Det-Tronics EQP Fire and Gas Detection/Releasing System SAFETY MANUAL User Manual
Page 14
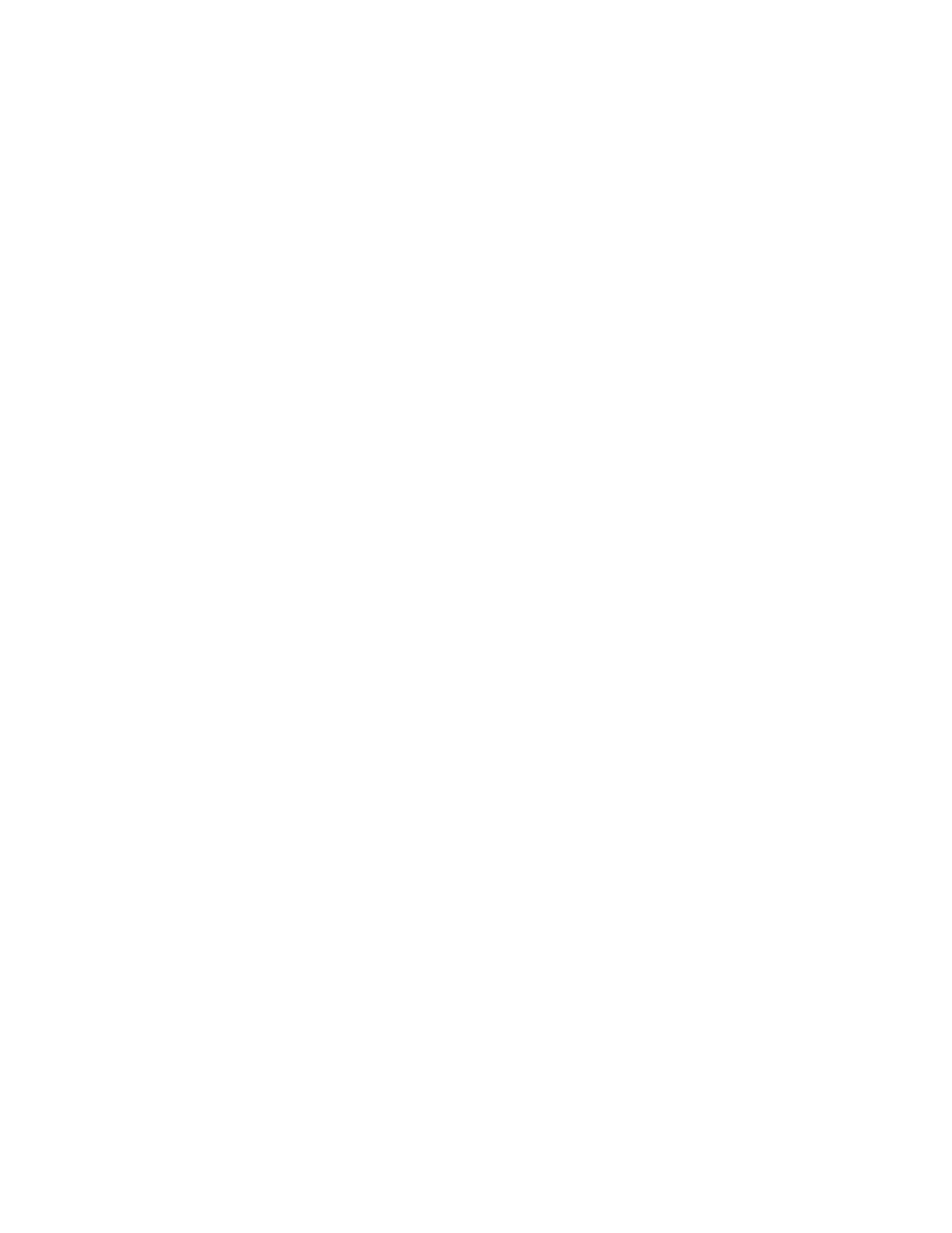
5.1
95-8599
12
gENERAL APPLICATION REQUIREMENTS
System Application Restrictions
The following application level restrictions have been
assumed:
• The EQP system is only used for safety applications
that are low demand according to IEC 61508
definitions.
• Only Det-Tronics EQP system devices may be
connected to EQPSL network (closed network).
• Physical EQPSL network topology is limited to a single
loop.
• Indication of degraded conditions through opening of
the EQP controller’s fault relay must be investigated
and the conditions corrected within time period
determined by SIF verification calculations for the
particular application.
• Periodic proof testing of trip signals through
EQPSL network at least once per 5 years (1 year
recommended).
• Periodic proof test of input sensors at least once per 3
years (1 year recommended).
• Product life limited to 20 years.
• The EQP System is operated within the environmental
conditions described in the Specifications section of
EQP Instruction Manual (number 95-8533).
Application Standards
The EQP Safety System is certified to meet the
requirements of a number of application standards
that are listed in this Safety Manual and on the exida
®
certificate. Users must ensure that they comply with
all the requirements of the standard, not just those that
apply to the EQP Safety System.
Operator Interface
The EQP Safety System may be connected to an
operator interface, matrix panels, mimic panels and
switches.
These interfaces allow the operator to monitor the
operation of the system and diagnose system faults.
The EQP Safety System will allow detected faults (from
line supervision monitoring, internal diagnostics etc.) to
be displayed or indicated.
S3 Safety System Software
Programming, downloading safety-related parameters
and programs and switching between operating states
is carried out via an engineering workstation using S
3
Software.
Access to the Programming Interface shall only be
permitted for authorized and suitably qualified
personnel. Access must be restricted by the use of
passwords (and the options to do this are provided
for within S
3
Software) and/or some other forms of
restricting access.
The Programming Interface may be used as the
Operator Interface, but use of the Programming Interface
must be restricted to authorized and qualified personnel.
Instructions for using S
3
and typical application
examples are provided in the S
3
Instruction Manual
(number 95-8560).
hardware fault Tolerance, Safe failure fraction and
Sub-System Type
The EQP Safety System is a Type B system, with a
hardware fault tolerance of 0 and a safe failure fraction
of >90%. It is, therefore, suitable for use in safety
functions requiring a safety integrity level of 2.
Calculating PfD for Low Demand Applications
This Section gives a basic introduction to calculating the
average probability of failure on demand (PFDavg) for a
safety function incorporating the EQP Safety System.
For the purpose of this example, the following
assumptions have been made:
• All components are certified as suitable for use in SIL
2 safety-related applications.
• All elements are used in 1oo1 arrangements.
• Any Mean Time To Restore (MTTR) less than 48 hours
is negligible.
• The approximation PFDavg = 1/2 T1
l
DU
is valid for
the proof test interval considered.
PFDavg for a particular safety function is the sum of the
probabilities of the average failure on demand of each
element of the system, taking into account the proof test
interval of each element.