Lbd - loop break detection alarm, Safe output value with sensor failure, Usb interface – NOVUS Controller N120 User Manual
Page 4: Instalation
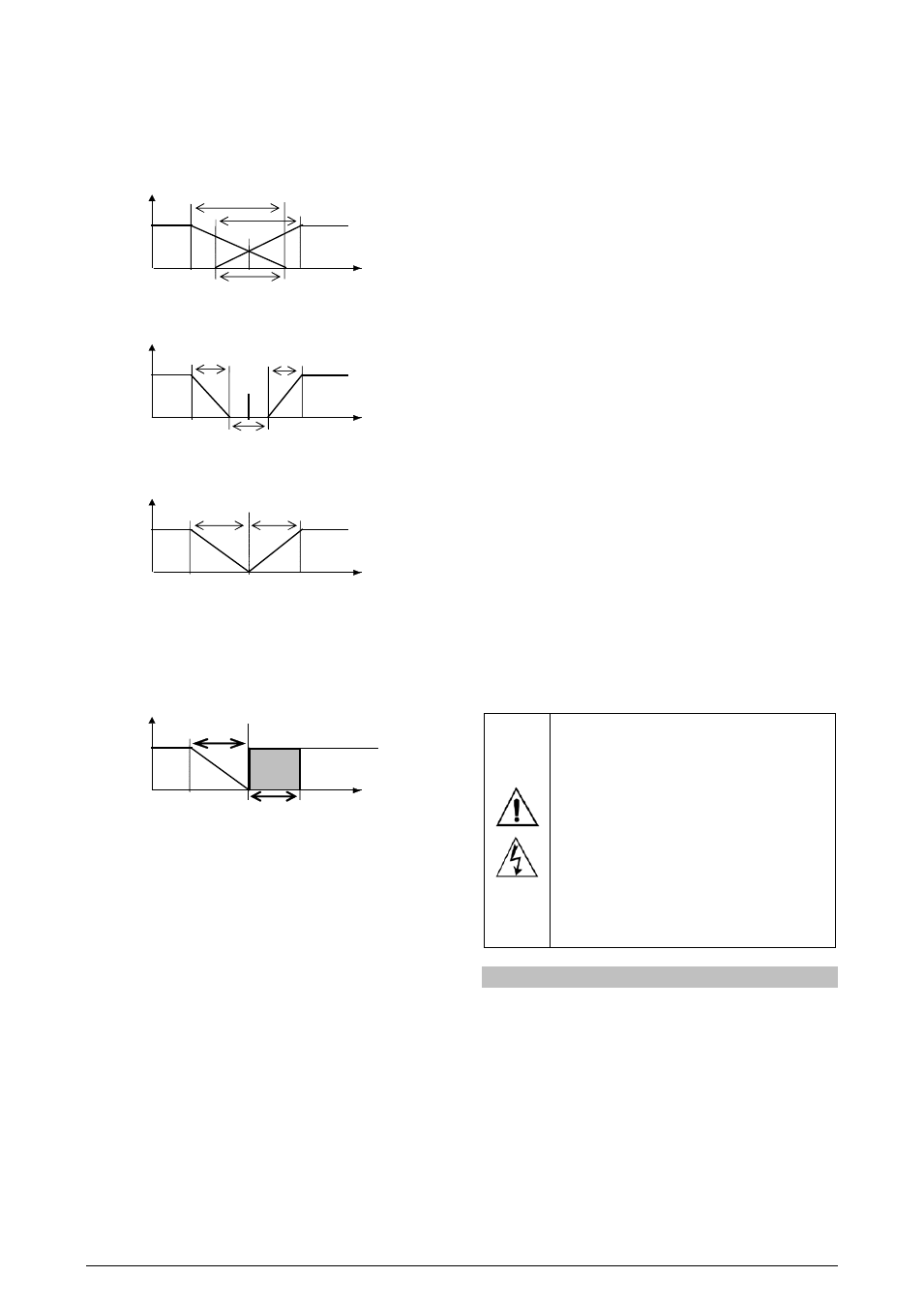
NOVUS AUTOMATION
4/14
When the application requires both heating and cooling at the same
time, you must set the parameters ACt=re and adjust the overlap
(OLAP) to determine the type of operation.
There are three situations:
OLAP
> 0; when there are overlapping between heating and cooling
actions.
Control output
Process variable
Overlap
Pb1
Pb2
Output 1
Output 2
Set Point
OLAP
< 0; for setting a dead-band.
Control Output
Process Variable
Dead band
Pb1
Pb2
Output 1
Output 2
SetPoint
OLAP
= 0; no superposition or dead-band for the outputs.
Control Output
Process Variable
Pb1
Pb2
Output 1
Output 2
Set Point
Output 2 has independent proportional band and PWM period, as
well as maximum and minimum limits for the output.
If Pb2=0, the control #2 becomes ON-OFF.
Both outputs can be on at the same time even with negative OLAP if
Control Output 1 is using PID control.
Control Output
Process Variable
Pb1
HIST2
Output 1
Output 2
OFF
ON
Set Point
LBD - LOOP BREAK DETECTION ALARM
The parameter defines a time interval, in minutes, within which the
PV is expect to react to a control output signal. If the PV does not
react properly within the time interval configured in lbd.t, the
controller interprets this as a control loop break and signals this
occurrence in the display.
A LBD event may be sent to any I/O channel. Simply configure the
LDB function to the desired I/O channel: the selected output will be
activated when a LDB condition is detected. When the lbd.t
parameter is programmed with 0 (zero), the LDB function is disabled.
The LDB is useful in system supervision and troubleshooting, allowing
early detection of problems in the actuator, power source or load.
SAFE OUTPUT VALUE WITH SENSOR FAILURE
(Output 1 only)
This function defines an output value (user defined) to be assigned to
the control output in the event of a sensor failure.
When the input sensor is identified as broken, the controller switches
the control mode to MANUAL while forcing MV to assume the user
configured value in the 1E.ov parameter.
This function requires that one of the alarms be configured as 1Err
and the 1E.ov parameter (control output percentage) programmed
with a value other then 0 (zero).
Once this function is triggered, the controller remains in SAFE mode
(MANUAL control output) even after the sensor failure appears to be
fixed. The operator intervention is required for switching back to
AUTO mode.
USB INTERFACE
The USB interface is used for CONFIGURING or MONITORING the
controller. The NConfig software must be used for the configuration.
It makes it possible to create, view, save and open configurations
from the equipment or files in your computer. The tool for saving and
opening configurations in files makes it possible to transfer
configurations between pieces of equipment and to make backup
copies. For specific models, the NConfig software also makes it
possible to update the firmware (internal software) of the controller
through the USB.
For MONITORING purposes you can use any supervisory software
(SCADA) or laboratory software that supports the MODBUS RTU
communication on a serial communications port. When connected to
the USB of a computer, the controller is recognized as a conventional
serial port (COM x). Use the NConfig software or consult the
DEVICE MANAGER in the Windows CONTROL PANEL to identify
the COM port that was assigned to the controller. Consult the
mapping of the MODBUS memory in the controller’s communications
manual and the documentation of your supervisory software to
conduct the MONITORING process.
Follow the procedure below to use the USB communication of the
equipment:
• Download the NConfig software from our website and install it on
your computer. The USB drivers necessary for operating the
communication will be installed together with the software.
• Connect the USB cable between the equipment and the
computer. The controller does not have to be connected to a
power supply. The USB will provide enough power to operate the
communication (other equipment functions cannot operate).
• Open the NConfig software, configure the communication and
start recognition of the device.
• Consult the NConfig help desk for detailed instructions about how
to use it and solve problems.
The USB interface IS NOT SEPARATE from the
signal input (PV) or the controller’s/indicator’s digital
inputs and outputs. It is intended for temporary use
during CONFIGURATION and MONITORING
periods. For the safety of people and equipment, it
must only be used when the piece of equipment is
completely disconnected from the input/output
signals. Using the USB in any other type of
connection is possible but requires a careful analysis
by the person responsible for installing it. When
MONITORING for long periods of time and with
connected inputs and outputs, we recommend using
the RS485 interface, which is available or optional in
most of our products.
INSTALATION
The controller was designed to be fixed by screws, behind a face of
metal panels of equipment or machinery. Display and keyboard
should fit in appropriate cut of this panel. The following figures show
the dimensions and distances required for attachment.