Det-Tronics EQP Fire and Gas Detection/Releasing System SAFETY MANUAL User Manual
Page 7
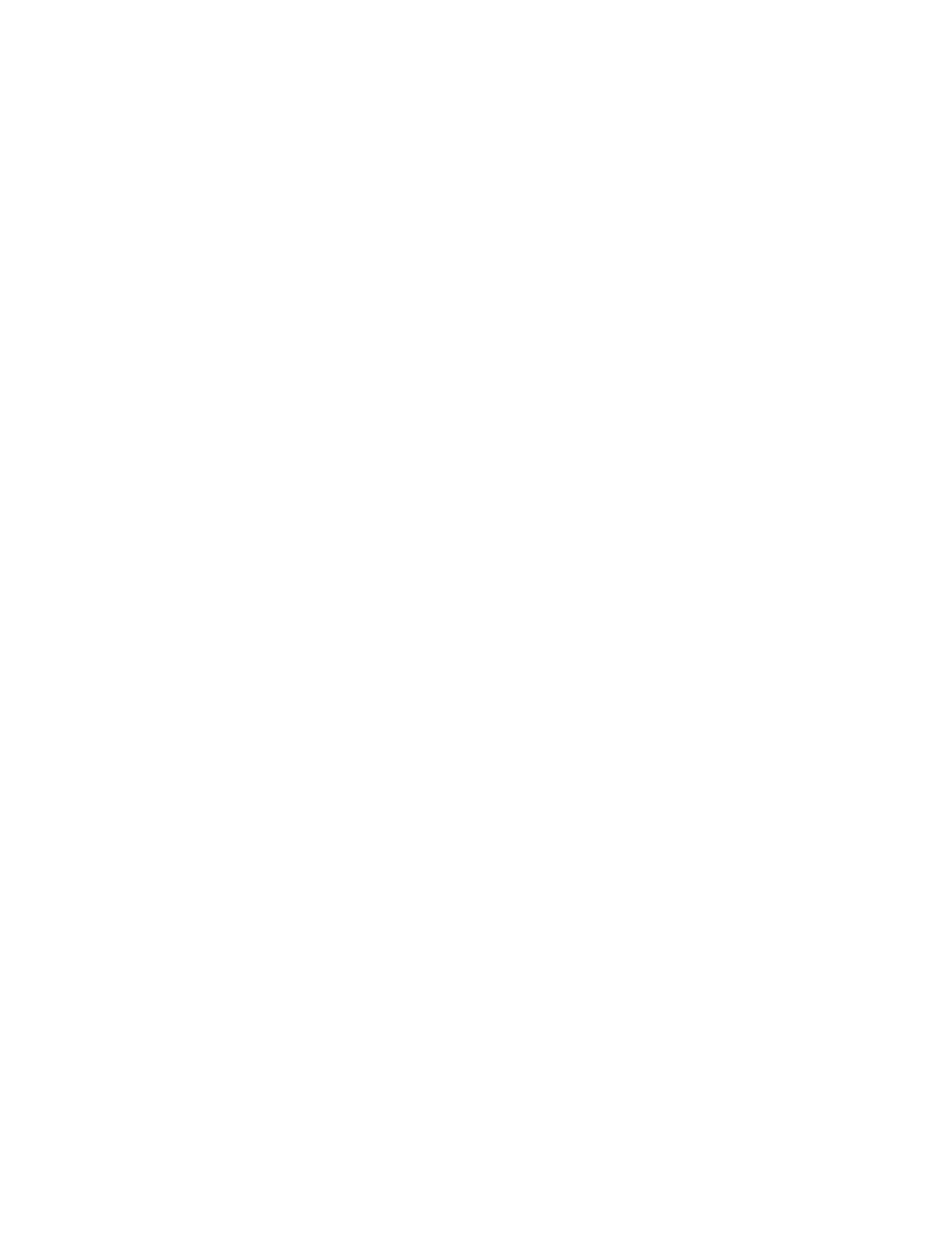
5.1
95-8599
5
EQP SAfETY CONTROLLERS
The EQP Safety Controllers share a common hardware
and software platform with standard EQP Controllers.
The SIL rated version of the Controller conducts
additional diagnostic checks and annunciates additional
fault conditions.
Safety compliance is assured by additional diagnostics,
which detect failures and take appropriate action should
errors be detected.
If the EQP Safety Controller detects a “dangerous”
fault in itself (i.e. one that would prevent the EQP
Safety System from carrying out its safety function) it
will de-energize the trouble relay. The fault causing
the Controller’s trouble relay to de-energize must be
investigated and corrected within the time period
determined by SIF verification calculations for the
particular application.
Run Mode
Run Mode is the state in which the Det-Tronics EQP
Safety System is acting as a safety-related system and
carrying out its safety function. When the system is in
this state, it is not possible to make modifications to
configuration parameters or control logic.
Program Mode
The system enters Program Mode when configuration
parameters are downloaded to the system. The
Controller trouble relay is de-energized while in this
mode as an indication. When the EQP System is in
Program Mode, the user is responsible for maintaining a
safe state.
Note
When there is a change of configuration, the user is
required to perform a validation test of the change.
Safe and Non-interfering Data
An EQP application program can read data from
safety-related and non-interfering sources. Data from
non-interfering sources must not be used in logic to
block or disable safety-related signals in the safety
loop. For example, data coming into the system from
a non-interfering field device should not be used to
block or disable an alarm output, but It could be used to
activate a common alarm used by safety-related logic.
Communication with Remote Modbus Devices
EQP Safety Controllers can read or write data to Remote
Modbus devices. Any data read from such devices
is not safety-related and shall not be used to block or
disable safety-related logic.
EQP Controller Inhibit Lockout
Device inhibits allow input and output signals to be
blocked to allow the user to perform maintenance and
testing without affecting system outputs. Example: If a
flame detector is inhibited, a flame can be presented to
the detector and the fire alarm will not be registered by
the controller. Subsequently, no action will be performed
by the controller. Therefore inhibits are classified as a
safety related issue. If a device is inhibited, it will no
longer perform its safety function. For this reason, there
is a global inhibit lockout feature.
Input channel four of the safety controller is designated
as the inhibit lockout channel. The channel must be
configured as “Inhibit Enabled” via the EQP controller
configuration screen in the S
3
software. A normally open
switch must be wired to channel four to perform the
inhibit enable function. When the switch is open, inhibits
are not allowed. When the switch is closed, inhibits can
be activated from the controller via user configured logic
or from the individual device point displays on the S
3
software.
When the inhibit lockout switch changes state, it is
logged in the EQP controller. Additionally, individual
devices are logged when they are put into the inhibit
state.
It is the user’s responsibility to create and enforce an
appropriate lockout policy for the site.