Rockwell Automation AADvance Controller Demo Unit User Manual
Page 11
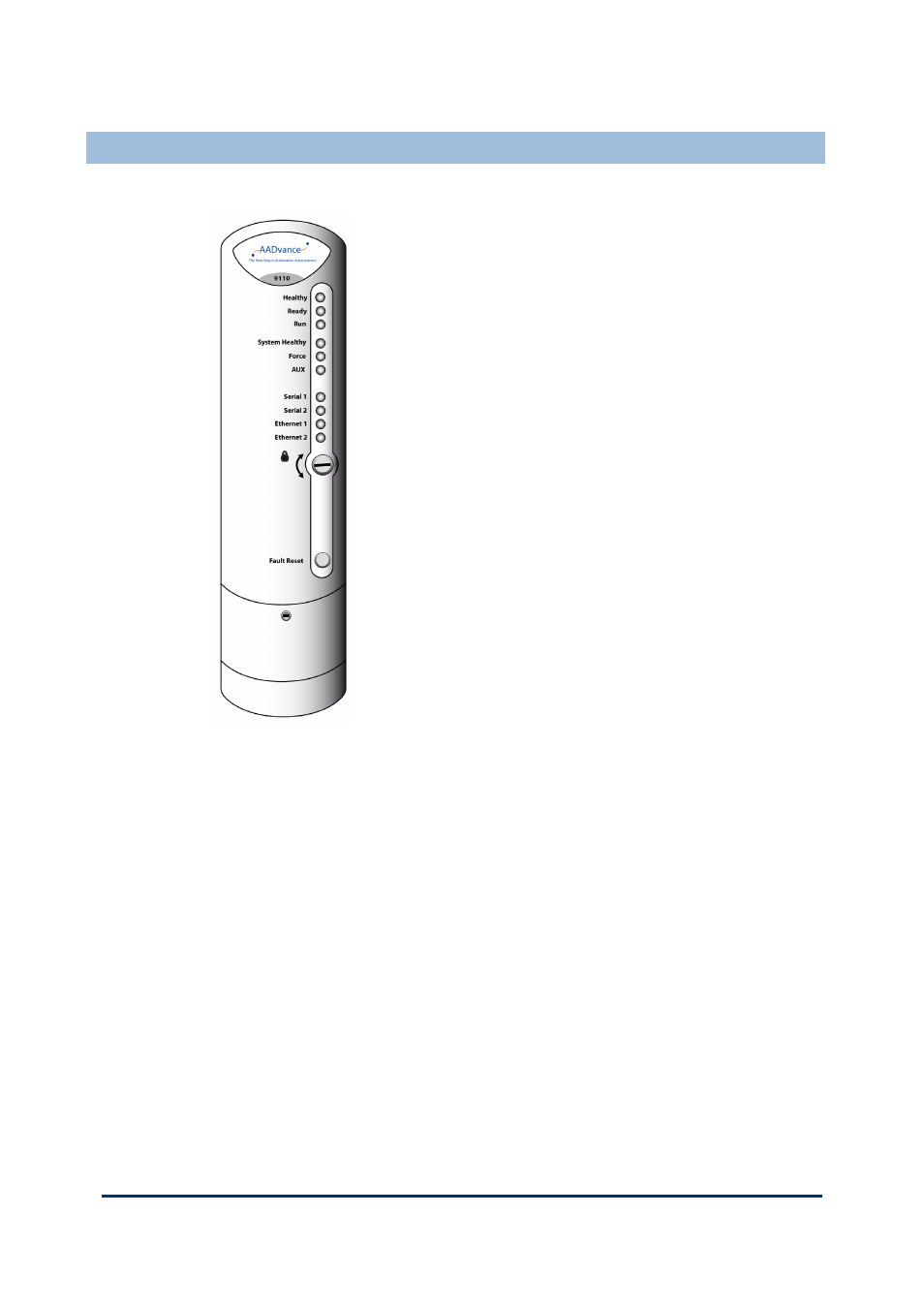
Document: 553850 Issue 1.2: March 2011
1-5
T9110 Processor Module
The T9110 processor module is the central processing unit of an
AADvance controller. The processor module carries out the
following critical process and safety controller tasks:
Execution of the AADvance Safety Kernel to solve
application logic
Interfacing with the controller I/O modules, reading and
processing input data and writing output data
Communication with other processor modules, both locally
and across the control network
Initiation of periodic diagnostics for the controller
Communication with other systems such as HMIs
Message encapsulation and verification for secure channel
communication to other nodes
The processor module is galvanically isolated from external
power supplies and data links so that any faults developed in the
field cannot cause the module to fail. The module will continue
to operate in the event of failure of one of its dual redundant
24V dc power supplies. The module incorporates under- and
over-voltage protection for its internal power supplies, which
provide a 'power valid' signal to the modules own diagnostics
microprocessor.
A processor module has two functionally independent,
electrically isolated Ethernet ports. Each port is separately
configurable for multiple protocols such as Modbus RTU, Open
Modbus/TCP and proprietary AADvance protocols, and its data
is available to every processor in the controller.
Two serial communications ports per processor are provided for Modbus RTU slave
communications. These ports are also functionally and electrically isolated from each
other. They support RS-485 (4– and 2–wire) communications and can be configured to
support asynchronous data rates from 1,200 to 115,200 baud.
The processor periodically initiates internal diagnostic tests which, together with a
watchdog circuit, monitor the processor internal performance. If the tests detect a
serious fault, the processor module will shut down. A controller can use one, two or
three processor modules. Using two or three processor modules provides a fault
tolerant processor architecture.
If a controller uses two or three processor modules, and one processor module
develops a fault, plant maintenance personnel can fit a new processor module while the
controller is on-line. The new processor module automatically carries out self-
education and synchronizes with the other processors. Fault detection and fail-over in
redundant processor configurations is automatic and has no impact on controller
operation.