Problems and remedies – USG Manufactured Housing Handbook User Manual
Page 25
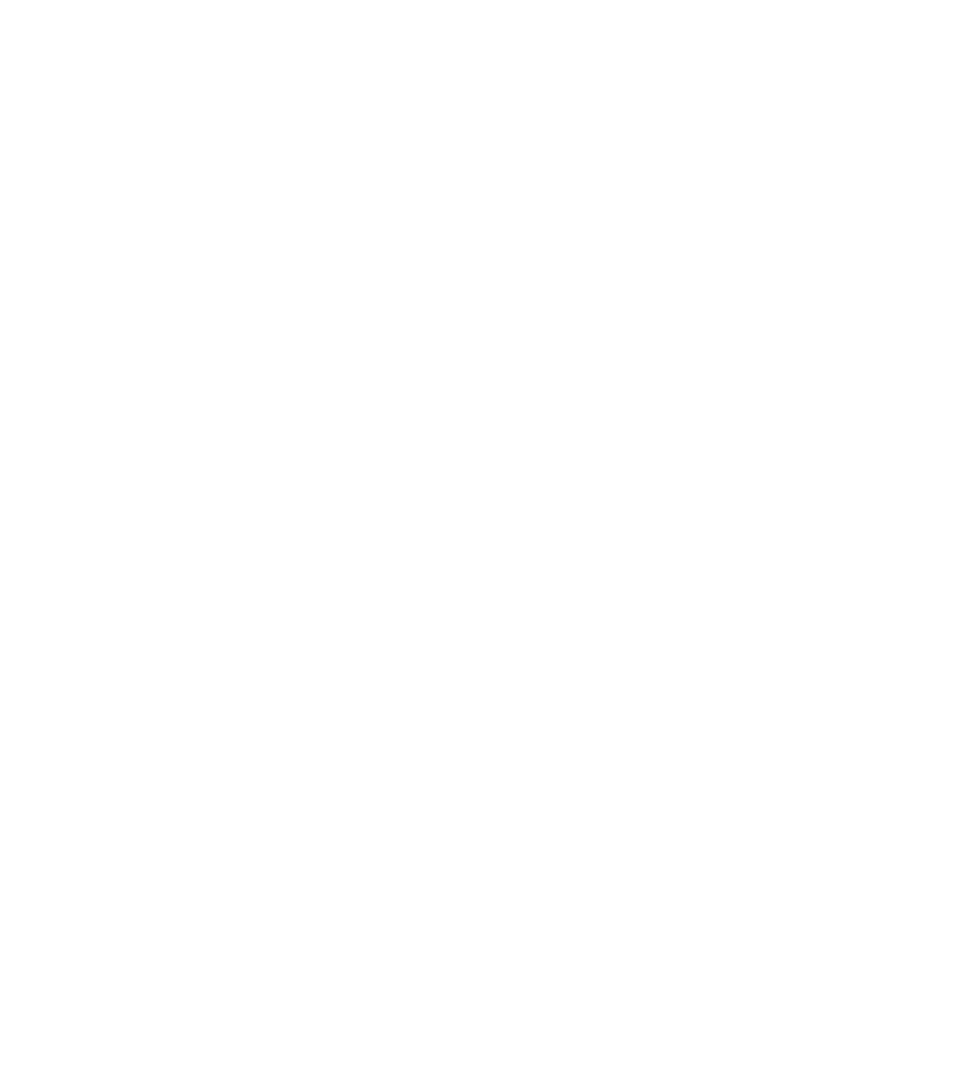
Problem: Mix wet or too thin.
Cause: Overdilution and/or exces-
sive water used during the initial
mix. Also, insufficient soak time in
cold water (this can delay thicken-
ing, giving the user a false impres-
sion of low viscosity).
Prevention: Use recommended
amount of water to ensure proper
consistency. Allow materials to
soak for an extended period when
using cold water.
Texture Finishes—Application
Problem: Excessive aggregate fall-
out.
Cause: Excessive air pressure at
nozzle and/or holding spray gun
too close to surface being sprayed.
Prevention: Use proper spray pres-
sure for type of material to be
sprayed. Hold spray gun at a
proper distance (4 ft. minimum)
from the surface to prevent exces-
sive bounce and fallout of aggre-
gate.
Problem: Flotation of aggregate.
Cause: Overdilution of mix and/or
lack of mixing after water is added
to control consistency.
Prevention: Add the correct amount
of water as directed on the bag to
ensure the proper suspension of
materials in the mix. Make certain
that water is blended thoroughly
into the mix.
Problem: Poor coverage (mileage)
with spray finishes.
Cause: Not enough water being
added to bring texture material to
proper spray viscosity and/or
improper application, such as
moving spray gun too slowly, over-
loading spray surface, or using
incorrect spray pressures and/or
spray gun adjustment.
Prevention: Add proper amount of
water as directed on bag. Use cor-
rect spray gun pressures and
application technique to ensure
uniform texture with optimum cov-
erage.
Problem: Poor hide.
Cause: Overdilution of mix, causing
reduction in wet and dry hiding
power. Insufficient water in spray
finishes causes poor material
atomization, resulting in surface
show-through. Also can be caused
by overextending material, choos-
ing incorrect spray pressures, or
moving the spray gun too fast.
Prevention: Use the proper amount
of water as directed on bag. Use
correct spray gun pressures and
application technique to ensure
uniform texture. Crosshatch the
spray pattern for an even appear-
ance, and to fill in all voids.
Problem: Poor bond or hardness.
Cause: Overdilution of job mix
results in thinning out of binder in
the texture. Contamination or
intermixing with other materials
can destroy bond power.
Prevention: Add proper amount of
water as stated in the bag direc-
tions. Always use clean mixing
vessel and water. Never intermix
with other products or additives,
except those recommended by the
manufacturer.
Problem: Unsatisfactory texture pat-
tern.
Cause: Improper spray pressures,
air/material mix, or worn spray
equipment (fluid or air nozzle).
Also, improper spray consistency
of mix or improper spraying tech-
nique.
Prevention: Use recommended
amount of water to ensure proper
spraying consistency. Check and
...............................................................................................................................
...............................................................................................................................
...............................................................................................................................
...........
...............................................................................................................................
...............................................................................................................................
...............................................................................................................................
...........
...............................................................................................................................
...............................................................................................................................
...............................................................................................................................
...........
49
Joints—Corner Cracking
Cause: Too much compound applied
over tape at apex of angle.
Remedy: After compound is com-
pletely dry, smooth out excess
compound at apex. Fill only hairline
cracks with compound. Do not
apply additional compound, which
will build up.
Prevention: Keep excess compound
from corner, leaving only a small
amount of compound—or none—
in apex.
Cause: Slitting or scoring reinforcing
tape during application. May result
from use of improper tool.
Remedy: If crack extends through
tape, retape and finish.
Prevention: Use proper tool for cor-
ner treatment.
Joints—Shadowing
Cause: Underfilled joint during appli-
cation or delayed shrinkage
(shadow on the joint centerline).
Remedy: Remove texture and fill
joint flush with the board surface
with lightweight setting compound.
Prime and retexture or repaint.
Prevention: Review application
process. Ensure that adequate
compound is applied to make the
joint flush with the board surface.
Use a setting compound with a
shorter set time to eliminate
delayed shrinkage.
Cause: Crowned joint—excessive
compound application above the
surface of the gypsum panel
(shadow to the side of the board
taper).
Remedy: Remove texture; apply set-
ting-type joint compound to both
sides of the joint to feather out the
bulge over 18 inches or more.
Retexture and repaint.
Prevention: Review application
process. Check tools for excessive
bowing or knife edge wear. Leave
compound flush with the board
surface.
Cause: Thin line of compound
bulging out over the center of the
joint (narrow shadow to one side of
joint centerline).
Remedy: Remove texture (try to
scrape down the high spot if possi-
ble) and feather out the ridge over
10
Љ. Retexture and repaint.
Prevention: This condition is called
“hydraulic ridging,” and results
when the applicator tries to fill the
board taper in one pass when there
is a gap between the underlying
panels. The ridge forms behind the
taping tool during application. If
gaps occur between gypsum panels
during assembly, prefill these gaps
with quick-setting compound. Allow
the compound to harden before fill-
ing the board taper.
Texture Finishes—Mixing
Problem: Lumping of wet mix.
Cause: Too much water added to ini-
tial mix, making lumps difficult to
break up, and/or material that has
remained unmixed below the level
of the mixer shaft.
Prevention: Initial mix should use 2
to 2-1/2 gallons of water per bag,
less than the total water recom-
mended. After mixing to a lump-
free consistency, let material soak
for the recommended time, then
add remaining water.
Problem: Slow solution time.
Cause: Insufficient soaking time
and/or use of very cold water.
Prevention: Allow materials to soak
for an extended period after the
initial mix, especially in cold water.
Always use drinkable, room tem-
perature water (at least 55 °F).
Problems and Remedies
...............................................................................................................................
...............................................................................................................................
...............................................................................................................................
...........
...............................................................................................................................
...............................................................................................................................
...............................................................................................................................
...........
48
...............................................................................................................................
...............................................................................................................................
...............................................................................................................................
...........