Problems and remedies, Tips for successful finishing – USG Manufactured Housing Handbook User Manual
Page 24
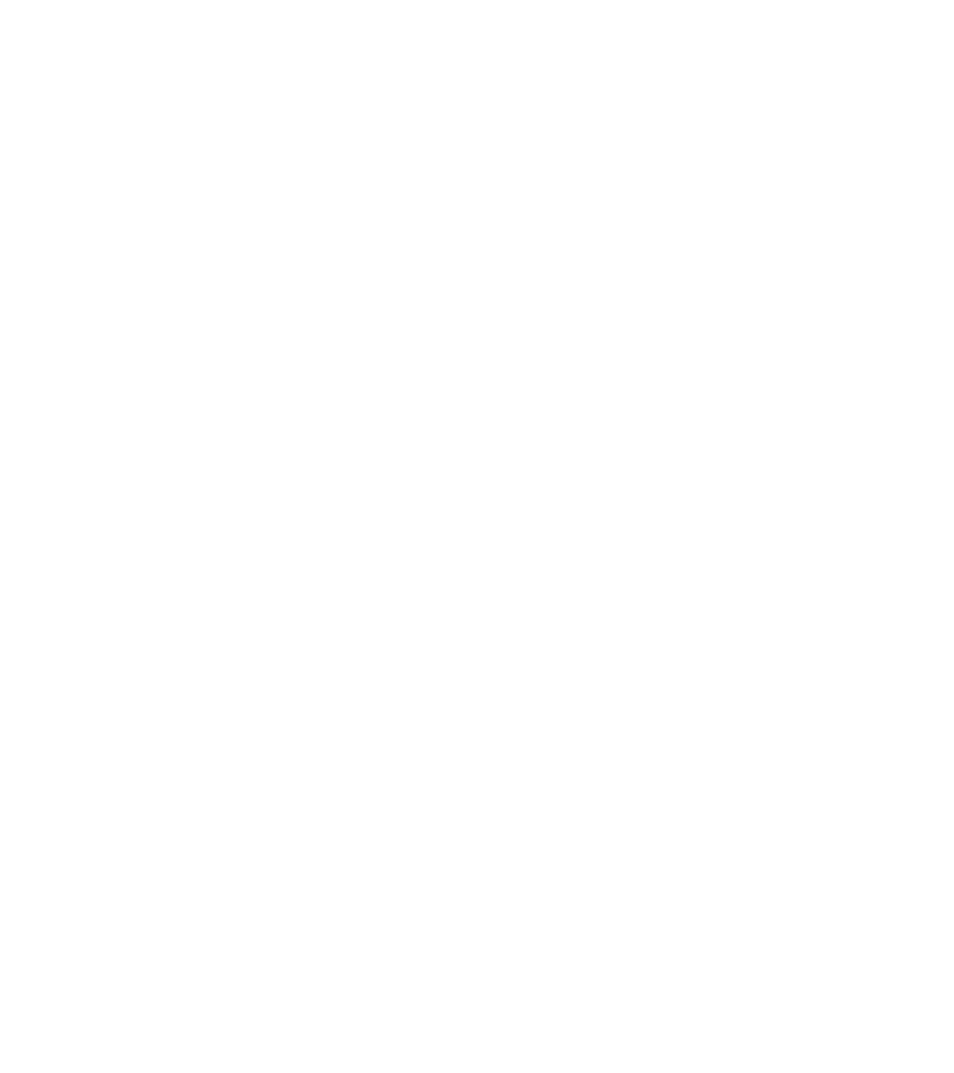
Problems and Remedies
Joints—Center Cracking
Cause: Abnormal stress buildup
resulting from structural deflection
or racking.
Remedy: Relieve stress. Provide
adequate isolation and retape,
feathering joint compound over
broad area to disguise buildup.
Prevention: Provide proper isolation
from structure to prevent stress
buildup. Use a setting compound
that hardens before the assembly
is moved from the finishing sta-
tion.
Cause: Joint compound applied over
dusty surfaces.
Remedy: Remove loose tape and
compound. Retape area, feather-
ing joint compound over broad
area to disguise buildup.
Prevention: Clean drywall of foreign
material (such as drywall dust)
prior to application of tape and
joint compound. Tape and joint
compound applied over dusty sur-
faces will not adhere adequately to
drywall paper. Joint cracking and
tape delamination may result.
Cause: Joint compound over-
thinned.
Remedy: Retape area, feathering
joint compound over a broad area
to disguise buildup.
Prevention: Mix joint compound
according to bag directions. Joint
compound consistency greatly
affects the joint strength of the fin-
ished system. Overthinning of the
joint compound can cause joint
cracking.
Cause: Joint compound not pushed
through mesh tape; compound not
in contact with drywall.
Remedy: Remove tape and loose
compound if necessary. Retape
area, feathering joint compound
over a broad area to disguise
buildup.
Prevention: Make sure compound
pushes through mesh tape and is
in contact with drywall. Overlap
runs when boxing to ensure con-
tact of compound with drywall.
Cause: Setting-type joint compound
force dried prior to setting.
Remedy: Remove tape and loose
compound if necessary. Retape
area, feathering joint compound
over a broad area to disguise
buildup.
Prevention: Allow joint compound to
set prior to force drying with fans
or heaters. Force drying of the joint
compound prior to set will result in
strength loss.
Cause: Joint compound not allowed
to set prior to application of vapor
barrier and texture. Application of
vapor barrier prior to setting action
of joint compound can retard the
set of the compound dramatically.
Remedy: Scrape off any unset joint
compound. Retape area, feather-
ing joint compound over a broad
area to disguise buildup.
Prevention: Allow joint compound to
set prior to application of vapor
barrier and texture. This will ensure
the highest possible wet strength.
...............................................................................................................................
...............................................................................................................................
...............................................................................................................................
...........
...............................................................................................................................
...............................................................................................................................
...............................................................................................................................
...........
...............................................................................................................................
...............................................................................................................................
...............................................................................................................................
...........
47
– Drywall should be clean of foreign
material (such as drywall dust)
prior to application of tape and joint
compound. Tape and joint com-
pound applied over dusty surfaces
will not adhere adequately to the
drywall paper. This can result in
joint cracking and tape delamina-
tion.
– Mix joint compound according to
bag directions. Joint compound
consistency greatly affects the joint
strength of the finished system.
Overthinning of the joint compound
can cause joint cracking.
– The set time of the joint compound
is affected by mix consistency,
mixing time, and water tempera-
ture. A loose initial mix of the joint
compound and/or the use of cold
water will lengthen set time. A
heavier initial mix and/or the use of
hot water will shorten the joint
compound set time. Excessive
drill-mixing of setting-type joint
compounds will also cause com-
pound to set more quickly.
– Push joint compound through
mesh tape. Inadequate contact of
the compound to the drywall sur-
face will result in cracking of the
joint or delamination of tape from
the drywall.
– Joint compound should be allowed
to set prior to force drying with
fans or heaters. Force drying of the
joint compound prior to set will
result in strength loss, delayed
shrinkage, and starved appear-
ance at the joint.
– Allow the joint compound to set
prior to application of vapor barrier
and texture. Application of the
vapor barrier prior to setting of the
joint compound will retard the set-
ting of the joint compound and
contribute to joint cracking.
– Keep application tools clean. Small
pieces of dry compound or texture
can dislodge from the tools and
prevent smooth application of the
compound.
– Keep mixing equipment clean. Set
compound from previous batches
of material will cause the new
batch to set more quickly. This will
reduce working time available and
can lead to wasted material.
Tips for Successful Finishing
...............................................................................................................................
...............................................................................................................................
...............................................................................................................................
...........
...............................................................................................................................
...............................................................................................................................
...............................................................................................................................
...........
46
...............................................................................................................................
...............................................................................................................................
...............................................................................................................................
...........