Nor-Lake Refrigeration Systems User Manual
Page 20
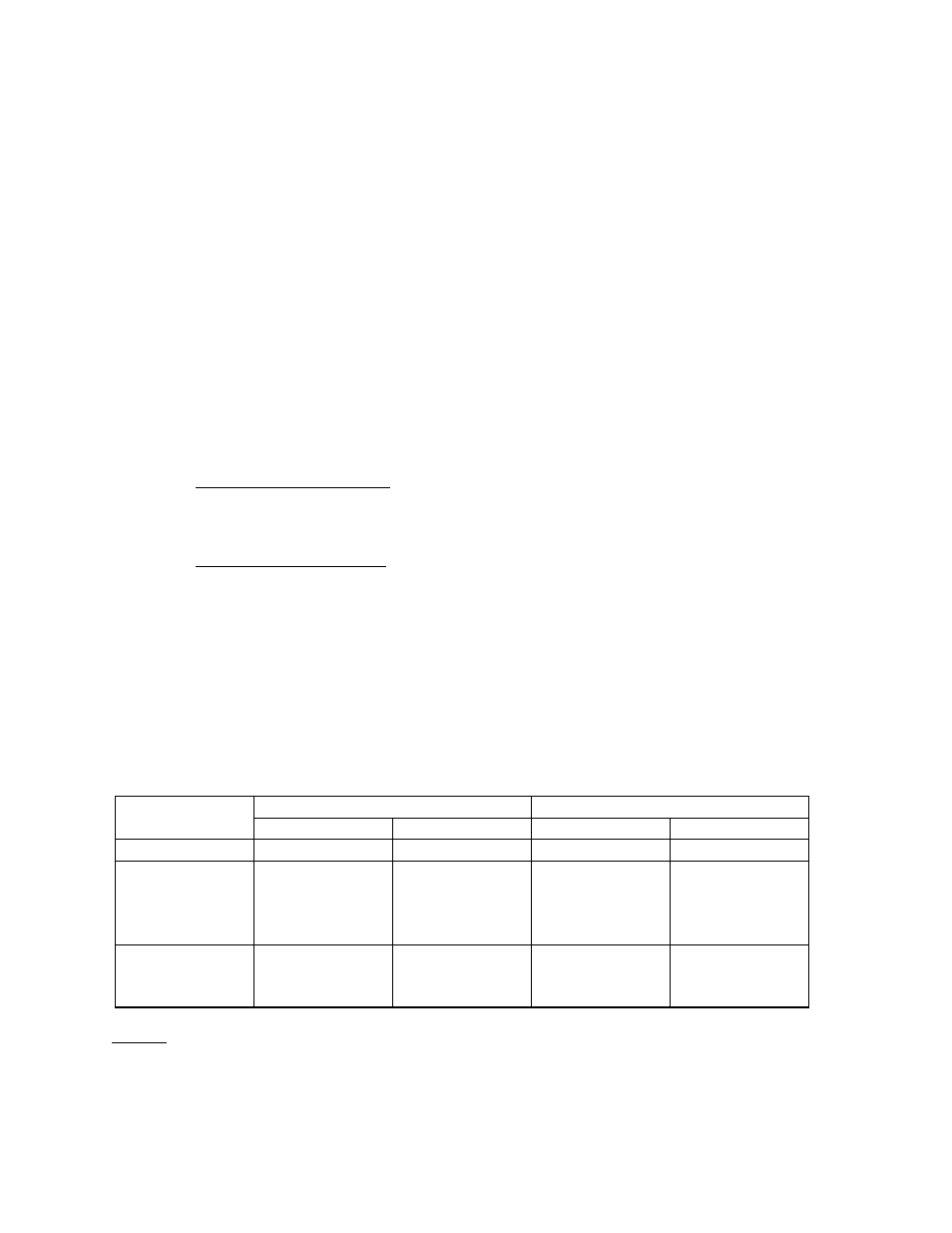
09/14 Rev. E 101628
20
1. Check with operation personnel: Always check with the operating personnel who are using
the equipment to see if there have been any reports of abnormal or erratic operation. Frequently
indications of abnormal operation may be observed by operating people who do not realize their
significance, and this information may never be given to the service personnel unless brought
out by specific questions concerning system operation. Ask particularly about trips of the oil
pressure safety control, or other safety devices.
2. Operating pressures and temperatures: If permanent gauges are available, check the
compressor suction and discharge pressures to be sure they are within the normal range for the
application and the temperature of the condensing medium. If there are any indications of
abnormal operation such as short cycling on pressure controls or excessive compressor
temperatures, use a gauge manifold to check the operating pressures on systems without
permanently installed gauges. If abnormal operating pressures are found, the cause must be
determined and the malfunction corrected. Check the compressor head temperature by touch.
An abnormally cool head can indicate a broken discharge valve, a blown or improper head
gasket, or inadequate compressor cooling.
3. Oil level and condition: On Copeland semi hermetic compressors, the oil level should be at or
slightly above the center of the sight glass. It should be kept in mind that some slight fluctuation
in oil level may occur during an operating cycle particularly before and after defrost periods. As
long as the oil level is maintained well within the sight glass such fluctuations are not harmful.
a. If the oil is black in color, the crankcase should be drained and the oil replaced. If
there has been a recent compressor failure on the system and the oil has an acid
odor, a fresh filter drier should be installed in the suction line and left in the line for a
period of 48 hours and then must be removed.
b. If the oil is still discolored, the oil and the suction line filter drier element should again
be changed. This procedure should be continued until the oil remains clean, odor
free, and the color approaches that of new oil. The filter drier element then may be
replaced with a permanent type suction line filter.
It is recommended that only mineral oil (MO) or Alkyl Benzene oil (AB) be used in compressors.
ONLY Polyol Ester oils (POE) used in R-404A compressors. DO NOT use POE oils in systems
if the system came pre-charged with mineral oil. Table 6 below references the appropriate oil for
the type of refrigerant used. This data is from Copeland specifications and is RIE recommended
oil for their product.
TABLE 6
Refrigerant
Lubricants
Type
Source
Preferred
Alternate
Ozone Depleting
HCFC
Many
MO
AB & MO
Interims
HCFC R-401A
Dupont/Allied
AB & MO
POE & MO
HCFC R-401B
Dupont/Allied
AB & MO
POE & MO
HCFC R-402A
Dupont
AB & MO
POE & MO
HCFC R-408A
Atochem
AB & MO
POE & MO
Non-Ozone
Depleting
HFC R-134a
Many
POE
HFC R-404A
Many
POE
HFC E-507
Allied
POE
Legend:
MO = Mineral Oil (3GS or Equivalent)
AB = Alkyl Benzene ( Zerol 200 TD)
POE = Mobil EAL™ Arctic 22 CC or ICI Emkarate™ RL32CF
POE & MO = Minimum 50% POE
AB & MO = Minimum 50% Alkyl Benzene (Shell 22-12)
Note: Shell 2212 is a 70/30 mixture of AB and MO. Zerol 200 TD is 100% AB
Note: Unless there are reasons for changing the oil, as outlined earlier in this section, the
refrigerant oil should not be changed. It does not deteriorate or wear out with normal usage.