NOVUS N323RHT User Manual
N323rht
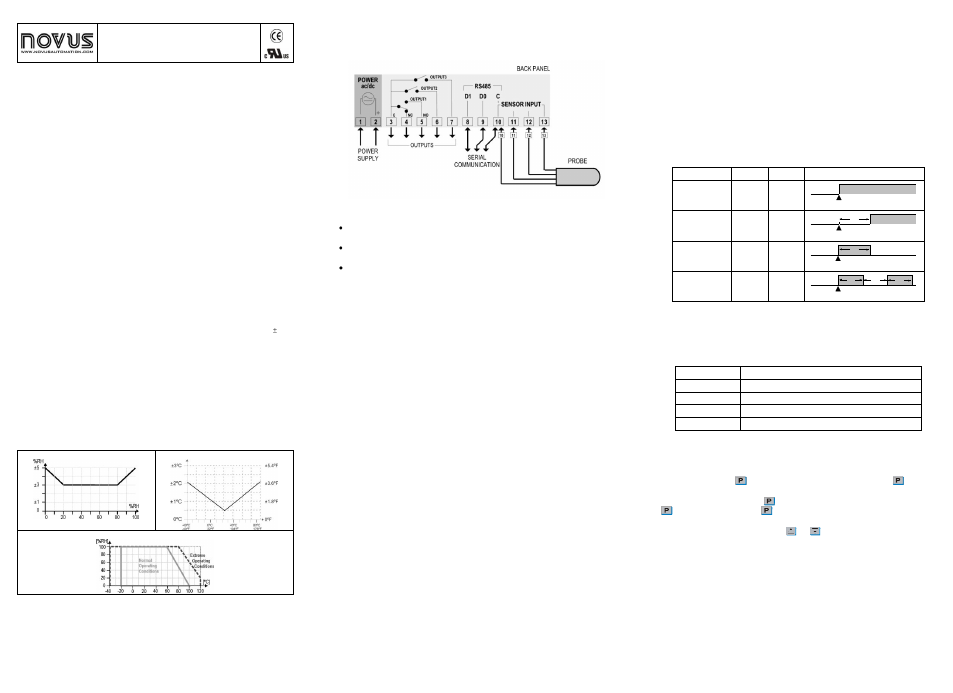
TEMPERATURE AND HUMIDITY CONTROLLER
N323RHT
OPERATING MANUAL - V1.8x B
Man 5001276
The 323RHT is a digital controller for relative humidity and temperature with three relay outputs
configurable independently for control or alarm. Timer functions are available to all three outputs.
A Relative Humidity and Temperature 3-meter probe is bundled with the instrument. The sensor is
protected by a polyamide capsule.
The features of a particular model (input sensor type, sensor range, mains supply, etc) are identified by
the label placed on the controller body.
SPECIFICATIONS
INPUT SENSOR: Humidity measurement
Range: 0 and 100 % (RH) (see Fig. 1);
Accuracy: See Fig. 1; Repeatability: ± 1 % RH;
Hysteresis: ± 1 % RH;
Linearity error: << 1 % RH;
Stability: < 1 % RH / year;
Response time:
4 seconds in the range from 10 to 90 %, with slow moving air. Outside
this range, up to 48 hours.
INPUT SENSOR: Temperature
Accuracy: Refer Fig. 1; Repeatability: ±0.1 °C;
Range: -40 and 120 °C (see Fig. 1);
Response time: up 30 seconds in slow moving air;
WARM-UP: ................................................................................................................................... 15 minutes
MEASUREMENT RESOLUTION:
RH: ..................................................................................... 1 %
T: ...................................................... 0.1º from –19.9 to 119.9º
OUTPUT1: ........................................................... Relay SPDT; 1 HP 250 Vac / 1/3 HP 125 Vac (16 A Res.)
.................................................................................. Optional: Pulse, 5 Vdc, 25 mA max.
OUTPUT2: ...................................................................................................... Relay: 3 A / 250 Vac, SPST-NA
OUTPUT3: ...................................................................................................... Relay: 3 A / 250 Vac, SPST-NA
POWER SUPPLY:
Tension: ........................................... 100 to 240 Vac/dc 10 %
Optional: ............................................................... 12 to 30 Vdc
Frequency:................................................................. 50~60 Hz
Consumption: .................................................................... 5 VA
Dimensions:
Width x Height x Depth: ........................................................... 75 x 33 x 75 mm.
Weight: ........................................................................................................ 100 g
Panel cut-out: .................................................................................... 70 x 29 mm
Instrument operating environment: ................................................................... 0 to 40 °C / 20 to 85 % RH
Probe operating environment: .................................................................... -10 to 100 °C / 0 to 100 % RH
Case: Polycarbonate UL94 V-2, Protection: Box IP42; Front panel: IP65
Suitable wiring: Up to 4.0 mm²; RS-485 digital communication; RTU MODBUS protocol (Optional)
Serial interface not isolated from input circuitry.
Input circuitry isolated from power supply, except in the 24 V powered model.
Relative Humidity Accuracy @ 25 °C
Temperature Accuracy
Sensor Operating Conditions
Fig. 1 – RH and temperatures accuracies
IMPORTANT
The sensor used in this controller may be damaged or lose calibration if it is exposed to aggressive
atmospheres with high concentrations as Chloride Acid, Nitride Acid, Sulphuric Acid or Ammonia.
Acetone, Ethanol and Propylene Glycol may cause reversible measurement drifts.
Fine trimming in the indication of RH and Temperature are available at the parameters 0fk e 0ft, in the
configuration level of parameters.
ELECTRICAL WIRING
The figure below indicates the connection to the sensor, power supply and controller output, as well as a
connection example.
Fig. 2 – N323RHT terminals – Relays share a common terminal (standard model)
It is important to follow the recommendations below:
The humidity sensor Conductors shall go through the system plant separately from the control and
feeding output conductors, if possible in grounded electrical ducts.
The controller feeding shall be preferably provided from a proper instrumentation network with a
phase different from the one used for the control output.
It is recommendable to use RC FILTERS (47 R and 100 nF, series) in contactor coils, solenoids, etc.
WORKING WITH THE CONTROLLER
The controller operates on the outputs OUTPUT1, OUTPUT2 and OUTPUT3 to lead the measured
variable (temperature or humidity) to the intended value, defined by the setpoint (SP1, SP2 and SP3).
OUTPUT1, OUTPUT2 and OUTPUT3 can operate either as control outputs, when they operate directly on
the system load (resistance, compressor, humidifier, etc.) or as alarm outputs that operate notifying the
operator about the occurrence of any specific situation, defined by the user. The operation modes are
presented below and they can be defined on parameters a(1, a(2 and A(3.
0
- Reverse control action.
Activates the corresponding OUTPUT when the process variable (RH or temperature) is below the
setpoint of that output. Normally used for heating control.
1
- Direct control action.
Activates the output whenever the process variable is above the setpoint for that output. The direct
action is used for refrigeration control.
2
- Low Alarm.
Minimum value alarm, indicates that the process value is below the alarm setpoint defined for the
output.
3
- High Alarm.
Maximum value alarm, indicates that the process is above the alarm setpoint defined for that output.
4
- Low alarm with initial blocking.
Identical to the Low Alarm, with the addition of the initial blocking feature explained in Note 2 below.
5
- High alarm with initial blocking.
Identical to the High Alarm, with the addition of the initial blocking feature explained in Note 2 below.
6
- Inside Range Alarm.
Activates the output when the process variable is within the interval defined by:
(SP1 – SP2) and (SP1 + SP2) or (SP1 – SP3) and (SP1 + SP3)
7
- Outside Range Alarm.
Activates the output when the process variable is outside the interval defined by:
(SP1 – SP2) and (SP1 + SP2) or (SP1 – SP3) and (SP1 + SP3)
8
- Inside the range alarm with initial blocking.
Identical to the inside the range alarm with the addition of the initial blocking feature, describe in
Note 2 below.
9
- Outside the Range Alarm With Initial Blocking.
Identical to the outside the range alarm with the addition of the initial blocking feature, describe in
Note 2 below.
Note 1: The action modes 6, 7, 8 and 9 are available to OUTPUT 2 and OUTPUT 3 only. For OUTPUT 2
when (NT = 0, 1, 6 or 7. For OUTPUT 3 when (NT = 0, 2, 5 or 7.
Note 2: The Initial Blocking feature inhibits the alarm from being recognized if an alarm condition is
present when the controller is first energized. The alarm will be enabled only after the occurrence of a
non-alarm condition followed by a new occurrence for the alarm.
The Initial Blocking impedes (blocks) the alarm from being switched on in the beginning of the
control process. The alarm will only be unblocked after the passage of the variable measured by a non-
alarm condition. This feature is useful when, for example, a minimum alarm is programmed in a heating
process. Without the blocking, the process would start with an enabled alarm until the control setpoint is
achieved.
Output Timing
The controller allows for the Output Timing programming, where the user can establish three conditions:
output tripping delay, temporary activation and sequential activation.
The timing is available only for outputs 1, 2 and 3 and is programmed by means of the “1t1”, “2t1”,
“3t1”, “1t2” “2t2” and “3t2”.
The figures below represent these functions; T1 and T2 can vary from 0 to 1999 seconds and their
combinations determine the timing mode. For normal operation of the alarms, without timing, program 0
(zero).
On the front panel, the controllers P1, P2 and P3 light when the respective outputs are activated. During
the delay, the respective signaler remains flashing.
TIMER FUNCTION
T1
T2
ACTION
Normal operation
0
0
Delayed activation
0
1 to 1999 s
Temporary activation 1 to 1999 s
0
Sequential activation 1 to 1999 s 1 to 1999 s
Table 1 – Timer alarm functions 1, 2 and 3
OPERATION
The controller shall be set up by the user before using. This consideration consists in the definition of the
values for the various parameters that determine the equipment operation mode.
These set up parameters are organized in groups or Levels, called parameter levels.
Level
Function
0
Measurement
1
Setpoints Adjustment
2
Configuration
3
Calibration
Upon power-up controller, the controller display shows for 1 second its firmware version. This information
is useful when consulting the factory.
Then, the temperature measured by the sensor is shown on the display. This is the parameter level 0 or
Temperature Measurement level.
For access to level 1 press
for 1 second till the “SP1” parameter appears. Press
again to go
back to the temperature measurement level.
To access level 2 of parameters, press
for 2 seconds until the “rkT” message is shown. Release the
key to remain in this level. Press
again to access other parameters from this level. After the last
parameter, the controller goes back to the temperature measurement level.
To change the parameters values, use the keys
and
until the achievement of the desired values.
Notes:
1
The programming is saved by the controller when the latter goes from one parameter
to the other and only then it is considered valid. The programming is stored in a
permanent memory, even if there is a power supply interruption.
2
If no keyboard activity is detected for over 20 seconds, the controller saves the current
parameter value and returns to the measurement level.
Alarm Event
Alarm
Output
Alarm Event
Alarm
Output
T2
Alarm Event
Alarm
Output
T1
Alarm Event
Alarm
Output
T1
T2
T1