Nor-Lake Refrigeration Systems User Manual
Page 21
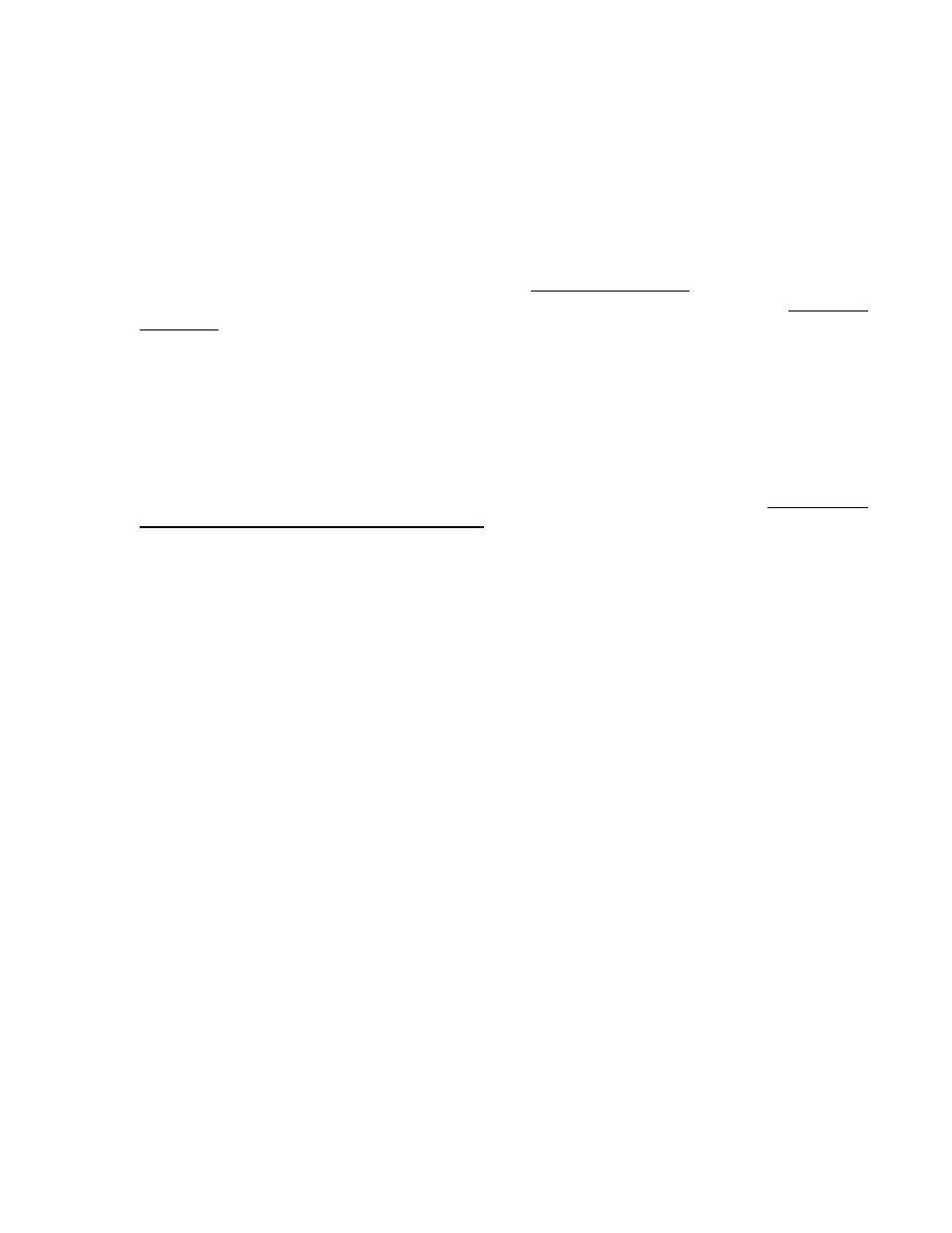
09/14 Rev. E 101628
21
4. System Refrigerant Charge: All systems must have a full head of liquid refrigerant at the
expansion valve to ensure proper operation of the expansion valve. A clear sight glass indicates
an adequate charge. Bubbles or flashing in the sight glass may indicate a shortage of
refrigerant, but flashing also can be caused by a liquid line restriction, hunting expansion valves,
sudden changes in condensing pressure, and rapid changes in the refrigeration load. If there is
doubt as to the refrigerant charge, check the liquid level in the receiver. There is no service
valve at the receiver.
Roof mounted condensing units equipped with low ambient head pressure controls will require a
great deal more refrigerant for low ambient head conditions, since the head pressure is normally
maintained by partially flooding the condenser. Too little refrigerant can result in lack of
refrigeration, loss of oil in the compressor, and overheating of the compressor. Too much
refrigerant can contribute to high discharge pressures, liquid refrigerant flooding, and liquid
slugging, with resulting compressor lubrication problems.
Special care should be taken in finding and repairing any leaks if a loss of refrigerant occurs.
5. System Control Settings: If there is a question as to the proper operations of the low-pressure
control or the oil pressure safety control, the pressure setting should be checked. The accuracy
of indicating scales on refrigeration pressure controls is not dependable, and if operation is
questionable, the control should be checked with a service technician’s gauges. Do not set the
low-pressure control below the recommended operating limits of the compressor. The cause of
any short cycling condition must be corrected. If the operation of an oil pressure safety control is
questionable, running a jumper connection across the pressure contacts to determine if the
control will trip should check it.
6. Liquid Line Filter Drier: Check the color code of the moisture indicator. A positive moisture
indication signals the filter dryer should be replaced. If the drier is frosted or if there is a
perceptible temperature change between the liquid line entering and leaving the drier, an
excessive pressure drop in the drier is indicated, and the drier or drier element should be
replaced.
7. Vibration Eliminators: If the wire braid cover on a metal vibration eliminator is starting to pull
out of the brazed end connectors, the vibration eliminator should be replaced to prevent
possible rupture, loss of refrigerant charge, and potential personal injury.
8. Capillary Tubes and Refrigerant Line: Check all capillary lines for wear and vibration. Tape or
support as necessary. Check refrigerant line supports and braces to make certain they are not
wearing or cutting the refrigerant line. Oil traces at flare nuts or valve connections indicate the
possibility of a refrigerant leak. Wipe clean and tighten the flare nut.
9. Liquid Refrigerant Control: Check for any indications of liquid refrigerant flooding such as
sweating or frosting of the compressor, rust on the suction service valve or compressor body,
tripping of the oil pressure safety control, audible slugging, or excessive foaming in the
crankcase. If there is any question as to liquid control, the operation of the system immediately
after a defrost cycle should be observed. Excessive sweating or frosting of the suction line
and/or compressor body must be corrected. Consult factory if compressor specifications are
required, but not available.
10. Electrical Control Panel: Check the electrical control panel to see that heaters or motor
protectors do not have jumpers. Look for burn marks on the cabinet that might indicate possible
shorts and check the contacts on any contactor.
11. Air Cooled Machine Room: Check the exhaust fan and fan motor, and lubricate if necessary.
Check operation of dampers and louvers, and lubricate as necessary. Run fan through an on
and off cycle by means of the thermostat.