Troubleshooting, Problem corrective action – Rockwell Automation 160 SER A FRN 1.XX-4.XX User Manual
Page 39
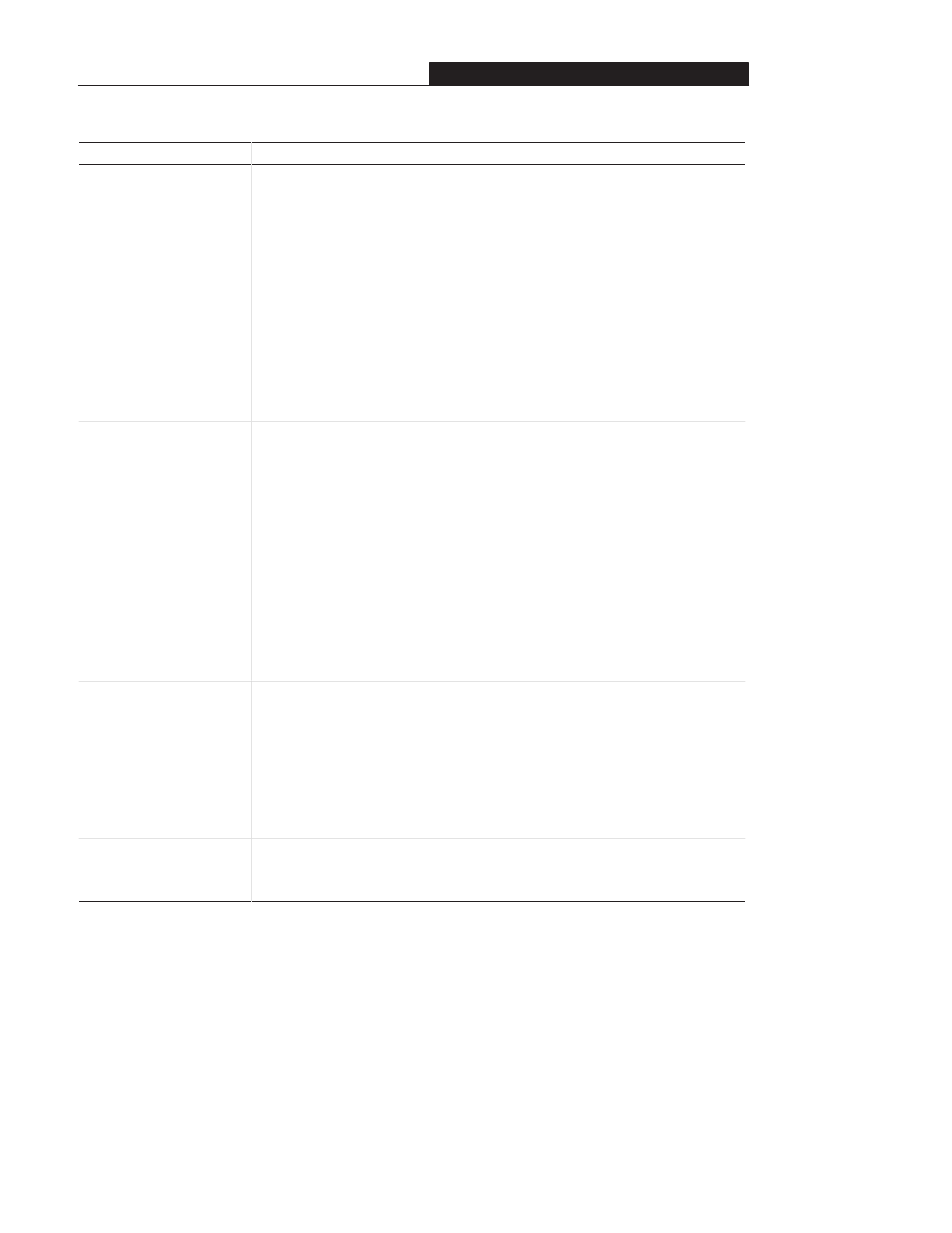
Chapter 6 - Troubleshooting and Fault Information
6–3
Table 6.B Troubleshooting
Problem
Corrective Action
Motor does not start
(No output voltage to motor).
1. Check power circuit.
D Check supply voltage.
D Check all fuses and disconnects.
2. Check motor.
D Verify that motor is connected properly.
3. Check control input signals.
D Verify that START signal is present.
D Verify that STOP signal is present.
D Verify that RUN FORWARD and RUN REVERSE signals are NOT both active.
4. Check P46 - [Input Mode Select].
D If P46 - [Input Mode Select] is set to 2", only the program keypad module Start button will start
the motor.
Controller Started but motor
NOT rotating.
(P01 - [Output Frequency]
displays 0.0").
1. Check motor.
D Verify that motor is connected properly.
2. Check frequency source P06 - [Frequency Command].
D Verify that frequency signal is present at terminal block TB3.
-10Ć +10V signal
4-20 mA signal
D Verify that Preset Frequencies are set properly.
3. Check control input signals.
D Verify that SW1, SW2 and SW3 are correct. (Refer to the chart at the end of Chapter 5).
4. Check parameter settings.
D Verify that P59 - [Freq Select] is showing desired frequency source.
D Verify that P58 - [Internal Frequency] is the desired value.
Motor not accelerating properly.
1. Check motor.
D Verify that motor is connected properly.
D Verify that no mechanical problems exist.
2. Check parameter settings.
D Verify that P30 - [Accel Time 1] or P69 - [Accel Time 2] is set properly.
D Verify that P43 - [Current Limit] is set properly.
D Verify that P38 - [Boost Volts] is set properly.
Can not operate in RUN FWD/
RUN REV" mode.
1. Verify that P46 - [Input Mode Select] is set to 1".
2. Verify that power has been cycled for above change to take effect.
3. Verify that both RUN FORWARD and RUN REVERSE switches are NOT closed simultaneously.