Nor-Lake Refrigeration Systems User Manual
Page 14
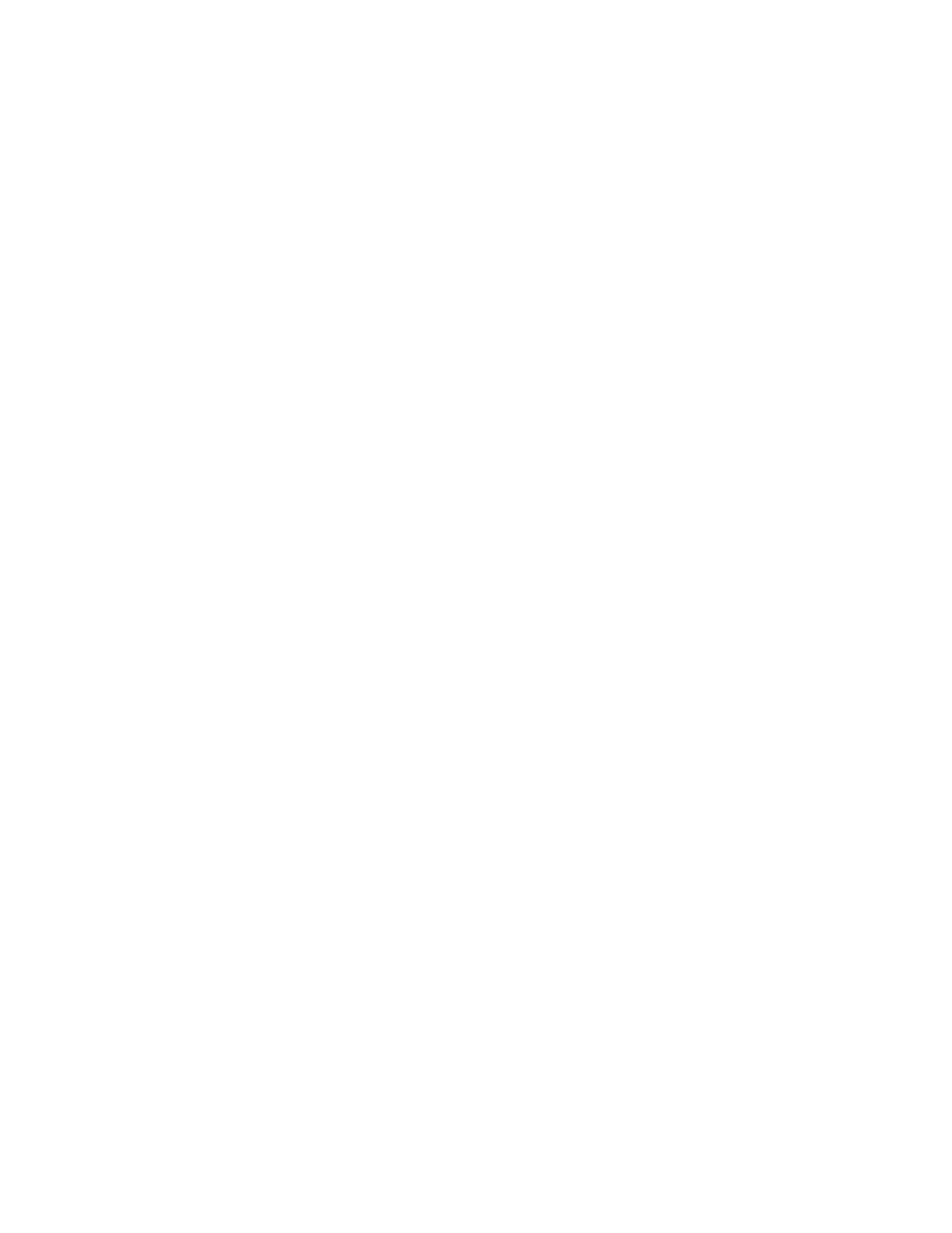
09/14 Rev. E 101628
14
f.
A “P” trap must be provided in the drain line outside the refrigerated space to prevent warm
moist air from being drawn into the unit cooler through the drain line. Note: When plumbing a
combination cooler/freezer, each compartment should be plumbed separately.
g. The drain line must be run to an open drain, not directly to the sewer system.
h. An electrical heating cable or heat tape must be wrapped on the entire drain line inside a
freezer, extending through the freezer wall up to and including the “P” trap. A heat input of 20
watts per lineal foot of drain line for 0°F and 30 watts per lineal foot for
–20°F will be
satisfactory. The heater must be energized continuously.
i. The entire length of heated drain line exposed within the refrigerated space must be insulated
with a suitable material, a minimum 1/2” wall thickness.
j. Condensate drain lines outside the refrigerated space that are exposed to below freezing
temperatures during the winter must be treated as in letters ”h” and “i” above.
LEAK TESTING
1. After all refrigerant lines are connected; the system must be leaked tested at a minimum of 150
psig with the compressor suction and discharge valves closed, and all other valves in the
system open. If local codes require higher test pressures, such codes must be complied with.
2. Sufficient liquid refrigerant of the type to be used in the system must be charged to raise the
pressure to 20 psig and dry nitrogen added to obtain the desired test pressure.
3. Leak test all joints and fittings with an electronic leak detector. If any leaks are found, isolate the
defective area, discharge the gas using proper reclamation techniques and repair the leaks
4. Repeat the leak test to prove the entire system is leak free.
5. When the testing is complete, release all pressure using proper reclamation techniques.
EVACUATION
Caution: Do not use the refrigeration compressor to evacuate the system. Do not start the
compressor while it is in a vacuum.
1. A good, deep vacuum pump should be connected to both the low and high side evacuation
valves with copper tube or high vacuum hoses, 1/4” ID minimum. If the compressor has service
valves, they should remain closed. A deep vacuum gauge capable of registering pressure in
microns should be attached to the system for pressure readings.
2. A shut off valve between the gauge connection and vacuum pump should be provided to allow
the system pressure to be checked after evacuation. Do not turn off the vacuum pump when
connected to an evacuated system before closing the shut off valve.
3. The vacuum pump should be operated until a pressure of 1,500 microns absolute pressure is
reached, at which time the vacuum should be broken with the refrigerant to be used in the
system through a drier until the system pressure rises above 0 psig.
4. Repeat this operation a second time.
5. Open the compressor service valves and evacuate the entire system to 200 microns absolute
pressure. Raise the pressure to 2 psig with the refrigerant and remove the vacuum pump.
Note: EPA regulations are constantly being updated. To ensure that your procedure is
proper, follow current regulations.