Enerpac E-Series User Manual
Page 4
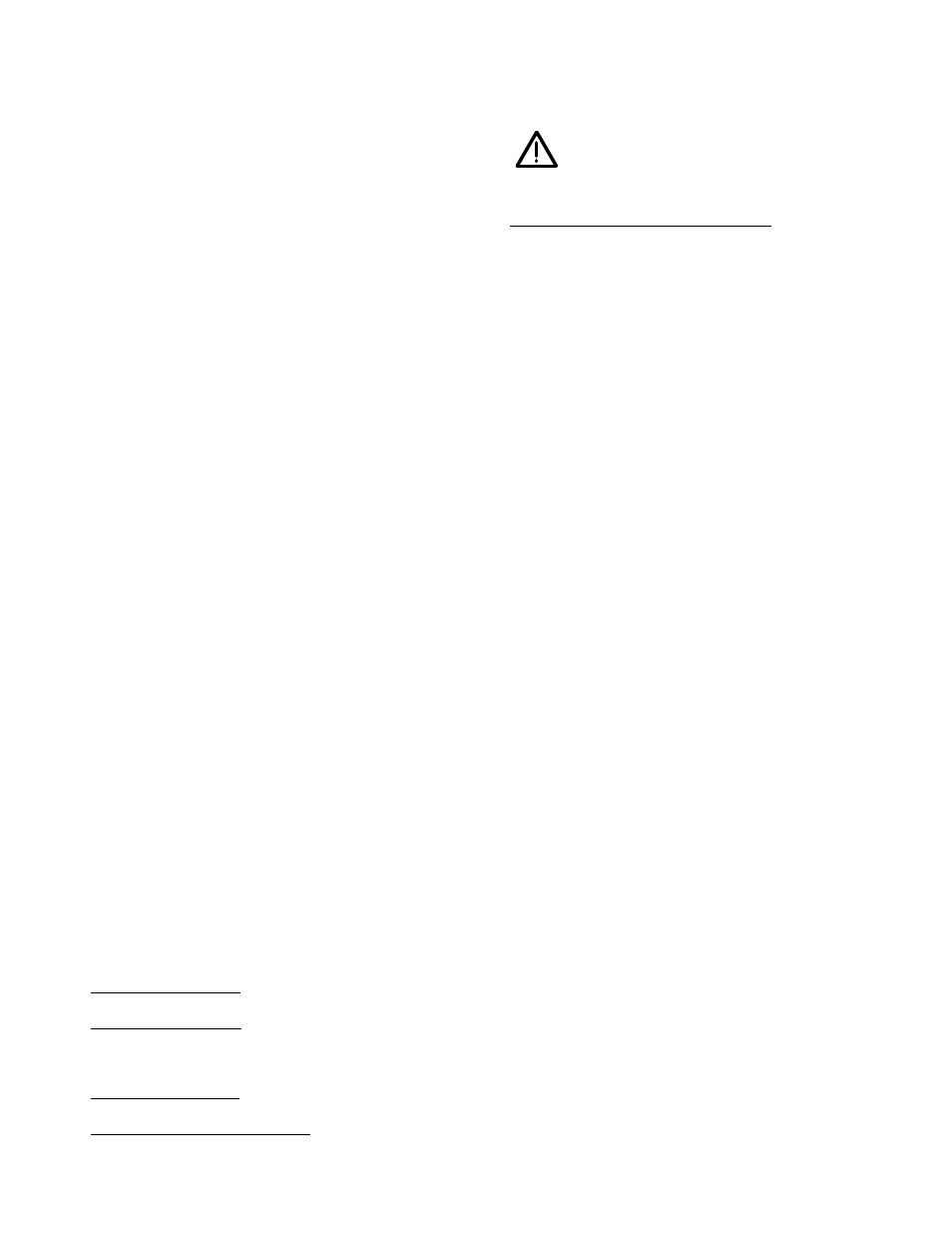
4
5.0 DESCRIPTION AND DESIGN FEATURES
Input and Output rotation directions are the same. (EXAMPLE:
Clockwise input rotation creates clockwise output rotation).
Torque multipliers use planetary gear action to tighten/loosen with
a continuous 360° rotation in either clockwise or counterclockwise
direction. An internal, bi-directional anti-backlash device inhibits
accidental torque wind-up release (not available on E290+, E291,
E391).
NOTE: Reaction force is equal to output force and is in the
opposite direction of input/output rotation force.
Reaction bars are held in place using a detent pin or socket head
cap screw, depending on model. Reaction plates are attached
with socket head cap screws.
A controlled-shear output square drive (Fig. 1 Item 4) protects
internal components in the event maximum output capacity is
exceeded. This overload-protection feature causes the drive
to fracture when output exceeds from 103% to 110% of rated
output capacity. One replacement drive is included with the
torque multiplier (E391, E392, E393, E492, E493, E494, E495).
(Order additional replacements from your Enerpac distributor.)
Selector pawl (Fig. 3, Item 3) must be set in neutral position and
the neutral position set screw (Fig. 3, Item 3) must be tightened to
lock the selector pawl for power drive unit operation. It controls
the torque multiplier’s rotational direction for manually-applied
input. (Not available on E290+, E291, E391 models). Do not use
impact wrench for power driving, damage to multiplier power
train will result.
6.0 TORQUE CONVERSIONS
A data plate attached to the torque multiplier displays input torque
required to obtain listed output torque values. To calculate a
specifi c input value not listed on the data plate, divide the desired
output torque by the multiplier’s torque ratio. See Specifi cation
Tables.
7.0 MANUAL OPERATION
1.
NOTE:
Reaction force is equal to output force and is in the
opposite direction of input/output rotation.
2. Set desired rotation direction by pushing the selector pawl
(Fig. 3, Item 3) in the direction indicated by the letters and
directional arrows stamped on the input end case (Fig. 3,
Item 1). EXAMPLE: “CCW” for counter-clockwise rotation,
push pawl to end of travel in the direction shown by the
“CCW” arrow. For clockwise rotation, push pawl in the
opposite “CW” direction. (Not available on E290+, E291,
E391models).
3. Mount the proper size female square drive socket onto
the torque multiplier’s output square drive (Fig. 1, Item 4).
Position socket and torque multiplier on the fastener to be
tightened.
4. Reaction Plate Models: Place a proper size socket on the
slave square drive and attach it to an adjacent fastener.
Reaction Bar Models: Butt the reaction bar securely
against a suitable object.
NOTE:
When socket is properly
positioned on fastener, reaction bar must be at right angles
to the fastener to which torque is being applied (Fig. 7). See
Application Information section 10.0 for additional torque
multiplier reaction information.
5. Tighten using a torque wrench: Determine the proper
input torque required (refer to torque data plate on tool) or
reference section 4.0 Specifi cation Tables. Output torque
accuracy requires an accurate torque wrench in series with
the torque multiplier. Apply torque with torque wrench until
desired input torque is achieved (Fig. 5).
WARNING: Failure of the output square drive, due
to torque overload or fatigue, could result in an
immediate torque release, potentially causing the
torque multiplier to fall from the fastener, and result in
personal injury.
6. To remove torque multiplier from fastener:
Anti-backlash models: using a torque wrench, apply
enough input torque to release internal anti-backlash device;
maintain torque input and push selector pawl (Fig. 3, Item 3)
into opposite position (EXAMPLE: Pawl set in “CW” position
requires reset to “CCW” position). Slowly relax input torque.
(Not available on E290+, E291, or E391 models).
Standard models: apply torque to desired rating, then slowly
relax input torque and remove multiplier from application
(E290+, E291, or E391 models).
7. Loosen using a torque wrench: Follow same procedure as for
tightening except set the selector pawl in opposite position.
8.0 PNEUMATIC OPERATION
Use an approved non-impact power drive with models: (E391,
E392, E393, E492, E493, E494 or E495 only). Lock selector
pawl in Neutral position by centering between the “CW” and
“CCW” positions and tightening the set-screw (fi g 3, Item 2).
NOTE: Set in the proper position, the selector pawl WILL NOT
move in either direction when the neutral position set screw is
tightened.
9.0 REPLACING A SQUARE DRIVE ASSEMBLY
9.1 Models E290PLUS, E291
1. Remove Retaining ring and circular shims (fi gure 4) from
input side of torque multiplier housing.
2. Remove gear cage assembly from ring gear (torque multiplier
housing).
3. Remove input pinion from gear cage assembly with a pulling
and twisting motion. Use an arbor press to remove dowel
pins from planet gears (fi gure 4).
4.
Replace gear cage assembly with genuine Enerpac
replacement.
5. Reassemble planet gears into cage assembly using arbor
press.
6. Lubricate all friction points with high-grade molybdimum-
disulfi de grease.
7. Reassemble input pinion, install assembly into ring gear
(torque multiplier housing). Reassemble shims and retaining
ring.
9.2 Models E391, E392, E393, E492, E493, E494, E495
1. Remove the screws (Fig. 1, Item 2) holding the reaction plate
(Figure 1, Item 1) to the torque multiplier, and remove the
reaction plate from the torque multiplier.
2. Remove the pin engaging the gear cage with the output
square drive and remove old output square drive.
3. Insert replacement square drive assembly into square
drive carrier, aligning the hole in the lower portion of the
replacement square drive with the hole in the square drive
carrier.