NOVUS N480D User Manual
Controller n480d
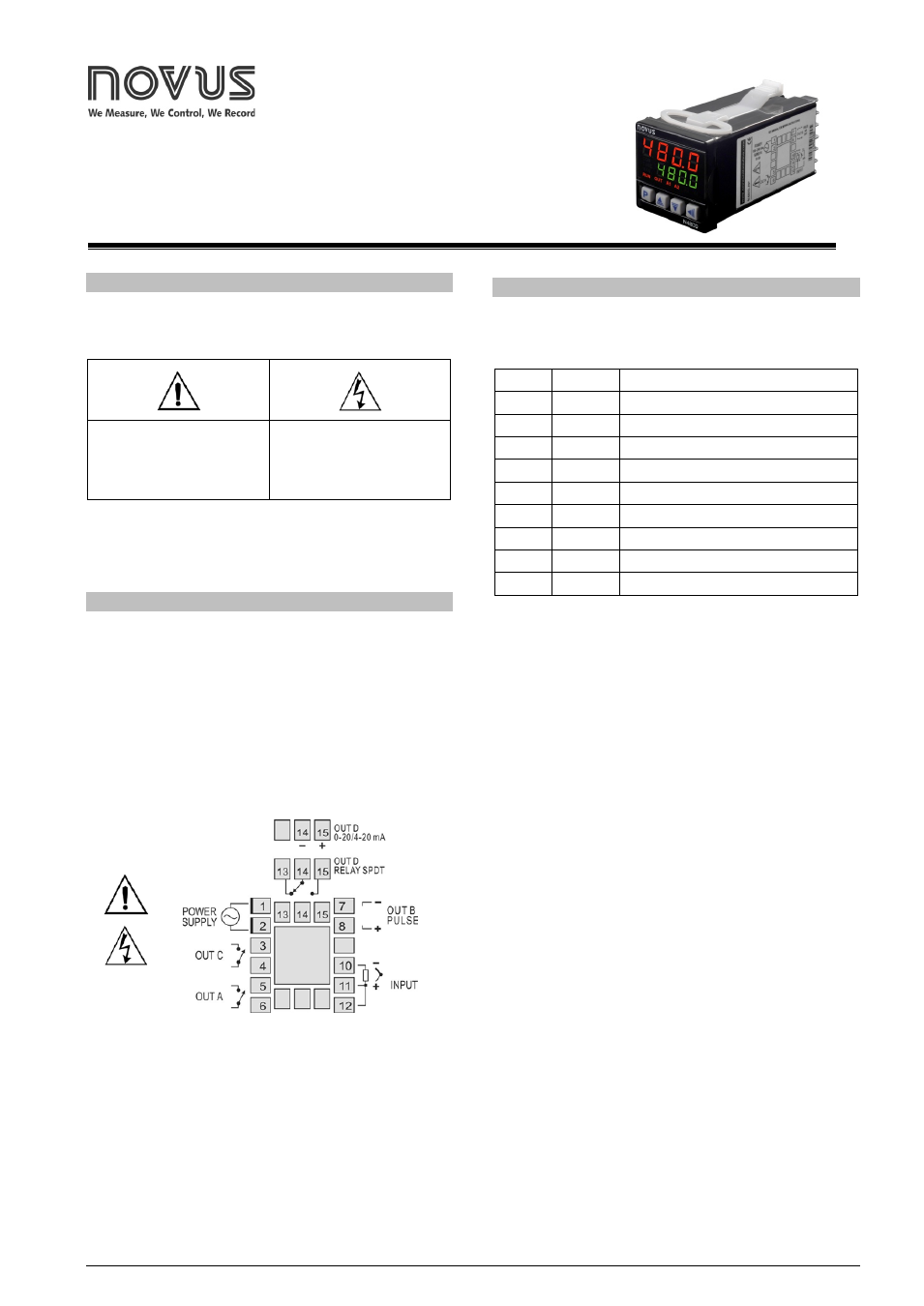
NOVUS AUTOMATION
1/6
Controller N480D
UNIVERSAL CONTROLLER – INSTRUCTIONS MANUAL – V5.0x
SAFETY SUMMARY
The symbols below are used on the equipment and throughout this
document to draw the user’s attention to important operational and
safety information.
CAUTION:
Read complete instructions prior
to installation and operation of
the unit.
CAUTION or WARNING:
Electrical Shock Hazard
All safety related instructions that appear in the manual must be observed
to ensure personal safety and to prevent damage to either the instrument
or the system. If the instrument is used in a manner not specified by the
manufacturer, the protection provided by the equipment may be impaired.
INSTALLATION
The controller must be installed on a panel with a square opening with
the specified dimensions. In order to fasten to the panel, remove the
clamps from the controller, introduce the controller in the panel’s
opening through the front and put the clamps back on the body of the
controller through the rear side of the panel. Firmly press the clamps in
order to fasten the controller to the panel.
The entire internal part of the controller can be removed from its
housing from the front of the panel, without needing to remove the
housing or clamps, or undo the connections. To extract the controller
from its housing, hold it from the front and pull.
Fig. 1 shows the electrical terminals of the controller.
Fig. 1 - Electrical connections of the controller
Thermocouples must be connected between pins 10 and 11. The
extension cable positive must be connected to terminal number 11.
Pt100 type sensors must be connected in 3 wires to terminals 10, 11
and 12. For Pt100 in 2 wires, terminals 11 and 12 must be
interconnected. For adequate compensation of the cable length, the
conductors of this cable must have the same section (gauge).
RESOURCES
INPUT
Table 1 shows the types of temperature sensors accepted by the
controller and the respective code used to configure the controller.
TYPE
CODE
RANGE
J
Tc J
Range: -110 to 950 ºC (-166 to 1742 ºF)
K
Tc H
Range: -150 to 1370 ºC (-238 to 2498 ºF)
T
Tc T
Range: -160 to 400 ºC (-256 to 752 ºF)
N
Tc N
Range: -270 to 1300 ºC (-454 to 2372 ºF)
R
Tc R
Range: -50 to 1760 ºC (-58 to 3200 ºF)
S
Tc S
Range: -50 to 1760 ºC (-58 to 3200 ºF)
B
Tc B
Range: 400 to 1800 ºC (752 to 3272 ºF)
E
Tc e
Range: -90 to 730 ºC (-130 to 1346 ºF)
Pt100
Pt
Range: -199.9 to 850 ºC (-328 to 1562 ºF)
Table 1 - Types of sensors accepted by the controller
CONTROL OUTPUTS AND ALARM (OUTA, OUTB, OUTC AND
OUTD)
The controller can have 2, 3 or 4 outputs, which can be configured as
control outputs or alarm outputs. These outputs are identified on the
rear panel of the controller as OUTA, OUTB, OUTC and OUTD.
The output type (control or alarm) is defined in the controller’s
configuration. The output configuration is individual and defined in the
ovt.A
, ovt.B, ovt.(, and ovt.d parameters respectively.
Output control is the output intended to control the process
temperature. It is possible to configure different outputs as the control
output, however, when the OUTD output is configured as the Analog
Output Control, the other control outputs are disabled.
The output control is always off when the “Erro” message is shown
on the controller’s display, signaling a process failure, defect in the
sensor or connection error.
Alarm outputs are used for signaling and/or safety of the process. For
outputs defined as alarm output, it is also necessary to define the alarm
function (see the Alarm Function Description item of this manual).
USB INTERFACE
The USB interface is used for CONFIGURING or MONITORING the
controller. The NConfig software must be used for the configuration. It
makes it possible to create, view, save and open configurations from
the equipment or files in your computer. The tool for saving and
opening configurations in files makes it possible to transfer
configurations between pieces of equipment and to make backup
copies. For specific models, the NConfig software also makes it
possible to update the firmware (internal software) of the controller
through the USB.
For MONITORING purposes you can use any supervisory software
(SCADA) or laboratory software that supports the MODBUS RTU
communication on a serial communications port. When connected to
the USB of a computer, the controller is recognized as a conventional
serial port (COM x). Use the NConfig software or consult the DEVICE
MANAGER in the Windows CONTROL PANEL to identify the COM port
that was assigned to the controller. Consult the mapping of the
MODBUS memory in the controller’s communications manual and the
Document Outline
- Controller N480D
- UNIVERSAL CONTROLLER – INSTRUCTIONS MANUAL – V5.0x
- SAFETY SUMMARY
- INSTALLATION
- RESOURCES
- configuration and operation
- PROTECTION OF CONFIGURATION
- TYPE OF ADOPTED PROGRAM
- PROGRAMS OF RAMP AND SOAK
- DETERMINATION OF PID PARAMETERs
- ALARMS FUNCTIONS
- PROBLEMS WITH THE CONTROLLER
- SPECIFICATIONS
- MODEL IDENTIFICATION
- SAFETY INFORMATION
- SUPPORT AND MAINTENANCE
- LIMITED WARRANTY AND LIMITATION OF LIABILITY