Nor-Lake Refrigeration Systems User Manual
Page 16
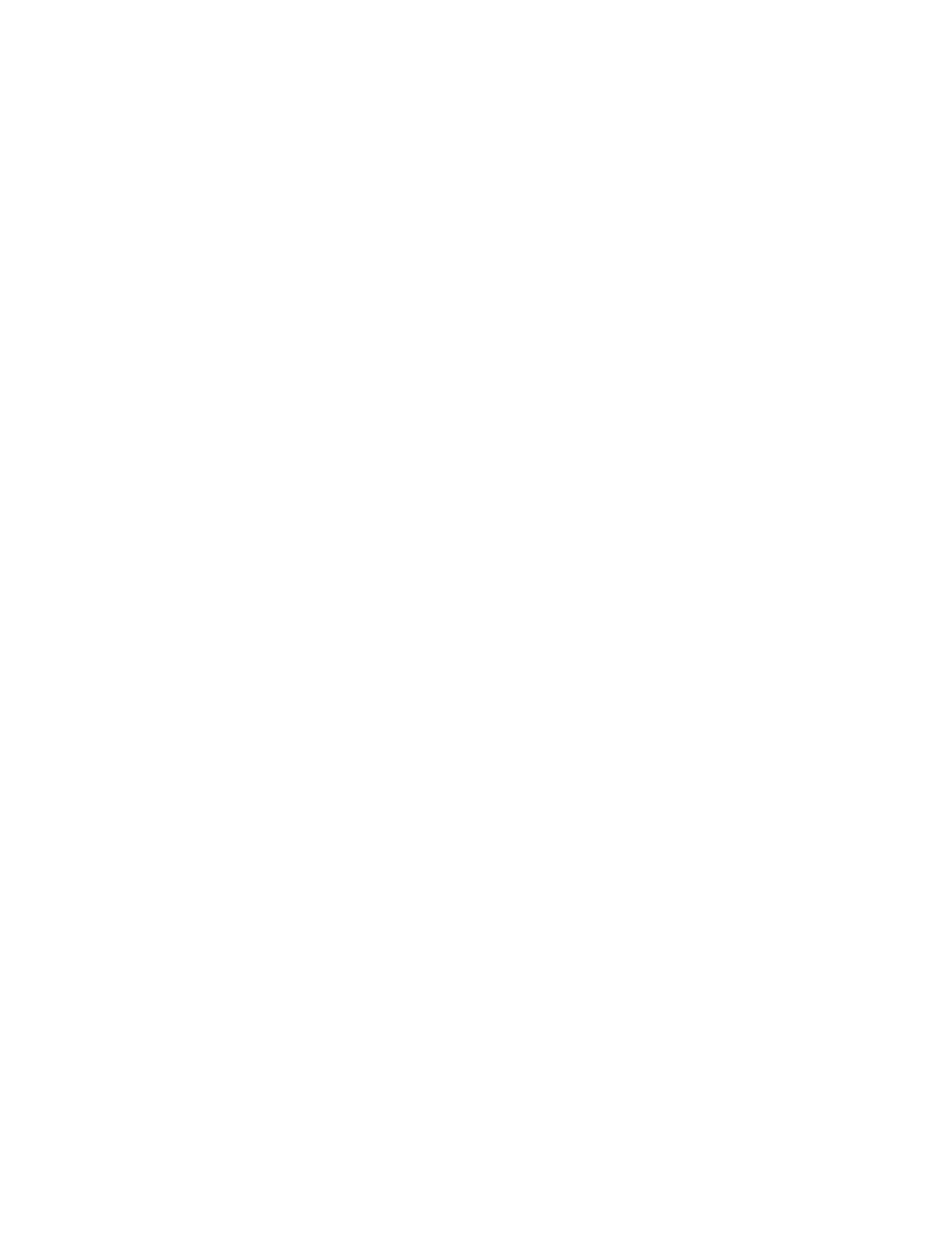
09/14 Rev. E 101628
16
Observing that the suction pressure drops and the discharge pressure rises when the compressor
is energized verifies the proper rotation. Additionally, if operated in reverse, the compressor makes
more noise and its current draw is substantially reduced compared to tabulated values.
If suction pressure does not drop and discharge pressure does not rise to normal levels, check the
power at the breaker. Reverse any two of the compressor power leads and reapply power to make
sure the compressor was not wired to run in the reverse direction.
Caution: Although operation of the scroll in the reverse direction for brief periods of time is not
harmful, continued operation will result in a failure due to insufficient lubrication of the drive bearing
and scroll galling.
All three-phase compressors are wired identically internally. Once the correct phasing is determined
for a specific system or installation, connecting properly phased power leads to the same Fusite
terminals will maintain proper rotation.
Brief power interruptions
Brief power interruptions, less than 1/2 second, may result in powered reverse rotation of single-
phase scroll compressors. High-pressure discharge gas expands backwards through the scrolls at
power interruption, causing the scroll to orbit in the reverse direction. If power is reapplied while this
reversal is occurring, the compressor may continue to run noisily in the reverse direction for several
minutes until the compressor’s internal protector trips. This does not have a negative impact on
durability. The internal protector will automatically reset once the internal temperature has returned
to a safe operating range for the compressor. When the protector resets the compressor will start
and run normally.
1. Start the system and finish charging until the sight glass indicates a full charge, the sight glass
should be clear. Care should be taken so as not to overcharge the system at this point. When
adding refrigerant to an operating system, it is necessary to add the refrigerant through the
compressor suction service valve. Because the refrigerant leaving the refrigerant cylinder must
be in liquid phase, care must be exercised to avoid damage to the compressor. It is suggested
that a sight glass be connected between the charging hose and the compressor suction service
valve. This will permit adjustment to the cylinder hand valve so that liquid can leave the cylinder
while allowing vapor to enter the compressor.
Rapid charging only on the suction side of a scroll equipped system or condensing unit can
occasionally result in a temporary no-start condition for the compressor. The reason for this is
that if the flanks of the compressor happen to be in a sealed position, rapid pressurization of the
low side without opposing high side pressure can cause the scrolls to seal axially. As a result,
until the pressures eventually equalize, the scrolls can be held tightly together, preventing
rotation. The best way to avoid this situation is to charge on both the high and low side
simultaneously at a rate that does not result in axial loading of the scrolls. The maximum
charging rate can be determined through simple tests.
2. During start-up, keep a continual check on high and low side pressures as well as compressor
amperage. Rated load amps are shown on the nameplate.
3. Outdoor condensing units which are equipped with a condenser flooding type head pressure
control valve for low ambient operation must have the correct refrigerant charge added at initial
start-up in order for the system to operate properly in all seasons. The extra winter charge, as
calculated below, should be weighed into the receiver. To determine the extra charge required,
calculate the total length of tubing in the condenser including the equivalent length for return
bends. See Table 4. Multiply the total length in feet by the number of pounds per 100 feet for the
proper refrigerant and condenser tube size from Table 4.