Enerpac E-Series User Manual
Page 5
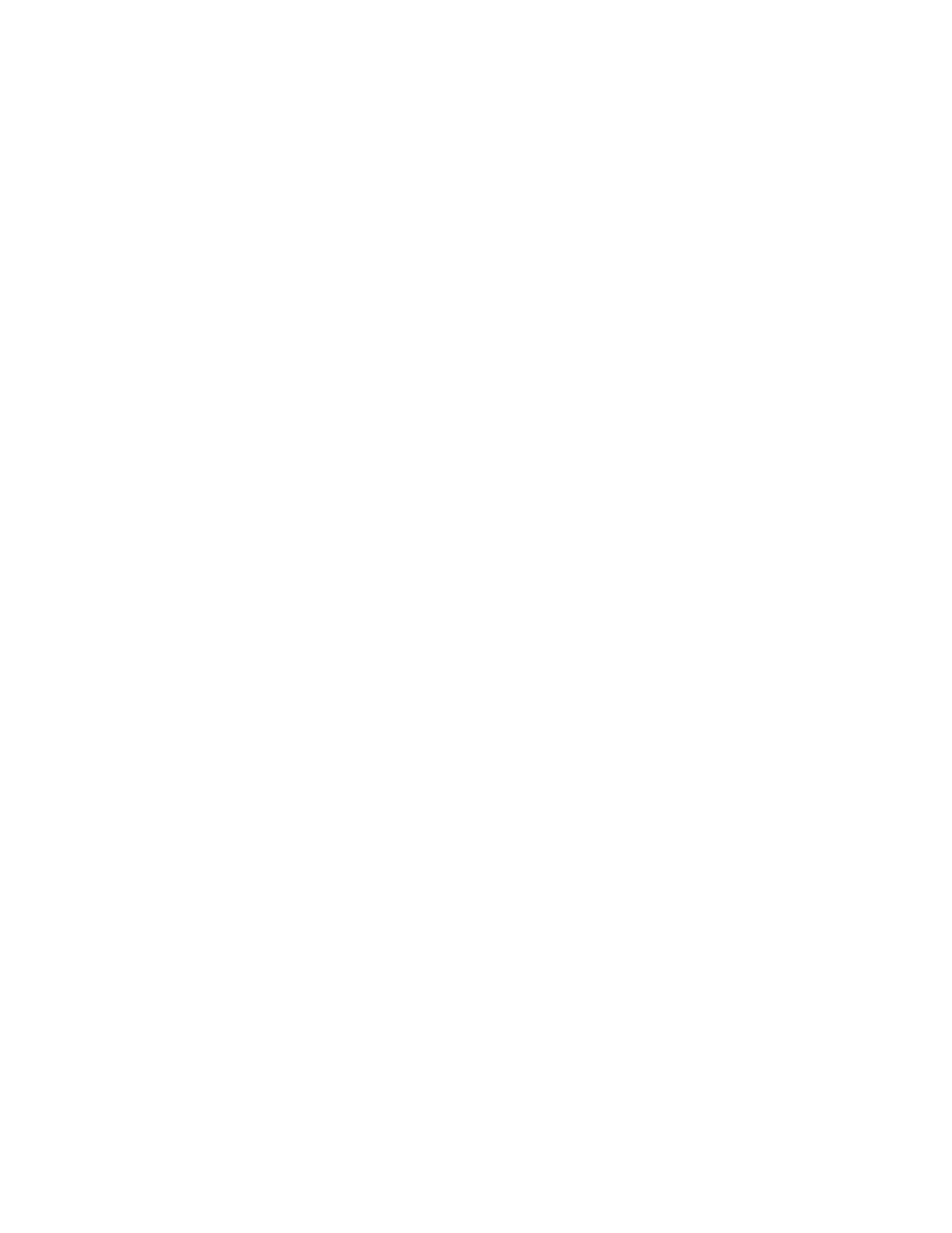
5
4. Insert pin through hole in square drive carrier and into hole in
replacement square drive.
5. Re-attach reaction plate to torque multiplier with the screws
previously removed (Fig. 1, Item 2).
10.0 APPLICATION INFORMATION
10.1 Torque Multiplier Reaction
1. Absorbing torque multiplier reaction forces can be
accomplished using common practices noted here.
2. First consider the size and type of torque tool required for the
application. Survey space limitations as well as the maximum
torque needed. Allow a minimum of 50% additional capacity
in the tool for breakout torque. NOTE: Damaged and corroded
fasteners can require even greater breakout torque capacity.
Allow a minimum of 100% over the make-up torque for these
conditions. Example: Corroded studs and a 1,500 Ft-Lbs.
make-up torque. Choose a tool with a capacity of at least
3,000 Ft-Lbs. for breakout.
3. Select a solid anchor point to minimize defl ection. Determine
where the reaction forces are going to take place (e.g.
against a fl ange or over an adjacent bolt). NOTE: This point
must withstand the torque tool’s reaction forces. Example:
A 3,200 Ft-Lb. torque multiplier, with reaction near the end
of its anchor stub (fi gure 5) produces a reaction force of
6,400 pounds. Reduce the reaction force to 2,400 pounds
by moving the reaction point toward the end of the reaction
plate/bar. Keep the reaction point tangent to the rotation
of the torque output to prevent increased reaction forces
(fi gures 6 and 7).
4. Keep output torque rotation pure by reducing bending
moments. Bending moments decrease torque effi ciency and
increase stress on the tool and sockets. Keep the distance
between the tool’s output and the fastener as short as
possible (fi gure 6).
5. Increase tool life and increase working environment safety
by taking torque reaction as far out on the reaction anchor as
possible (Fig. 5).
10.2 ANGLE OF TURN PROTRACTOR
Some torque multipliers include an Angle of Turn Protractor. This
allows the operator to accurately measure a specifi c number of
degrees of rotation of the fastener. The torque / angle of turn
method of tightening fasteners requires a pre-torque value, and
a specifi c additional rotation of the fastener, that is engineered
into the application. This data will be supplied by the original
equipment manufacturer’s engineering department if angle of
turn torquing is applicable.