Maintenance – Nor-Lake Refrigeration Systems User Manual
Page 19
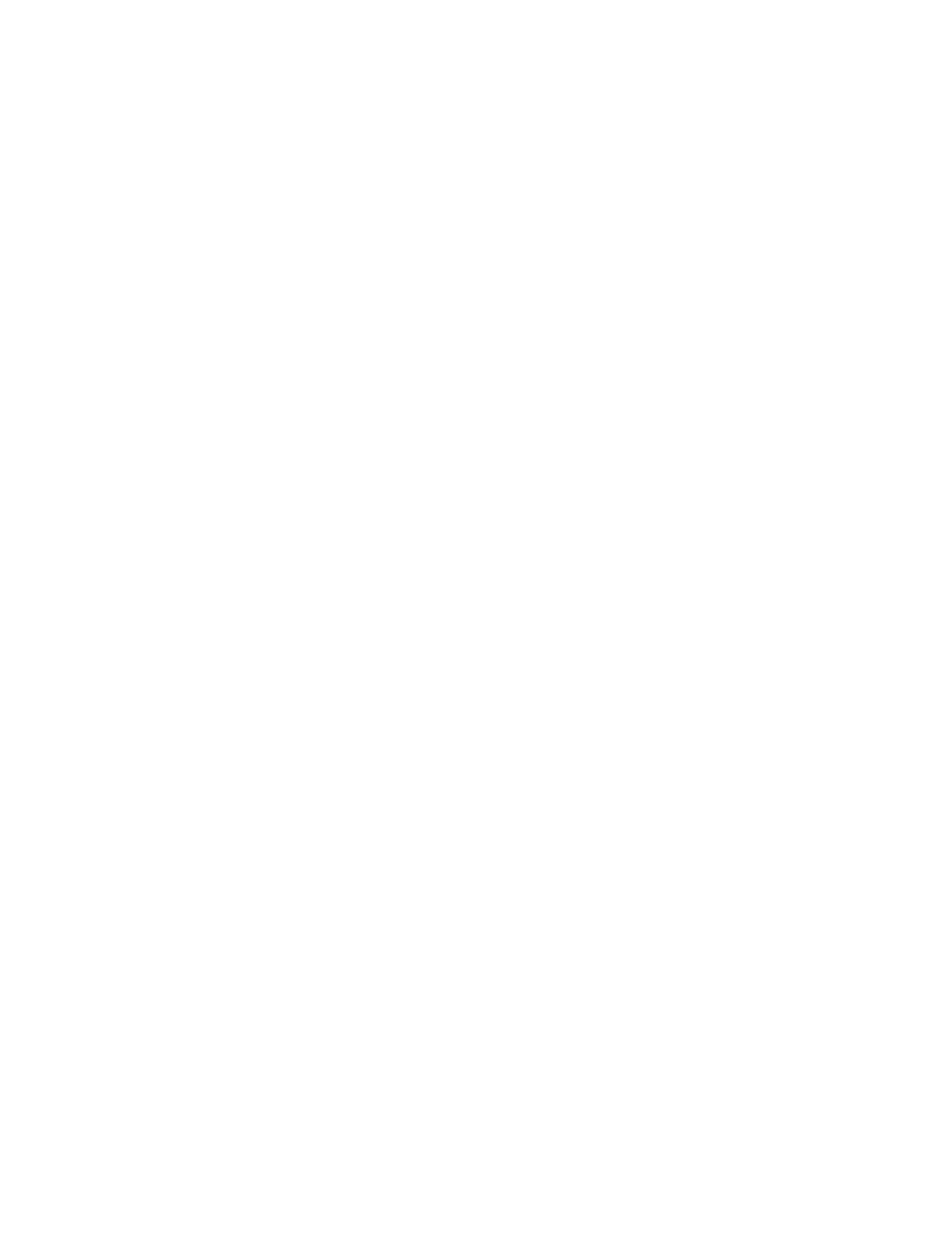
09/14 Rev. E 101628
19
defrost of any frost build up. When the room temperature control senses an increase in room
temperature above the cut in point, the control will close causing the liquid line solenoid to open
allowing refrigerant flow to the expansion valve with an increase in low side pressure. The low-
pressure control will close, starting the condensing unit for the next refrigeration cycle. Note: Some
high/medium temperature systems are provided with a time initiated defrost clock. Verify that all
wiring is per the wiring diagram provided with the system.
Low Temperature Systems:
Freezer rooms utilize the same room temperature control/pump down functions as high/medium
temperature rooms with the addition of time initiated temperature terminated electric defrost. The
defrost time switch initiates a defrost cycle according to times set as described under the Defrost
Time Switch section of this manual. The time switch, upon initiating a defrost cycle, causes the
liquid line solenoid to close, which in turn initiates a system pump down cycle. At the same time the
time switch stops the unit cooler fan(s) and energizes the evaporator defrost heaters. The defrost
heaters warm the evaporator until terminated by the defrost termination thermostat which senses
the evaporator temperature. Upon defrost termination the liquid line solenoid valve opens causing
the compressor to start when the low side pressure rises to the low-pressure control cut in point.
The unit cooler fan motor(s) will not start, however, until the evaporator has reached approximately
25°F to freeze any remaining water droplets to the evaporator fins. The fail-safe function on the
defrost time switch and/or the high limit temperature control in the unit cooler will terminate defrost if
there is a malfunction with the defrost termination thermostat.
MAINTENANCE
PREVENTIVE MAINTENANCE
How long does it take a compressor to wear out? It is almost impossible to answer that question
because seldom, if ever, does a compressor fail from wear due to normal operation. Almost
invariably a compressor failure results from malfunctions in either the refrigerant or electrical
system, or from system operation conditions beyond the limitations of the system design.
Just what does this mean in terms of preventive maintenance? In practically every case, indications
of a system malfunction are usually evident prior to the compressor failure. If the problem is
detected and corrected in time, a large percentage of compressor failures can be prevented. If the
inspector is alert and on the lookout for any indication that operation of the system is in an way
abnormal, a periodic maintenance inspection can be a major factor in maintenance cost reduction.
Inspections should be made at least three times per year, and more frequent inspection is
recommended during heavy usage periods or in a dirty environment.
Some factors that contribute to decreased unit efficiency and failure:
Excessive load
Improper air circulation
Excessive frost
Dirt on condenser coil
Short refrigerant charge
Clogged filter drier
Low head pressure
No winter control kit in low ambient temperature
Following is a summary of the major items to be checked.