USG Manufactured Housing Handbook User Manual
Page 15
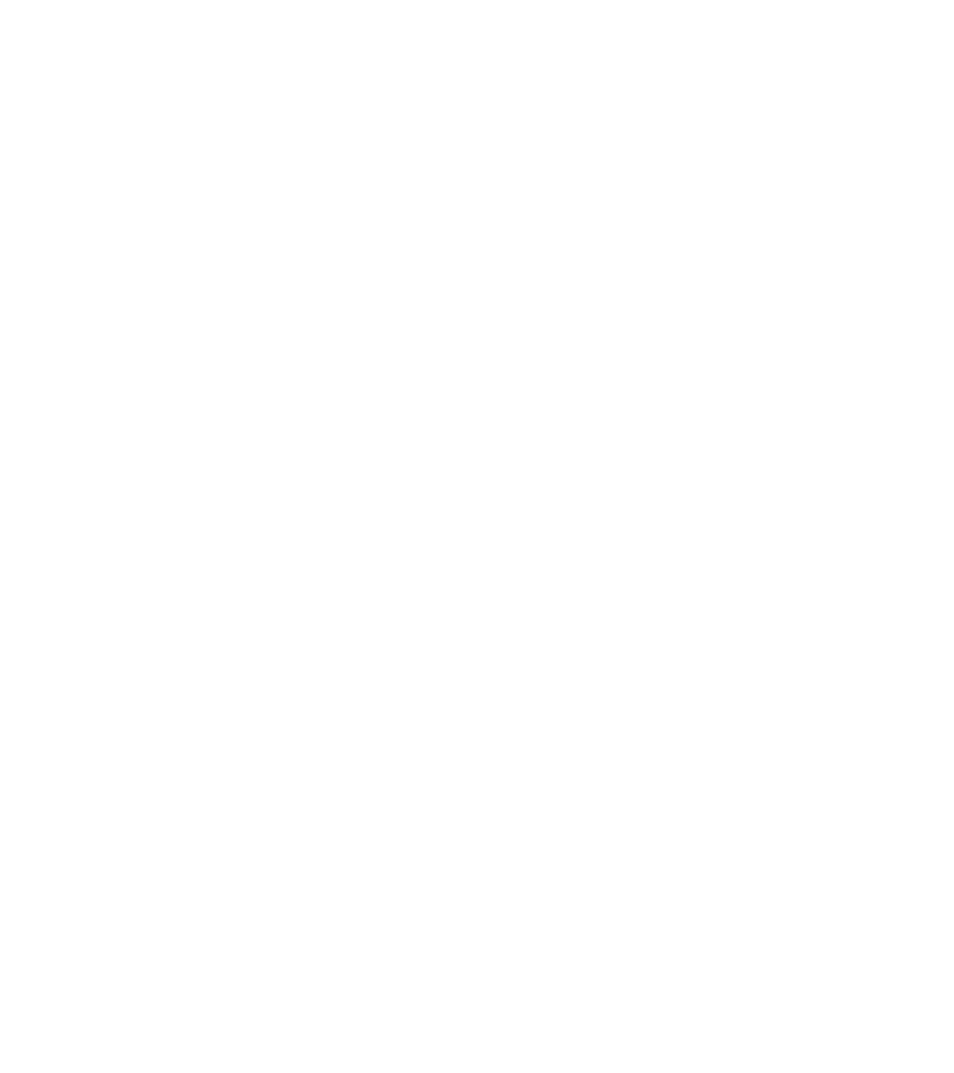
CAUTION
Do not use hot water for mixing.
Hot water will cause lumping in
the mix, and will not provide any
benefit to the texturing operation.
To thin a paste product—that is,
ready-mixed texture—use a
heavy-duty electric drill fitted with
a suitable mixing paddle. Operate
at not over 450 rpm with drill pad-
dles completely submerged at all
times. Mix until compound has a
creamy texture, then add water to
obtain proper consistency for tex-
ture effect desired. Add water in
1/2-pint increments and stir after
each addition.
23 Application
On piston pumps, the larger the
pump, the easier the pumping. It
is difficult to give hard and fast
rules for pumping pressures since
there are many variables.
Consistency of the texturing
material, length and size of hose,
condition of hose and pump, and
pumping height all determine the
air pressure.
On a Roto-Stator, the motor
should be running at about half-
speed, with the machine in sec-
ond gear. The variables listed
above determine the speed and
gear setting.
Nozzle size of the material-feed
orifice for QT spray texture fin-
ishes should never be over 1/2 in.
diameter, preferably 3/8 in. or
even 5/16 in.
At start of spraying, make adjust-
ments to mix consistency accord-
ing to bag directions. When proper
mix consistency has been deter-
mined, adjust air and material
feed pressures as needed to
obtain preferred spraying charac-
teristics.
These adjustments should be
made while spraying material
back into the mixing tank and not
onto the surface to be textured.
When starting to spray, always
take care to have atomization air
pressure “on” before turning on
material feeds. To activate pump,
turn on “mechanical man.”
At this point, you can tell if the
material is pumping normally and
has good atomization. If no
adjustments are necessary, spray
the surface. Keep air pressure as
low as possible while maintaining
good spray pattern. Do not exceed
recommended coverage, since
color differences may show
through, or a lighter texture may
result. When spraying is com-
pleted or temporarily interrupted,
always turn off “mechanical man”
(pump), then close material feed,
and, finally, turn off atomization
pressure.
Pumping Precautions
Material flow in both single- and
multi-piston pumps is controlled by
poppet or ball valves. The valves
are made of steel, rubber, or plas-
tic, the pistons of rubber or plas-
tic—both parts are subject to wear
and possible damage. Whenever
pumping problems such as a pres-
sure loss occur, it is advisable to
check the valves and pistons for
wear or damage before altering the
texture mix.
CAUTION
With all types of pumping equip-
ment, material having either ver-
miculite or perlite aggregate has a
tendency to stiffen while being
...............................................................................................................................
...............................................................................................................................
...............................................................................................................................
...........
...............................................................................................................................
...............................................................................................................................
...............................................................................................................................
...........
...............................................................................................................................
...............................................................................................................................
...............................................................................................................................
...........
29
appearances, including crowsfoot
and stipple designs.
CAUTION
Heavy water-based textures may
result in sagging of gypsum board
ceilings under the following con-
ditions: high humidity, improper
ventilation, and/or board applica-
tion to framing and insufficient
board thickness for span between
supports.
Heavy-texture finish has two detri-
mental effects. It not only wets the
face paper, but adds to the dead
load that must be borne by the
gypsum panel. A heavy texture,
when wet, weighs as much as 1/4
lb. per sq. ft. Even more important
is the added moisture provided by
application of this material.
Complete drying of texture prod-
ucts should normally occur within
a 24-hour period. In hot-humid or
cold-humid conditions, or in areas
with insufficient ventilation, com-
plete drying could take 2 to 3
days. Note: Application of primer is
to equalize the surface porosity
and to provide a uniform color.
Primers are not intended to
reduce sag potential.
21 Checking Equipment
Spraying with a pole gun usually
involves three hoses: (1) material-
feed hose (supplies material to
nozzle); (2) atomization hose
(supplies air pressure to gun and
to “mechanical man”); (3)
“mechanical man,” a manual
valve for controlling feed pump.
Taping the hoses together eases
handling. Hoses usually are avail-
able in 50 ft. lengths and should
be checked periodically and
repaired as required, since dam-
aged hoses can cause poor
results in application.
Tips
– For mixing, use a clean mixing
vessel equipped with a vari-
able-speed agitator.
– Do not overthin texture materi-
als as poor adhesion, lack of
hide, and texture pattern varia-
tion may result.
– Intermixing with other com-
pounds is not recommended
unless specified.
– Provide minimum 55 °F air,
water, package, material, and
substrate temperature during
and after application.
– Avoid drafts while applying,
but provide ventilation after
application to aid drying.
– For comfort, use a respira-
tor and protect eyes while
spraying.
– Do not use unvented gas or oil
heaters.
– Application in high-humidity
areas is not recommended.
22 Mixing
Inspect mixing tanks and clean
out any rust or soured material.
Mix spray texture first, since it
requires more mixing time to be
lump-free.
To mix powder texture products,
start with slightly less water than
recommended on bag and slowly
add material to water while agi-
tating. Do not overload mixing
motor (causing it to slow).
Disperse all ingredients com-
pletely; add remaining water
according to bag directions, and
allow mix to stand 20 minutes
before use. Textures should be
mixed at a heavier consistency
than needed for spraying, then
thinned to spraying consistency.
...............................................................................................................................
...............................................................................................................................
...............................................................................................................................
...........
...............................................................................................................................
...............................................................................................................................
...............................................................................................................................
...........
28
...............................................................................................................................
...............................................................................................................................
...............................................................................................................................
...........