Pid tuning explanations, Auto-tune, Initiate auto-tune – Red Lion PAX2C User Manual
Page 50: Derivative time, Primary/alternate pid values
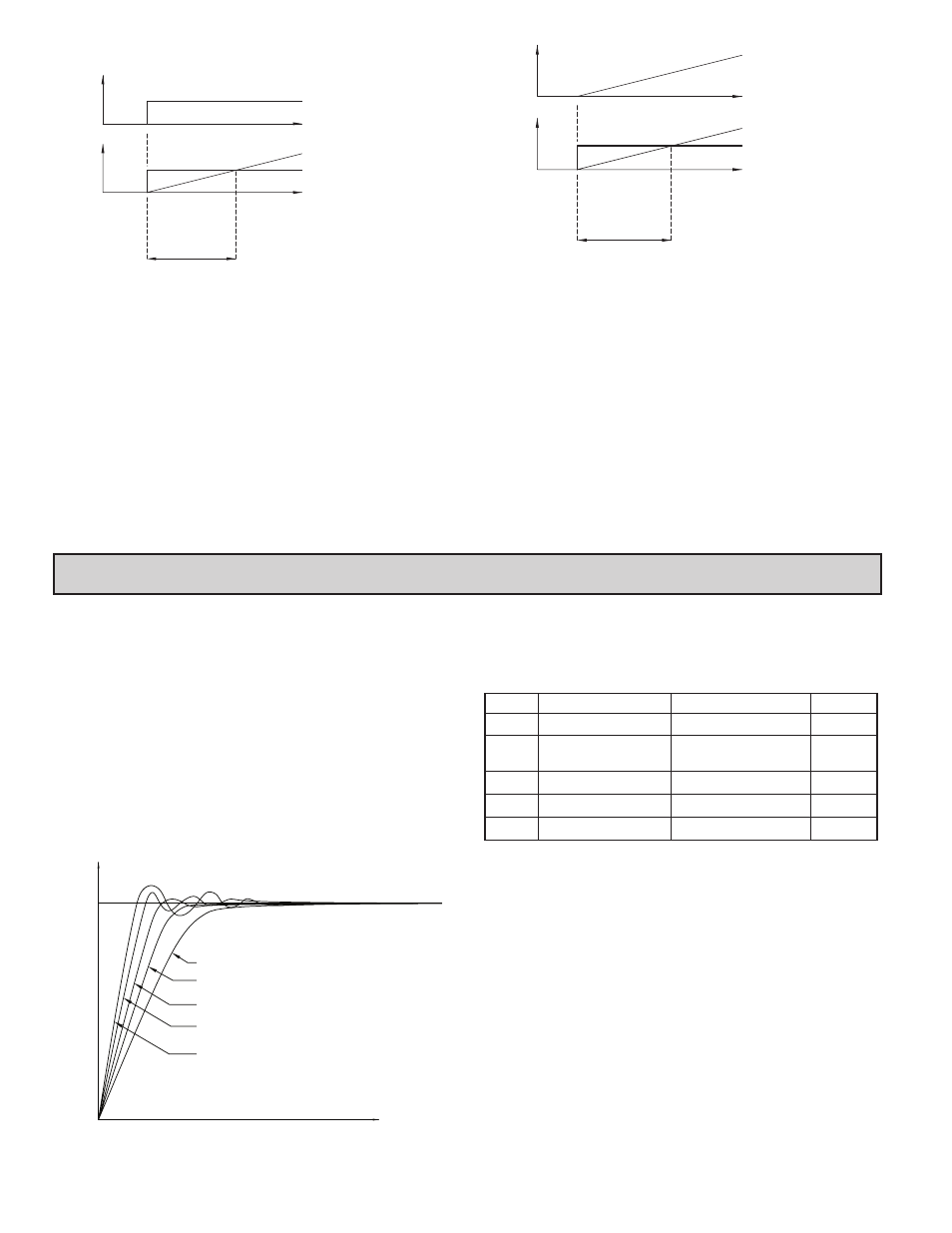
50
AUTO-TUNE
Auto-Tune is a user-initiated function where the controller automatically
determines the Proportional Band, Integral Time, Derivative Time, Digital
Filter, Control Ouput Dampening Time, and Relative Gain (Heat/Cool) values
based upon the process characteristics. The Auto-Tune operation cycles the
controlling output(s) at a control point three-quarters of the distance between the
present process value and the setpoint. The nature of these oscillations
determines the settings for the controller’s parameters.
Prior to initiating Auto-Tune, it is important that the controller and system be
verified. (This can be accomplished in On/Off Control or Manual Control
Mode.) If there is a wiring, system or controller problem, Auto-Tune may give
incorrect tuning or may never finish. Auto-Tune may be initiated at start-up,
from setpoint or at any other process point. However, insure normal process
conditions (example: minimize unusual external load disturbances) as they will
have an effect on the PID calculations.
AUTO-TUNING CODE FIGURE
INITIATE AUTO-TUNE
Below are the parameters and factory settings that affect Auto-Tune
calculations. If changes are needed, then they must be made before starting
Auto-Tune. Please note that it is necessary to configure the input and control
outputs prior to initiating auto-tune.
DISPLAY PARAMETER
FACTORY SETTING
MENU
FLtr
Digital Filtering
1.0
INPt
CHYS
On/Off Control Hysteresis 2 (Temperature Mode)
0.2
(Process Mode)
Pid
tCod
Auto-Tune Code
2
Pid
dEAd
Deadband
0.0
Pid
tUNE
Auto-Tune Access
LOC
Pid
1. Enter the Setpoint value via the PID Menu or via the Display, Parameter or
Hidden Menu Loop Menu (if enabled).
2. Initiate Auto-Tune by changing Auto-Tune tUNE to YES via the PID Menu or
via the Display, Parameter or Hidden Menu Loop Menu (if enabled).
DERIVATIVE TIME
Derivative time is defined as the time, in seconds, in which the output due to
proportional action alone equals the output due to derivative action with a
ramping process error. As long as a ramping error exists, the derivative action is
“repeated” by proportional action every derivative time. The units of derivative
time are seconds per repeat.
Derivative action is used to shorten the process response time and helps to
stabilize the process by providing an output based on the rate of change of the
process. In effect, derivative action anticipates where the process is headed and
changes the output before it actually “arrives”. Increasing the derivative time
helps to stabilize the response, but too much derivative time coupled with noisy
signal processes, may cause the output to fluctuate too greatly, yielding poor
control. None or too little derivative action usually results in decreased stability
with higher overshoots. No derivative action usually requires a wider proportional
and slower integral times to maintain the same degree of stability as with
derivative action. Derivative action is disabled by setting the time to zero.
PRIMARY/ALTERNATE PID VALUES
The PAX2C incorporates two different groups of PID parameters in memory.
These are designated as the Primary (Pri) and Alternate (Alt) PID values. It is
possible to toggle between these values using the PID Selection parameter
which is available in the PID configuration menu. This functionality (PSEL) is
also available via the user inputs, function keys or Line 2 user function.
The Active PID parameters reflect the PID values that are selected via the
PSEL
parameter. If a change is made to an active PID value, such as a user change
or after an Auto-tune, the values will automatically be copied into the Primary
or Alternate group depending on which group is selected by the PSEL parameter.
TIME
TIME
INTEGRAL
TIME
DEVIATION
OUTPUT
POWER (%)
INTEGRAL OUTPUT
PROPORTIONAL OUTPUT
NOTE: TOTAL OUTPUT POWER IS CALCULATED
BASED ON THE THREE PID SETTINGS.
TIME
DERIVATIVE
TIME
TIME
DEVIATION
OUTPUT
POWER (%)
DERIVATIVE OUTPUT
PROPORTIONAL OUTPUT
NOTE: TOTAL OUTPUT POWER IS CALCULATED
BASED ON THE THREE PID SETTINGS.
Note: The Proportional band shift due to integral action
may itself be “reset” by temporarily setting the controller
to the on/off control mode (proportional band = 0).
TIME
TEMPERATURE
SP
0
1
2
3
4
TYPICAL RESPONSE CURVES
WITH AUTOTUNE DAMPENING
CODES 0 TO 4.
pid Tuning eXplanaTiOns