Glossary of terms – USG Manufactured Housing Handbook User Manual
Page 27
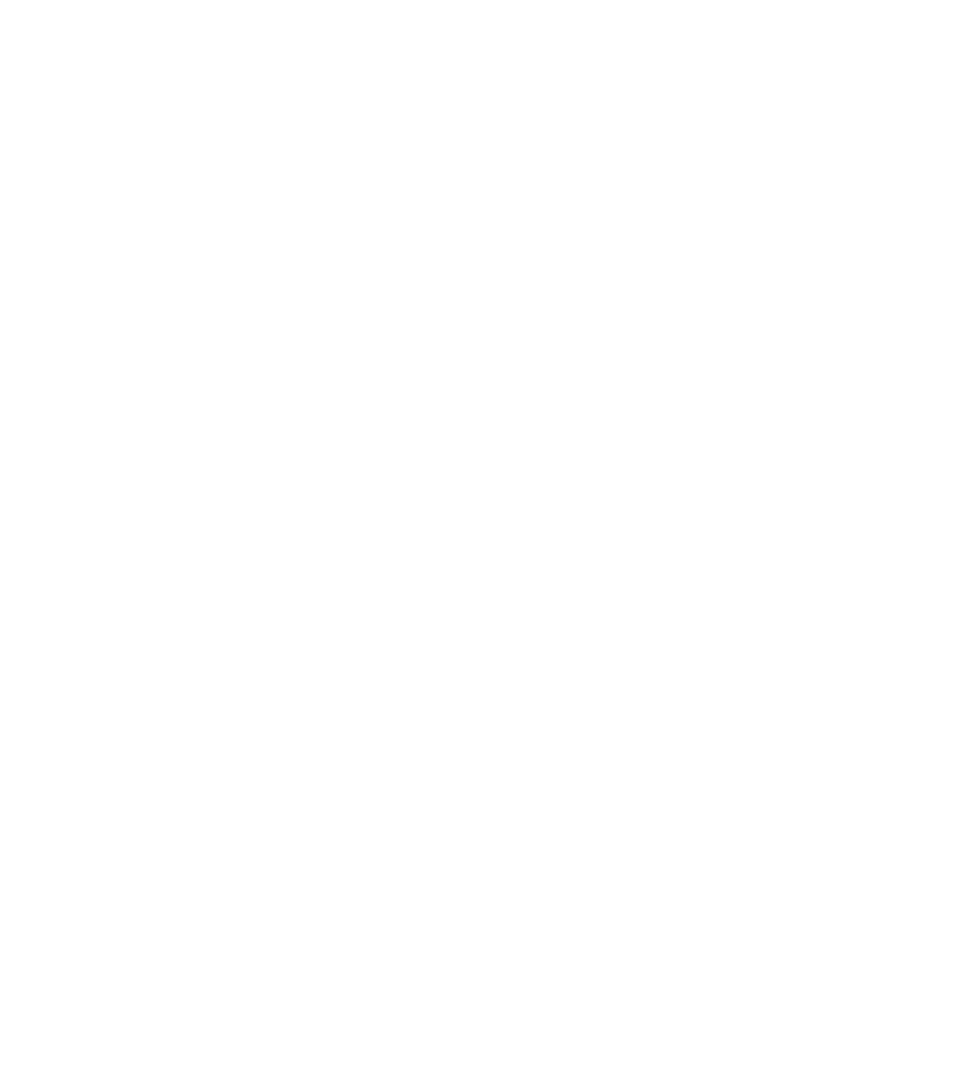
Drying Time—Period of time
required for all water to evaporate
from a product.
Drying-Type—Refers to joint com-
pounds that contain water. These
compounds must be used with paper
joint tape, and allowed to dry com-
pletely for full strength to be
achieved.
Dryness—Degree of change as a
liquid-containing product becomes a
solid material, due to the evaporation
of the liquid from the product.
Various stages of drying are
described by the qualifying terms
used below.
Dust Dry: When dust no longer
adheres to the surface.
Hard Dry: When drying has reached
the stage at which a subsequent
coat of the same material can be
applied.
Surface Dry: When a product is dry
on the surface but is wet, soft, or
tacky underneath.
Touch Dry: When a very slight pres-
sure with the fingers does not leave
a mark or reveal stickiness.
Tack Free: Free from stickiness, even
under pressure.
Dry to Handle: When the product is
sufficiently hardened to be handled
without damage.
Edge-Crack Resistance—
Ability of finished joint compound to
resist cracking along the edges of
the reinforcing tape.
Feathering—Process of smoothing
the outermost edge of the joint com-
pound during application.
Flat Spots—Areas of an aggre-
gated surface having a lesser
amount of aggregate.
Functional Filler—Inert material
used as a bulking agent to add body
in joint compound and texture prod-
ucts.
Halo—Texture pattern that leaves a
different color or appearance around
the perimeter of a ceiling.
Holidays—Also called “voids.”
Skipped or missed areas that are left
uncoated.
Latex—Originally a natural rubber
emulsion, the term “latex” now
applies to a stable dispersion of a
polymer substance in an aqueous
medium.
Melt Back—Shrinkage or soften-
ing/rounding of a spray texture pat-
tern.
Mix Life—Also “wet life” or “pot
life.” Length of time a powder-type
joint compound or texture product
will be usable after being mixed.
Mixability—Ease of mixing of pow-
der-type products.
Powder-Type—Dry products that
are mixed with water prior to use.
Racking—Forcing out of plumb of
structural components, usually by
wind, seismic stress, or thermal
expansion/contraction.
...............................................................................................................................
...............................................................................................................................
...............................................................................................................................
...........
...............................................................................................................................
...............................................................................................................................
...............................................................................................................................
...........
...............................................................................................................................
...............................................................................................................................
...............................................................................................................................
...........
53
Additive—Any substance added in
small quantities to improve the per-
formance properties desired in joint
compound and texture products.
Adhesion—The bonding forces
between two surfaces.
Aggregate—Inert granular mater-
ial, such as polystyrene, perlite,
pumice, or sand, used to create an
aesthetic effect in texture finishes.
All-Purpose Compound—A joint
compound that is suitable for use in
all joint treatment applications.
Atomization—Breaking up of mate-
rial at the spray gun tip/orifice.
Banding—Also called “photograph-
ing,” “striping,” “tracking,” etc. When
dry, the area over the joint is a differ-
ent color from that of the field area.
Usually caused by a difference in
porosity between the joint compound
and the gypsum board.
Binders—Raw materials that bind,
cement, or hold a joint compound or
texture product together, while pro-
moting adhesion of the product to
the surface on which it is applied.
Break Down—(1) How well a
material mixes into a homogeneous,
lump-free mixture. (2) Loss of con-
sistency or viscosity.
Cohesion—Forces that bind the
particles within a product or a sur-
face.
Compatibility—Ability of one prod-
uct or surface to mix with or adhere
properly to another.
Coverage—The amount of surface
area covered by a particular product,
usually described in square feet per
pound. Also known as mileage or
yield.
Cracking—Generally, the splitting
of a film surface. The following terms
are used to denote the nature and
extent of this defect:
Hair Cracking: Very fine surface
cracks that do not penetrate the top
coat, and occur erratically and at
random.
Check Cracking: Fine surface cracks
and breaks that do not penetrate to
the underlying surface, and are dis-
tributed over the surface, giving the
semblance of a fine pattern.
Craze Cracking: resembles check
cracking, but the cracks and breaks
are broader and deeper.
Alligator/Crocodile Cracking: A dras-
tic type of craze cracking that pro-
duces a pattern resembling the hide
of an alligator or crocodile.
Mud Cracking: A severe condition
characterized by a broken network
throughout the surface, and which
has penetrated to the substrate.
Cratering—The formation of small
bowl-shaped depressions in a tex-
ture or paint film.
Drag—Also “ragging” or “tearing.”
When wiping material with a trowel
or broad knife, the material pulls and
sticks on the tool, leaving a torn,
rough edge or surface.
Dry Hide—Ability of material to
visually hide a substrate when dry.
Glossary of Terms
...............................................................................................................................
...............................................................................................................................
...............................................................................................................................
...........
...............................................................................................................................
...............................................................................................................................
...............................................................................................................................
...........
52
...............................................................................................................................
...............................................................................................................................
...............................................................................................................................
...........