Ride-on roller screed components – Multiquip WRS5200 (ORIGINAL COPY) User Manual
Page 25
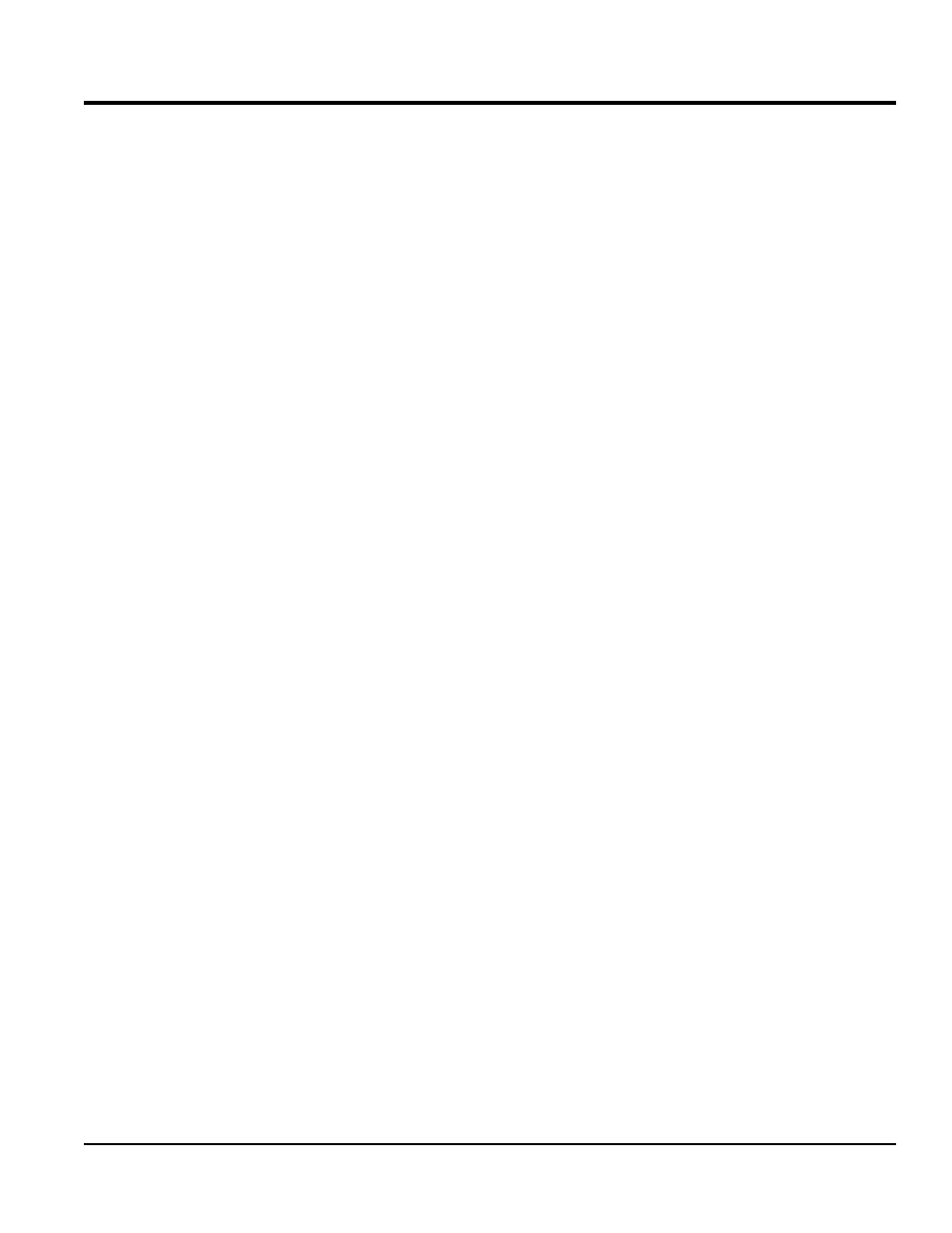
wrs5200 hydraulic roller screed • operaTion manual — rev. #1 (10/22/10) — page 25
riDe-On rOller ScreeD cOMpOnentS
7.
frame (operator end) — 5 foot (1.5 meters) section
that consists of 2 rubber coated drive tubes and
associated hardware. This frame section is located just
below the operators seat.
8.
serial number plate — When ordering parts, use
information on this plate to identify model and type
of unit.
9.
inner plate (operator end) — Included with operators
frame end. Required for the inter-connection of truss
section assemblies. There is also an inner plate at the
power unit end of the screed.
10.
hydraulic hose lines — Always keep hose lines
clean.
do noT allow foreign debris, dirt to enter into
the quick disconnect fittings. Dirt or foreign matter can
contaminate the hydraulic fluid system. Insert Dust cap
into quick disconnect fitting if hose is removed.
11.
protective cover — Attach protective cover to the
various truss sections to prevent the build up of
concrete from accumulating on the frame and hoses.
Utilizing the protective cover greatly reduces cleanup
time.
12.
power unit platform — Place power unit on this plat
form during operation.
13.
power unit — Provides the necessary hydraulics
and electronics to operate the ride-on roller screed.
never tow the ride-on roller screed on the highway
or public roads with the power unit attached to the
screed platform.
14.
Jack hand grip — When manuvering of the screed is
required, grip this handle to position the screed.
15.
Jack raise/lower handle — Turn handle clockwise
to raise screed, turn counterclockwise to lower.
16.
wheel pins — There are 2 wheel pins on each side of
the wheel support. When transporting of the screed is
required, insert pull handle into locking pins.
17.
strike Tube hydraulic motor — Rotates hydraulic
strike tube.
18.
locking pin — To prevent movement of the power
unit and the possibility of the power unit falling from
the platform during operation, insert screed locking pin
into power unit frame.
19.
wrenches — These wrenches are to be used for the
assembly and disassembly of the truss sections, drive
tubes and strike tubes.
20.
middle Bracket — Required when adding truss
sections that will accomodate strike tube.
21.
scrapper — Helps prevents excessive amounts of
concrete from accumulating on the screed frame.
22.
pneumatic Tires — Allows for easy manuvering of the
screed around jobsite.
23.
Truss section — Available in various lengths. See
Table 9.
24.
strike Tubes — Levels concrete surface to grade.
Available in various lengths. Max speed is 450 rpm.
25.
drive Tubes — There are 2 sets of rubber coated drive
tubes that operate independently of each other. Max
speed is 150 rpm.
26.
outer plate (operator side) — Included with
operators frame end. Required for the connection of
strike tube. There is also an outer plate at the power
unit end of the screed.
27.
pull handle — When manuvering of the screed is
required for small distances, insert the hooks on the
pull handle into to the caster wheel pins, then pull on
handle to move screed to desired location.
28.
lift loops — When lifting of the screed is required,
attach lifting straps of adequate lifting capacity to these
lifting loops. Lifting loops are located at each end of the
screed (caster bracket assembly).
29.
strike Tube speed and direction control lever — This
lever controls the speed and rotation of the strike tube.
Push forward for clockwise rotation, pull backwards
for counter-clockwise rotation. The further you push/
pull the lever, the faster the strike tube rotates. Strike
tube speed is variable, full forward or reverse is rated
at 450 rpm.