Interior finishes/ mixing and application – USG Manufactured Housing Handbook User Manual
Page 10
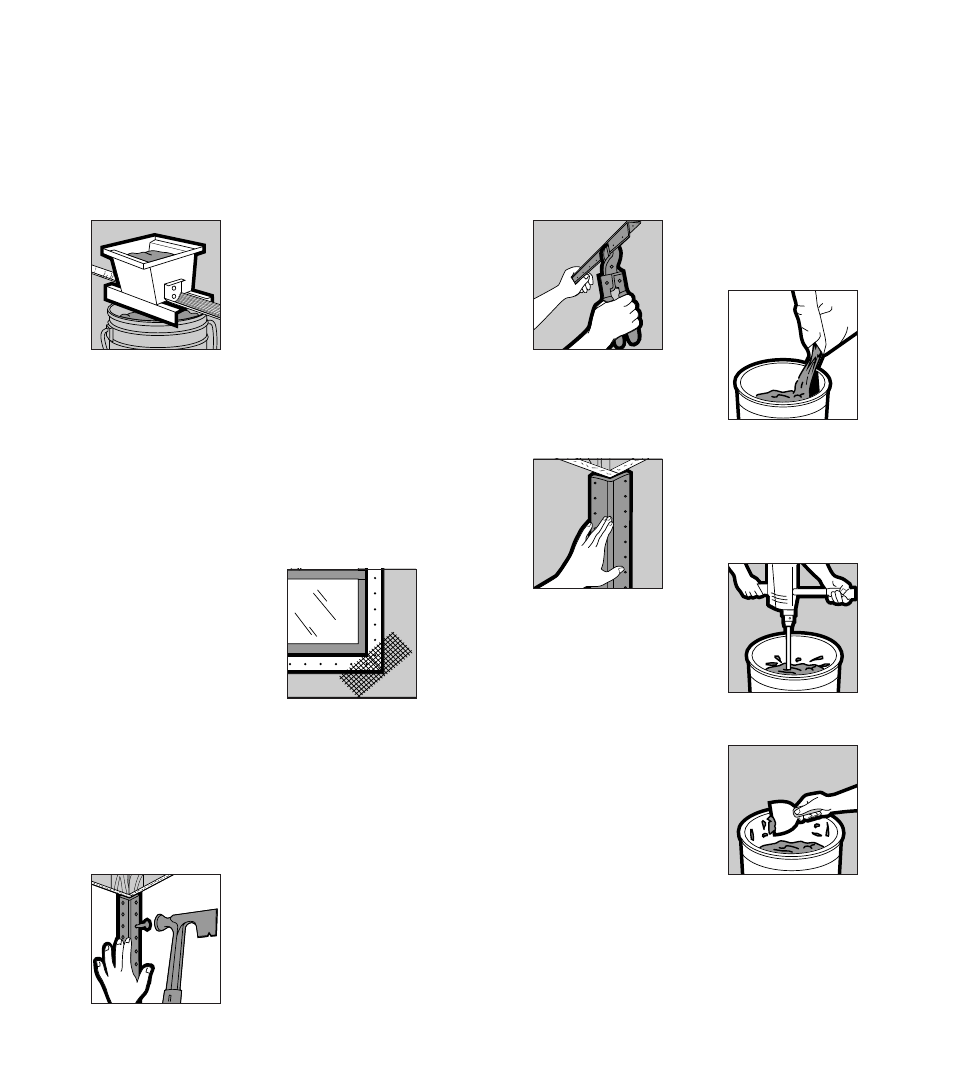
Always be sure to place the hop-
per so that the gate on the exit
side (where the bead, with com-
pound applied, will leave the hop-
per) matches the profile of the
bead.
For more information on the many
sizes and styles of S
HEETROCK
Brand Paper Faced Metal Bead
and Trim, please refer to publica-
tion J996. For additional instruc-
tions on installation, see publica-
tion J1124.
D
UR
-A-B
EAD
Corner Reinforcement
Apply D
UR
-A-B
EAD
Corner Rein-
forcement to all exterior corners
of walls, soffits, and window
returns. Hold bead firmly against
corner and nail bead through
small holes every 9
Љ on each
flange. Start at the midpoint of the
bead and work out toward the two
ends. The fasteners on the
flanges should be directly oppo-
site one another, not staggered.
Make sure that nails penetrate
framing members. Drive all nails
below nose of corner bead and
tightly into flange so that joint
compound will cover smoothly
and evenly. Be careful not to dent
the metal. Screw attachment is
not recommended.
Install USG Metal Trim where gyp-
sum panels butt window or con-
crete block. Nail trim every 9
Љ
through small holes in flange.
Make sure that nails penetrate
framing members.
Mitering
To miter corner bead for trimming
around windows or skylights, begin
with a bead section approximately 3”
longer than the section being cov-
ered. Starting at one end, using tin
snips, cut the outside flange at a 45°
angle down to the nose of the bead.
From this point on the nose, cut the
inside flange at 90°. Hold the bead
against the section of wall and mark
the length on the inside flange. Cut
the inside flange at 90° up to the
nose of the bead. Cut the outside
flange at 45° down to this point on
the nose. The outside flanges should
be longer than the inside. Repeat this
process for the remaining sections.
Crosstaping of mitered corners
(diagonal application of tape, as
shown above) is recommended.
this prevents cracking that can be
caused by movement of the two
sections of bead.
...............................................................................................................................
...............................................................................................................................
...............................................................................................................................
...........
...............................................................................................................................
...............................................................................................................................
...............................................................................................................................
...........
Tips
The easiest way to trim a corner
bead to the correct length is to
cut through the flanges with tin
snips one flange at a time, bend,
and snap at the nose of the bead.
When pushing the bead onto the
corner, be careful that the flanges
do not spread beyond a 90°
angle; this will make it hard to
cover them with joint compound.
The steps that follow are general
guidelines for mixing joint com-
pounds and texture products. For
detailed information concerning pro-
portions, mixing methods, and cau-
tions, please refer to product pack-
aging.
11 Mixing Dry Powder Joint
Compounds and Texture
Products
Always add powder to drinkable
water at room temperature (about
55-70 °F). Make sure that your
tools and mixing equipment are
clean. Refer to package instruc-
tions for exact proportions of
powder and water.
Mix thoroughly by hand or using
a power mixer, as indicated on
packaging. If you are power-mix-
ing, use a mixing paddle
designed for joint treatment and
textures, and use a drill with a
maximum speed of 450 rpm.
Scrape unmixed material from
sides of container and mix again.
...............................................................................................................................
...............................................................................................................................
...............................................................................................................................
...........
...............................................................................................................................
...............................................................................................................................
...............................................................................................................................
...........
...............................................................................................................................
...............................................................................................................................
...............................................................................................................................
...........
19
18
...............................................................................................................................
...............................................................................................................................
...............................................................................................................................
...........
Interior Finishes/
Mixing and Application