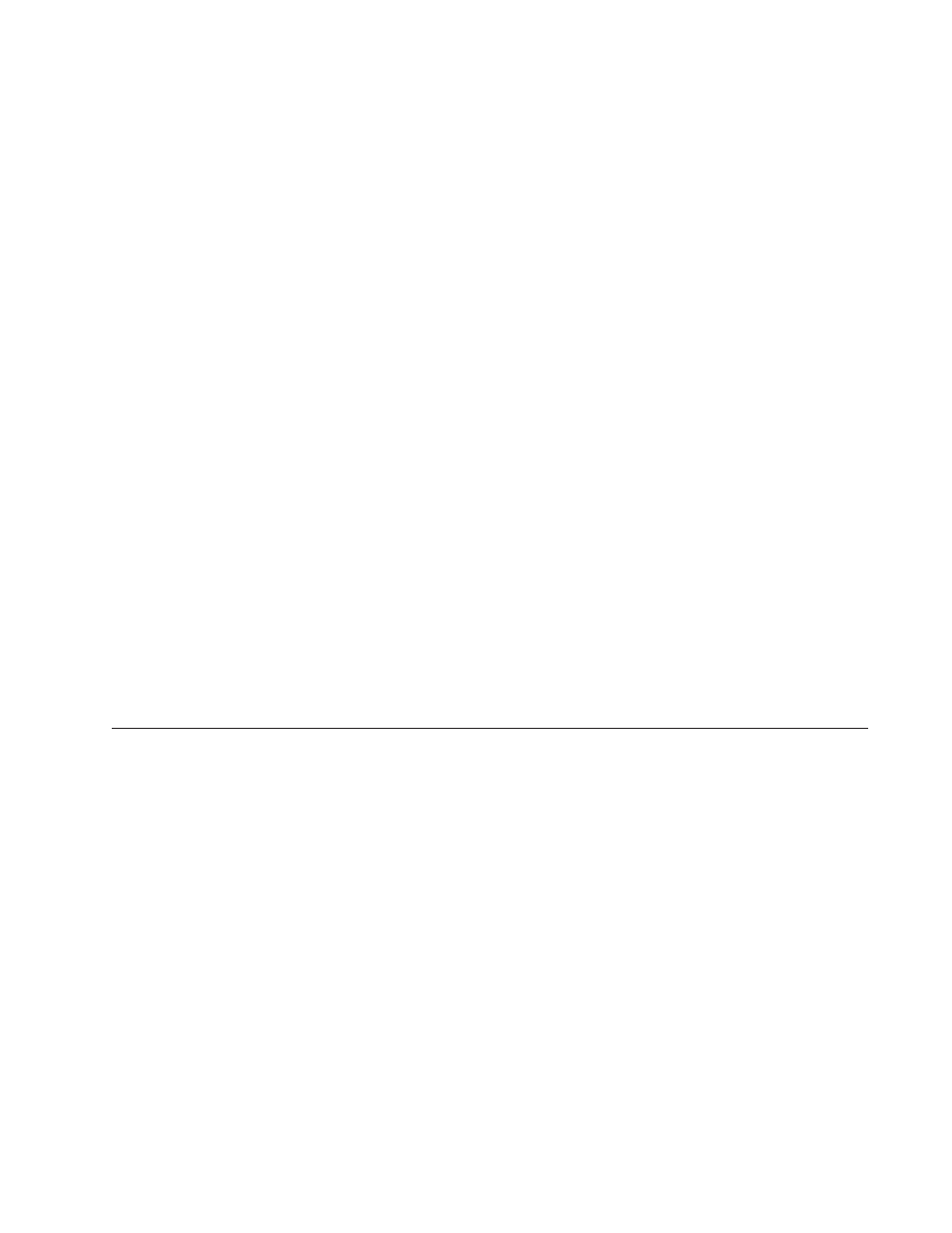
DESCRIPTION
Powers’ most popular actuator, the ‘46’, is a versatile, field reversible
design that is available on most Flowrite II valves. This actuator
provides:
• large effective area (1380 lbs of force at 30 psi) for powerful
valve close control
• excellent narrow range control signal performance
• accurate repetitive positioning due to large diameter
diaphragm, low friction actuator stem and bronze bearings, and
• dual NAMUR accessory mounts.
The 46 actuator and Flowrite II valves are designed to integrate intro a
highly flexible system. It is possible through the Flowrite II 46”
actuation system to adapt to changing application requirements by
reconfiguring the actuator through simple spring changes, stem
changes, etc. The purpose of these instructions is to suggest solutions
to meet your applications needs.
OPERATION
The actuator springs provide the necessary force to hold the stem in
the lowered or raised position.
On a Normally Open valve (ATC, D/A) assembly, the stem will
start its downward stroke whenever the control air pressure applied
against the actuator diaphragm area and upper housing exceeds the
holding force of the springs.
A further increase in control air pressure will initiate a continued
downward travel of the valve stem until the valve has completed its
stroke.
On a Normally Closed valve (ATO) assembly, the valve stem will
start its upward stroke whenever the control air pressure applied
against the actuator diaphragm area and the lower housing exceeds
the holding force of the springs.
A further increase in control air pressure will initiate a continued
upward travel of the valve stem until the valve has completed its
stroke.
The air pressure change to initiate full stem travel is known as the
throttling range or spring span. Standard spring span is equal to 8
psi (55 kPa) with no drop across the valve.
This throttling range is based on typical system pressure and will
vary slightly as the pressure drop across the valve changes. A
decrease in pressure at the diaphragm will initiate an upward
movement on a normally open valve assembly and a downward
movement on a normally closed valve assembly.
When the valve is at its wide open position, the disc and throttling
plug are farthest from the seat and there is maximum flow through
the valve.
Valve actuators equipped with a pilot positioner can utilize full
control air pressure at any point in the stem travel to initiate stem
movement or to maintain stem position.
However, the actuator springs still provide the necessary force to
move the stem in the opposite direction.
Use of a positioner will tend to provide faster response and to ensure
repeatability of stem position regardless of the load on the actuator.
However, in a system where available pressure and flow
requirements are relatively consistent, control valves can usually
perform adequately without a positioner.
GUIDE TO APPLICATIONS
To reverse actuator action, i.e., change an NO to an NC valve,
or an NC to an NO valve:
1. Refer to the Modification Tables for correct replacement parts.
2. Follow instructions for Reversing Actuator Action.
3. Follow instructions for Preload Adjustment.
To attempt valve sequencing with a 3-15 psi air signal OR to set
a NC valve assembly at a higher preload to maintain closeoff or
to increase the throttling range:
1. Refer to the Modification Tables for correct replacement parts.
2. Refer to Changing Springs.
3. Follow instructions for Preload Adjustment.
4. Use dimensions in the Spring Range Matrix.
To modify the actuator action, i.e., using the same actuator on a
different valve body or size:
1. Refer to Modification Tables for correct replacement parts.
2. Refer to Changing Springs.
3. Refer to Changing Action (changing stems).
4. Follow instructions for Preload Adjustment.
5. Use dimensions in the Spring Range Matrix.
To install an actuator on a valve and set the preload adjustment:
1. Follow Installing Actuator instructions.
2. Refer to Modification Tables for correct replacement parts.
3. Follow instructions in Preload Adjustment.
To replace a ruptured diaphragm:
1. Refer to Replacing the Diaphragm instructions.
3