Tuning level, R&s programs level, Alarms level – NOVUS Controller N120 User Manual
Page 6: Atvn, Kyt1, Bias, O1ll, O1kl, Kyt2, Olap
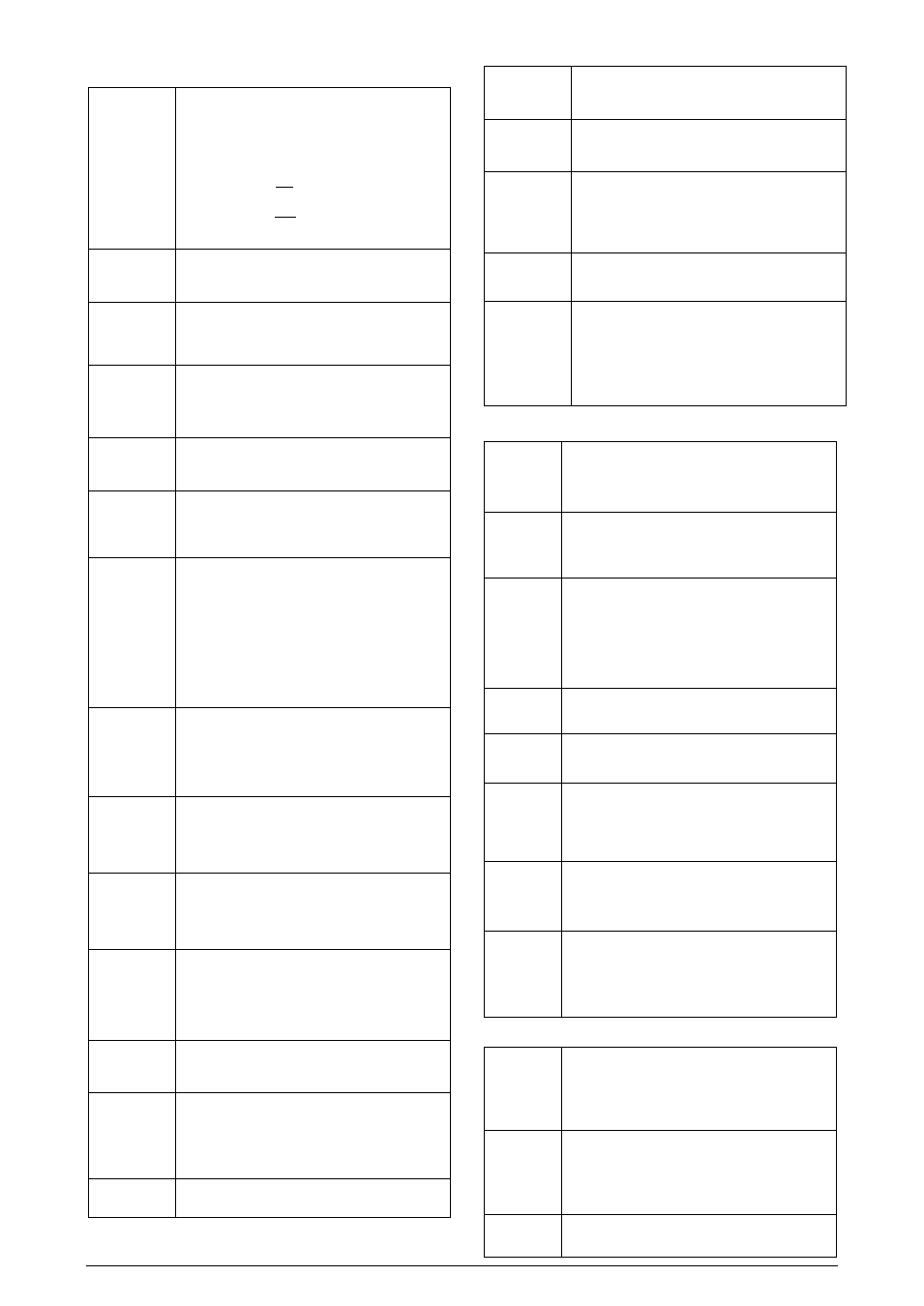
NOVUS AUTOMATION
6/14
TUNING LEVEL
Atvn
Auto-tune. Defines the control strategy to be taken -
Off
– Turned off. (no PID tuning)
Fast
– automatic tuning.
Full
– More accurate automatic tuning.
self
– Precise + auto - adaptative tuning
rslf
– Forces one new precise automatic precise
+ auto - adaptative tuning.
tght
– Forces one new precise automatic + auto -
adaptative tuning when Run = YES or
controller is turned on.
Pb1
Proportional Band. Value of the term P of the control 1
mode PID, in percentage of the maximum span of the
input type. Select zero for ON/OFF control.
ir
Integral Rate. Value of the term I of the PID algorithm, in
repetitions per minute (Reset).
Displayed only if proportional band ≠ 0.
dt
Derivative Time. Value of the term D of the control mode
PID, in seconds. Adjustable between 0 and 300.0
seconds.
Displayed only if proportional band ≠ 0.
(t1
Cycle Time. Pulse Width Modulation (PWM) period in
seconds to Control 1. Displayed only if proportional band
≠ 0.
Kyt1
Control 1 Hysteresis (in engineering. units): This
parameter is only shown for ON / OFF control (Pb1=0).
Adjustable between 0 and the measurement input type
span.
ACt
Control Action. For Auto Mode only.
re
Control with reverse Action. Appropriate for
heating. Turns control output on when PV is
below SP.
dir
Control with direct Action. Appropriate for
cooling. Turns control output on when PV is
above SP.
For the control output 2, the control action is always
opposite to the one defined for control output 1.
bias
Fuction Bias. Offset for MV (manual reset). Range: -100
% to +100 %.
Allows adding a percentage value between -100 % and
+100 %. to the MV control output
The value 0 (zero) disables the function.
O1ll
Output Low Limit. Lower limit for the control 1 output -
Minimum percentage value assumed by the control
output when in automatic mode and in PID.
Typically configured with 0 %. Default value: 0 %
O1kl
Output High Limit. Upper limit for the control 1 output -
Maximum percentage for the control output when in
automatic mode and in PID.
Typically configured with 100 %. Default value: 100 %
Pb2
Proportional Band 2. Value of the P term for control
output 2, in percentage of the maximum span of the input
type.
Select zero, and the hysteresis control is set in the
OLAP
screen.
Kyt2
Control 2 Hysteresis. This parameter is only shown for
ON / OFF control (Pb2=0).Adjustable between 0 and the
measurement input type span.
Olap
Overlap. Defines the overlap between the heat and cool
outputs. The overlap is given in engineering units of the
input type used.
When the overlap value is negative, it represents the
value of the dead-band instead.
[t2
Cycle Time. PWM period in seconds. Can only be viewed
if proportional band is other than zero.
O2ll
Output Low Limit: minimum. Percentage value for MV
(Manipulated Variable) when in automatic control and
PID. Default value: 0.0 %
O2kl
Output High Limit: Maximum. Percentage value for MV
when in automatic control and PID. Default value: 100.0
%
sfst
SoftStart Function. Time in seconds during which the
controller limits the MV value progressively from 0 to 100
%. It is enabled at power up or when the control output is
activated. If in doubt set zero (zero value disables the
Soft start function).
Lbd.t
Loop break detection time.Time interval for the LBD
function. Defines the maximum interval of time for the PV
to react to a control command. In minutes.
Sp.a1
Sp.a2
Sp.a3
Sp.a4
Alarm Setpoint. Tripping points for alarms 1 and 2. Value
that defines the point of activation for the programmed
alarms with the functions “Lo” or “ki”.
For the alarms configured with Differential type
functions, this parameter defines deviation (band).
Not used for the other alarm functions.
R&S PROGRAMS LEVEL
Pr.tb
Program time base. Defines the time base that will be
used by all Ramp & Soak programs.
Se( - Time basis in seconds;
Min - Time basis in minutes;
Pr n
Program number. Selects the ramp and soak profile
program to be edited/viewed. The sequence of
parameters that follows refer to this selected program.
Total of 20 programs possible.
Ptol
Program Tolerance. Maximum admitted deviation of PV
with respect to SP. If exceeded, the program execution is
suspended (the internal timer freezes) until the deviation be
returns back within the defined tolerance.
The value 0 (zero) disables the function (the program
progresses regardless of the difference between PV and
SP).
Psp0
Psp9
Program SP’s, 0 to 9: Group of 10 values of SP that define
the Ramp and Soak profile segments.
Pt1
Pt9
Segments durations, 1 to 9: Defines the time of duration,
in second or minutes, of the segments of the program
being edited.
Pe1
Pe9
Program event. Alarms of Event, 1 to 9: Parameters that
define which alarms are to be activated during the
execution of a certain program segment. The alarms
chosen must have its function configured as “rS.” (See
Table 3)
Psp1
Psp9
Program SP. Ramp and Soak Set Points: (0 to 9): Set of
10 SV values which define the ramp and soak profile
segments.
Lp
Link Programs. Number of the next profile program to be
linked following the current program. Profiles can be linked
together to produce larger programs of up to 180
segments.
0 – do not link to any other program.
ALARMS LEVEL
Fva1
Fva2
fva3
fva4
Functions of Alarms. Defines the functions for the alarms
among the options of the Table 3.
oFF, iErr, rs, Lo, xi, DiFL, DiFx, DiF
bla1
bla2
bla3
bla4
Blocking Alarm. This function blocks the alarm at power-
up when the units is first energized.
YES - Enables.
NO - Inhibits this blocking function.
xya1
xya2
Histeresis of Alarm. Defines the difference between the
value of PV at which the alarm is triggered and the value